Дефектация и сортировка
Дефектацию деталей проводят с целью определения их технического состояния:
а) деформацию и износ поверхностей;
б) целость материала;
в) изменение свойств и характеристик рабочих поверхностей;
г) сохранность формы.
Операции дефектации:
1. Внешним осмотром. Невооруженным глазом или с помощью лупы, проверкой на ощупь, простукиванием выявляют: трещины, забоины, риски, обломы, пробоины, вмятины, задиры, коррозию, ослабление плотности посадки.
2. Используя универсальный или специальный измерительный инструмент, определяют геометрические параметры деталей.
3 С помощью специальных приборов определяют скрытые дефекты К специальным приборам и методам относят ультразвуковую, гамма -, рентгеновскую, магнитную, цветную и т.д. дефектоскопию.
Детонационное нанесение порошковых покрытий
Способ основан на использовании энергии детонации в газах. При этом способе металлический или металлизированный порошок наносится взрывом кислородо-ацетиленовой смеси, обеспечивающим скорость движения частиц 800 - 900 м/с. Прочное соединение частиц с восстанавливаемой поверхностью обеспечивается микросваркой.
Образование газовопорошковой смеси, ее взрыв осуществляется в специальной камере, куда порошок доставляется струей азота.
В качестве материалов порошков применяют: а) карбиды - вольфрама и титана; б) оксиды - алюминия и хрома; в) металлы: хром, кобальт, титан, вольфрам.
При каждом взрыве, длящемся примерно 0,23 секунды, образуется слой толщиной примерно 0,007 мм. Многослойные покрытия, толщиной 0,02 - 0,4 мм получают, многократно повторяя взрывы.
Покрытие обладает высокой твердостью и износостойкостью, малой пористостью (менее 1 %), высокой прочностью сцепления с основным металлом.
Преимуществом способа детонационного нанесения порошков является невысокая температура нагрева металла-основы (менее 250 °С), что позволяет наносить слой порошка на закаленную поверхность без риска ее отпуска.
Технологические возможности способа позволяют наносить покрытия на цилиндрические внешние поверхности диаметром до 1000 мм и внутренние диаметром более 15 мм, а также на плоские поверхности сложной конфигурации.
Примером использования данного способа может служить восстановление детонационным покрытием порошком ВК - 15 закаленной поверхности гибочного штампа из стали Х12М, имеющей твердость НRC -57 - 61.
Древесина
Применительно к данному материалу было бы более правильно рассмотреть переработку и использование отходов образующихся при выработке пиломатериалов. Отходы - это та часть сырья, которая не попадает в основную продукцию. Величина отходов при переработке древесины зависит: 1) от степени раскроя бревен; 2) назначения и степени обрезки пиломатериалов; 3) толщины пил; 4) соблюдения технологии. От объема распиливаемого материала отходы составляют, %:
- горбыли - 6 - 10;
- рейки - 10 - 15;
- концы досок - 2 - 4;
- опилки - 10 -12;
- вырезка брака -2-3.
В раскройных цехах при раскрое досок образуются отходы, %:
- опилки - 7 - 10;
- обрезки - 10 - 25 (вырезка брака, некратные остатки).
В строгальных цехах отходы составляют 12-20 % от объема перерабатываемого материала.
В результате переработки отходов древесины получают следующие продукты:
1) целюлозу; 2) бумагу, 3) картон; 4) спирты; 5) фурфурол; 6) кормовые дрожжи; 7) глицерин; 8) фенолы; 9) смолу; 10) сажу; 11) уголь; 12) ацетон; 13) витамины; 14) вазелин; 15) лаки; 16) уксусную кислоту; 17) ДВП; 18) ДСП; 19) фибролитовые плиты; 20) арболит, 21) канифоль; 22) скипидар; 23) древесную муку и др.
В технологических процессах получения перечисленных продуктов древесину измельчают до нужных фракций. Для этого кусковые отходы лесопиления (горбыли, рейки и обрезки) перерабатывают в технологическую щепу (сопутствующая продукция лесопильного производства).
Мягкие отходы (опилки и стружку) используют для хозяйственных и промышленных целей.1.Опилками полируют и чистят мелкие металлические и проволочные изделия, алюминиевую посуду, листовой алюминий, меха, кожу. 2. Применяют при производстве пористого кирпича. 3. Опилки и стружка являются хорошим поглотителем влаги при уборке мест общественного пользования. 4. В смеси со щепой опилки используют для варки целлюлозы в гидролизном производстве для получения спирта и кормовых дрожжей. 5. После размола опилок на специальных мельницах получают древесную муку, используемую при производстве пластмасс, взрывчатых веществ, линолеума.
Кора используется для изготовления: а) органических удобрений; б) наполнителя для строительного плитного материала.
В крайнем случае, отходы древесины могут быть использованы как топливо.
Как уже отмечалось, при переработке крупных отходов древесины основным этапом является получение технологические щепы. Технологическая щепа производится согласно ГОСТ 15815-84. ГОСТ предусматривает недопустимость в щепе примесей: коры, гнили, обугленных частиц, металлических включений, песка.
Кусковые отходы измельчают на рубильных машинах, барабанных или дисковых (барабанные машины дают щепу низкого качества, используемую в гидролизном производстве и идущую на топливо; дисковые рубильные машины обеспечивают более высокое качество щепы).
Затем щепу сортируют по размерам на установках вибрационного или гирационного типа. Крупная щепа отдельным конвейером направляется на повторное дробление, кондиционная - на отгрузку потребителям, а мелочь и опилки - в бункера для опилок.
Крупные горбыли и рейки перерабатывают на обапол (пиломатериал, полученный из боковой части бревна) и мелкую пилопродукцию. Обапол изготавливают, в основном, из соснового и елового горбыля. Технология выработки обапола включает одну операцию - торцовку на маятниковых станках. Основным потребителем этой продукции является горнодобывающая промышленность (крепление шахтных выработок).
Крупные отходы лесопиления перерабатывают на мелкую пилопродукцию: тарную дощечку, штакетник, штукатурную и кровельную дрань.
Физико - химические основы наплавки
Для возникновения сцепления между наплавляемым металлом и металлом-основой необходимо, прежде всего, чтобы атомы жидкого металла вступили в непосредственный контакт с поверхностными атомами твердого металла, т.е. чтобы произошло смачивание.
Если на чистую металлическую поверхность поместить каплю жидкого металла, то в зависимости от склонности данной пары к смачиванию, эта капля или останется на поверхности в виде сферы или растечется по ней (Рис.6). Растекание происходит не бесконечно, а до определенного предела пока она не примет форму сегмента, образующего с основанием краевой угол смачивания -q.
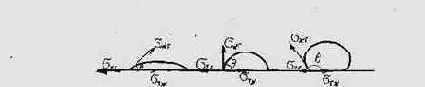
Рис.6
Рассмотрим равновесие капли на твердой поверхности в зависимости от соотношения сил поверхностного натяжения. После прекращения растекания условие равновесия на металлической поверхности:
sтг - sтж - sжгcosq = 0 ,
где - sтг , sтж , sжг - поверхностное натяжение, соответственно, на границе раздела твердое тело - газ, твердое тело - жидкость, жидкость - газ.
После преобразования имеем:
cosq =

Анализ последнего выражения показывает, что:
1) если sтг > sтж , то угол q - острый и имеет место хорошее смачивание;
2) если sтг < sтж , то угол q - тупой и смачивание плохое,
3) с понижением величины sтг во всех случаях наблюдается уменьшение величины cosq и увеличение величины угла q, т.е. смачивание ухудшается;
4) с понижением величины sтж во всех случаях величина cosq увеличивается, а угол q уменьшается, т.е. смачивание улучшается;
5) изменение sжг влияет двояко:
а) при sтг - sтж >0 понижение величины sжг приводит к увеличению cosq и уменьшению q в пределах 90о - 0°, т.е. наблюдается улучшение смачивания;
б) при sтг - sтж < 0 понижение величины sжг приводит к уменьшению cosq и увеличению q в пределах 90° - 180°, т.е. наблюдается ухудшение смачивания
Вывод. Если q >0, т.е. q < 90°, то расплав хорошо смачивает поверхность металла. Если cosq < 0, т.е. q >90°, то расплав плохо смачивает поверхность металла.
При q = 0° имеет место один из крайних случаев - полное смачивание. При q =180° наблюдается второй крайний случай - полное отсутствие смачивания.
Смачивание поверхности твердого металла расплавом можно улучшить изменением значений поверхностных натяжений. Величина поверхностного натяжения как твердого так и жидкого металлов сильно зависит от характера и свойств той среды, на границе с которой определяется эта величина. Поэтому смачивание каждой конкретной пары металлов можно улучшить, взяв в качестве третьей среды, участвующей в процессе смачивания, не обычную атмосферу, а расплав солей - флюсов.
Существует несколько гипотез влияния флюсов на смачивание. Первая - гипотеза об очистке поверхности металла от окислов и загрязнений. Вторая - гипотеза об уменьшении поверхностного натяжения расплава металла. Третья - гипотеза об электромеханическом выделении на поверхности твердого металла тонкого слоя металла одноименного металлу расплава.
Требования к флюсам. 1. Хорошее смачивание поверхности твердого металла. 2. Улучшение смачивания твердого металла жидким. 3. Хорошо растворять или разрушать пленки окислов твердого и жидкого металлов. 4. Защищать наплавляемую поверхность от вторичного окисления при высоких температурах. 5. Температура плавления флюса должна быть меньше температуры плавления жидкого металла. 6. Продукты взаимодействия флюса с окислами должны иметь низкую температуру плавления и быть нетоксичными. 7. Флюсы не должны вызывать окисление, коррозию, обезуглероживание твердого металла. 8. Флюсы должны иметь высокую жидкотекучесть, чтобы легко смываться с твердой поверхности.
Для железоуглеродистых сплавов рекомендуются флюсы на основе буры (тетрабората натрия – Na2B4O7 ) и /или борного ангидрида – В2Оз. Для улучшения свойств флюсов вводятся активные добавки: КF, LiCOз, К2СО3, Na2СО3, К2ZгF6.
Для нанесения на поверхность твердого металла и удержания на этой поверхности применяются связки, эмаль ЭВ-300-60М, стеарат алюминия, полистирол, толуол, лак №302 и др.
Флюсы
От состава и свойств флюса зависят: а) устойчивость дуги; 6) плотность и механические свойства наплавленного металла; в) отделимость шлаковой корки; г) предотвращение разбрызгивания металла при наплавке; д) дегазация сварочной ванны.
Капли расплавленного металла перемешиваются с расплавленным флюсом, а затем отделяются от него. При этом происходит химическое взаимодействие: часть углерода, хрома, ванадия и других элементов, содержащихся в металле, окисляется и переходит в шлак. Если флюс содержит большое количество марганца и кремния, то эти элементы могут восстанавливаться и переходить из шлака в металл. Таким образом, состав флюса оказывает большое влияние на химический состав наплавленного металла.
Флюсы можно классифицировать по ряду признаков:
1. По способу изготовления.
2. По назначению.
3. По химическому составу.
4. По размеру и составу частиц.
Наиболее часто их подразделяют по способу изготовления. По этому признаку различают флюсы: а) плавленные; б) керамические.
Плавленные флюсы изготавливают путем плавления шихты в электрических или пламенных печах с последующим гранулированием расплава мокрым или сухим способом. Их подразделяют на четыре группы.
К первой группе относят высококремнистые марганцевые флюсы (АН-348А, АН-348АМ, ОЦС-45, АН-60). Их применяют при наплавке низкоуглеродистых, среднеуглеродистых и низколегированных сталей.
Ко второй группе относятся низкокремнистые безмарганцевые флюсы (АН-20С, АН-20СМ, АН-22, АН-26, АН-30, 48-ОФ-6). Эти флюсы применяются при наплавке легированной и высоколегированной стали с небольшим содержанием марганца.
К третьей группе относят низкокремнистые марганцевые флюсы (АН-10, АН-26С и др.). Их применяют преимущественно при наплавке сталей и сплавов с высоким содержанием марганца.
К четвертой группе относят специальные флюсы (АН-25, АН-8 и др.). Применяют при электрошлаковой наплавке, при наплавке цветных сплавов. При наплавке жидким металлом применяют плавленые флюсы АНШ-100 и АНШ-200.
По строению зерен (частиц) различают стекловидные, пемзовидные и кристаллические плавленные флюсы. Стекловидный флюс состоит из прозрачных зерен различной окраски. Зерна пемзовидного флюса пористы и непрозрачны. Кристаллический флюс имеет зерна кристаллического строения. Флюс может быть тонкозернистым, мелкозернистым, среднезернистым и крупнозернистым. В первом случае величина зерен не превышает 0,8 мм; в последнем - достигает 5 мм.
Керамические флюсы изготавливают путем замешивания на жидком стекле смеси тонкоразмолотых ферросплавов, химикатов и минералов, измельчения тестообразной массы, сушки и прокалки крупки. Исходными материалами для керамических флюсов являются марганцевая руда, титановый концентрат, кварцевый песок, мрамор, плавиковый шпат, ферросплавы и др.
Формирование переходной зоны при наплавке
Формирование переходной зоны при наплавке, независимо от технологии ее осуществления, связано, в первую очередь, с процессами перераспределения атомов твердого и жидкого металлов. Смачивание твердой поверхности жидким металлом сопровождается:
1) растворением твердого метала в жидком. Имеет место в том случае, когда наиболее быстро идет процесс растворения твердого металла в жидком или когда жидкий металл длительное время контактирует с твердым не кристаллизуясь.
2) атомная диффузия составляющих жидкий металл элементов в твердый. Имеет место, в том случае, когда металл находящийся в жидком состоянии, хорошо растворим в твердом.
3) реакция (реактивная диффузия) с образованием слоя интерметаллического соединения. Имеет место, в том случае, жидкий и твердый металл образуют между собой систему с интерметаллическим соединением.
Теоретически распределение легирующих элементов в зоне сплавления зависит от формы диаграммы состояния.
Система с полной взаимной растворимостью компонентов в твердом состоянии. Металлы, образующие системы с неограниченной взаимной растворимостью компонентов как в жидком, так и в твердом состоянии, легко диффундируют друг в друга с образованием твердых растворов переменной концентрации. Если два таких металла соединить между собой в твердом состоянии, нагреть до температуры, лежащей несколько ниже температуры плавления более легкоплавкого компонента М1 и выдержать при этой температуре достаточно долго, то в результате процесса взаимной атомной диффузии по обе стороны от плоскости соединения образуются твердые растворы с плавно изменяющейся концентрацией по кривой mcn (Рис. 7, а).
Схема эвтектического типа с ограниченной растворимостью компонентов в твердом состоянии. Металлы, образующие системы простого эвтектического типа с ограниченной растворимостью компонентов в твердом состоянии способны диффундировать друг в друга только в пределах взаимной их растворимости. При взаимной диффузии таких компонентов в твердом состоянии (при нагреве ниже эвтектической температуры - tе) по обе стороны от плоскости соединения образуются твердые растворы, причем максимальные концентрации твердых растворов M1 в М2
(b) и М2 в М1 (a) будут соответственно равны с2 и с1 ( рис.7, б ).
В отличие от системы с неограниченной растворимостью компонентов в твердом состоянии в данном случае на границе раздела будет наблюдаться скачок концентрации с2 – с1. Общее распределение концентрации по сечению шлифа выразится кривой mc1c2n. При сильном конвекционном или механическом перемешивании наплавляемого металла, обеспечивающем равномерность концентрации по всей массе жидкого металла, закристаллизовавшийся сплав может иметь среднюю концентрацию.
Система без растворимости компонентов в твердом состоянии. Металлы, не образующие твердых растворов и интерметаллических соединений не могут диффундировать друг в друга в твердом состоянии. Поэтому на границе между ними будет скачок концентрации от М1
до М2. Если такие металлы образуют простую эвтектическую систему ( рис.7, в.), то при быстром отводе растворяющихся в расплаве атомов от поверхности раздела возможен случай, когда при охлаждении выпадут первичные кристаллы М1 и эвтектика М1 + М2. Распределение концентраций по шлифу при этом выразится линией nc1m. В зоне соединения таких металлов нельзя обнаружить каких - либо новых структурных образований.
Система металлов, образующих ряд интерметаллических соединений. При взаимодействии твердого и жидкого металлов, которые в соответствии с диаграммой состояния могут образовывать химические соединения, в промежуточной зоне неизбежно возникают эти соединения. В общем случае в зоне соединения могут присутствовать все фазы, образования которых возможно по диаграмме состояния.
Проникновение атомов металла М1 за счет диффузионной подвижности в металл М2
вызовет образование слоя твердого раствора e (рис.7, г); концентрация компонента М1 в М2 при этом будет меняться по кривой М2с6. Непосредственно к слою твердого раствора e прилегает слой g, представляющий собой твердый раствор на базе интерметаллического соединения. Внутри слоя g концентрация, как это следует из диаграммы состояния, не остается постоянной, а изменяется по кривой c5c4. Слой фазы g граничит со слоем b.Концентрация на границе соприкосновения b и g скачком меняется от c4 до c3. Внутри слоя b концентрация меняется по кривой c3c2, и т.д.
Гальванические покрытия
Для восстановления деталей наиболее часто применяют хромирование и железнение.
Хромирование применяют для: 1) восстановления размеров изношенных деталей; 2) повышения износостойкости и прирабатываемости; 3) обеспечения хороших условий трения со смазкой; 4) декоративных целей.
Железнение (осталивание) применяют, главным образом, для восстановления размеров деталей машин. Твердость электролитического железа очень высока. Детали после железнения можно подвергать термической обработке.
Газопламенное нанесение порошков
Основа процесса газопламенного нанесения порошков заключается в пластификации порошка в высокотемпературном источнике тепла, например, ацетилено-кислородном пламени и нанесении его газовым потоком на предварительно подготовленную изношенную поверхность.
Преимущества данного способа восстановления: а) высокая производительность; б) локальность, т.е. выборочное нанесение материала только на изношенную поверхность; в) незначительное воздействие на подложку; г) отсутствие ограничений на сочетание материалов.
В зависимости от назначения и материала детали, условий ее эксплуатации используют следующие методы газопламенного нанесения порошковых материалов:
1. Газопламенное напыление порошка без последующего оплавления. Используется для восстановления износов более 2-х мм на сторону без деформации, искажения или изменения структуры основного металла. Таким образом восстанавливают детали, не подвергающиеся в процессе эксплуатации ударам, знакопеременным нагрузкам, сильному нагреву.
2. Газопламенное напыление порошка с одновременным оплавлением. Используется для восстановления износов 3-5 мм. Восстанавливаются детали, работающие при знакопеременных нагрузках, изготовленные из хромистых конструкционных сталей
3. Газопламенное напыление порошков с последующим оплавлением. Восстанавливают детали типа вала с износом до 2,5 мм на сторону из материалов устойчивых против коррозии, работающие в условиях абразивного изнашивания, действия повышенных температур.
Технологический процесс газопламенного напыления состоит из следующих этапов:
1) нагрев поверхности детали до 200 - 250 °С,
2) нанесение подслоя;
3) нанесение основных слоев с заданными физикомеханическими свойствами.
Для осуществления процесса используют сварочные горелки, снабженные бункером для порошка. У инжекторного распылительного аппарата (рис. 18) порошок через клапан, размещенный в корпусе аппарата под влиянием всасывающего действия кислорода и горючего газа, протекающего по каналу, попадают в сопло, а затем - в ядро пламени.
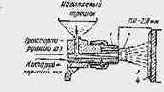
Рис.18
Годовой экономический эффект от восстановления деталей
Если на предприятии внедряется технологический процесс восстановления взамен приобретения новых деталей, то при одинаковом сроке службы деталей годовой экономический эффект ( Эг ) будет равен:
ЭГ = [ hЦн - (СВ + ЕНК) ]NВ ,
где h - коэффициент, учитывающий затраты на доставку новых деталей на ремонтные предприятия,
Цн - оптовая стоимость новых деталей;
ЕН - нормативный коэффициент окупаемости капиталовложений;
К - удельные капиталовложения;
nВ - число восстановленных деталей в расчетном году.
При различных сроках службы ( для деталей со сроком службы больше года):
ЭГ = [ hЦн×(Р1+Ен)/(Р2+ Ен) - (Св + Е НК) ] nВ ,
где Р1 и Р2; - величины обратные срокам службы новой и восстановленной деталей, соответственно. Для деталей со сроком службы менее одного года:
"ЭГ = [ hЦн × Wв/Wн - (СВ + ЕНК) ] n В ,
где Wв и Wн - сроки службы восстановленной и новой детали.
Изнашивание деталей машин
Процесс изнашивания деталей машин характеризуется тремя периодами во времени (Рис 1):
1) начальным (приработкой);
2) периодом установившегося изнашивания,
3) усиленного (аварийного) износа.
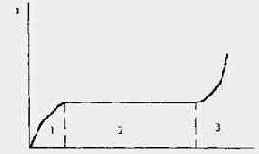
Рис.1
Интенсивность изнашивания (И) в первом периоде велика, во втором - мала, в третьем - вновь велика.
Износостойкость деталей определяется совокупностью внутренних и внешних факторов:
1 )физико-химическими и механическими свойствами трущихся поверхностей;
2)родом и характером трения;
3)величиной удельного усилия;
4)характером приложения нагрузки;
5)скоростью взаимного перемещения трущихся поверхностей;
6)способом подвода и качеством смазки;
7)температурой в месте контакта;
8)коррозионным воздействием среды.
Следует признать, что основное влияние на износостойкость оказывает структура металлов и сплавов.
Многочисленными исследованиями установлено, что более всего распространен абразивный износ - разрушение поверхностей деталей при трении скольжения, обусловленное наличием в зоне трения абразивной среды. На рис.2 показана диаграмма М.М.Тененбаума, отражающая связь между относительной износостойкостью (e) и структурой железоуглеродистых сплавов. Несмотря на то, что диаграмма не отражает всех структурных факторов, влияющих на износостойкость, она позволяет проводить качественный анализ влияния на износостойкость содержания углерода и структурного состояния сталей.
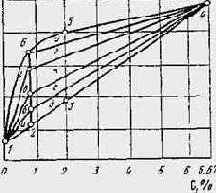
Рис. 2
На отрезке 1 -2 рис. 2 находятся значения относительной износостойкости отожженных доэвтектоидных сталей, на отрезке 2-3 - заэвтектоидных сталей, на отрезке 3-4 - белых чугунов Точки 1,2,4 характеризуют относительную износостойкость феррита, перлита и цементита, сооответственно. Линия 2-6 отражает относительную износостойкость эвтектоидных сталей в зависимости от дисперсности частиц цементита
Легирование является эффективным способом повышения износостойкости. На рис 3 показано влияние небольших добавок наиболее распространенных легирующих элементов на износ доэвтектоидной стали
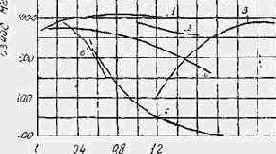
элементов, % мас.
Рис.3
На рис. 3 линия 1 - содержание никеля, 2 - марганца, 3 - кремния, 4 - хрома совместно с никелем (1:3), 5 - содержание фосфора, 6 - хрома
В зависимости от условий взаимодействия детали с абразивными частицами разрушение металла может происходить в результате микрорезания, многократного пластического деформирования поверхности трения и коррозионно-механического изнашивания. Установлено, что механизм абразивного изнашивания определяется главным образом соотношением значений твердости материала, Нм, и твердости абразивных частиц, На, (КТ=НМ/На). Схемы разрушения поверхностей трения представлены на рис. 4.
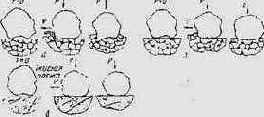
Рис. 4
Микрорезание и интенсивное пластическое деформирование поверхности трения могут наблюдаться при Нм < < На (рис.4,а) При более высокой твердости сплава процесс разрушения протекает в основном за счет коррозионно-механического изнашивания или хрупкого выкрашивания (рис.4, в)
При значениях Кт <0,6 имеет место пластическое оттеснение (рис.4, б). Увеличение Кт до значений, превышающих 0,6, приводит к интенсивному росту износостойкости детали.
При движении абразивной массы по поверхности изделия происходит непрерывное деформирование основы сплава вместе с мелкими карбидами, рассеянными по всему объему. Эти деформационные процессы определяют интенсивность изнашивания изделия при условии, что твердость металла Нм < 0,8 На . При этом, чем выше твердость и ниже пластичность матрицы, тем больше сопротивление сплава истиранию в абразивной среде. При взаимодействии твердых структурных составляющих с "мягким" абразивным материалом процесс изнашивания может протекать вследствие истирания окисной пленки, непрерывно восстанавливающейся в атмосферных условиях, или вследствие выкрашивания структурных элементов сплава при наличии динамических нагрузок.
Электроды, порошковая проволока и лента
При ручной и механизированной электродуговой наплавке применяют: электроды, проволоку сплошного сечения, порошковую проволоку и электродную ленту. Рассмотрим примеры применения того или иного материала в виде электродов для наплавки различных деталей.
Для наплавки ковшей пескометов и землечерпалок, матриц и штемпелей пресс-форм, матриц и пуансонов, подвергающихся в процессе эксплуатации интенсивному абразивному изнашиванию без ударных нагрузок, применяют электроды марок Т-590, X-5, БХ-2, принадлежащие к гр.G (ЗООХ25С2ГР, 350Х26Г2Р2СТ и т.п.), обеспечивающие в структуре наплавленного металла карбиды, карбобориды и ледебурит (НRС57 - 65).
Детали, в процессе эксплуатации, подвергающиеся интенсивному износу с ударами незначительной интенсивности (ножи и отвалы бульдозеров, ковшовые цепи экскаваторов), наплавляют электродами марки Т-268 (гр. G - ЗООХ25Т). В структуре наплавленного металла присутствуют карбиды и ледебурит, его твердость НRС58 - 60.
Интенсивный износ с ударами средней интенсивности (детали центробежных насосов, загрузочных устройств доменных печей) требует применения для наплавки электродов марки ЦС-1 и ЦС-2 (ЗООХ28С4Н4, гр. G и 170Х15Н2Г, гр. Е), обеспечивающих в структуре наплавленного металла аустенита с карбидной эвтектикой (после термообработки - мартенсита и карбидов, остаточного аустенита) НRС45 - 54. Электроды ЦН-11 (225Х10ПОС) применяют для наплавки деталей из стали 110Г13Л (черпаки драг и т.д.).
Ножи автогрейдеров, штампы калибровочные, режущий инструмент и др., подверженные абразивному изнашиванию и высоким ударным нагрузкам, наплавляют электродами ВСН-6, ВСН-8 (гр. Р - 110Х14В13Ф2), обеспечивающими в структуре наплавленного металла аустенит, мартенсит и карбидную эвтектику (НRС55 - 60).
Детали опорных частей наземных трубопроводов, колеса ходовой части машин, била молотковых дробилок, буровые долота и др. в северном исполнении, подвергающиеся абразивному изнашиванию, смятию, ударным нагрузкам при комнатной и отрицательных, до -60° С, температурах наплавляют электродами марок ВСН-9 и ВСН-10, принадлежащими гр.
Е (100Х12Н2АТ, 60Х14Н3М3). Структура наплавленного металла - аустенит и карбиды (НRС35 - 45).
Штампы, работающие при температурах до 400° С, наплавляют электродами Ш -7 (гр. В - 50Х2М). Структура наплавленного металла - сорбит (НRС38 - 44), а после термообработки - мартенсит и остаточный аустенит.
При выборе порошковой проволоки и ленты для наплавки руководствуются теми же принципами, что и при выборе марки электродов.
Детали, эксплуатирующиеся в условиях абразивного изнашивания при нормальных и повышенных температурах: детали загрузочных устройств доменных печей, била и футеровки конусных дробилок, ножи бульдозеров, гильзы шнековых насосов наплавляют порошковой проволокой марки ПП-АН101 (гр. G - УЗОХ25НЗСЗ), обеспечивающей в структуре наплавленного металла ледебурит и карбиды. Буквы "ПП" обозначают "порошковая проволока".
Ролики рольгангов, детали смесителей, ножи для холодной резки металла и др. детали, работающие в условиях абразивного изнашивания и ударных нагрузок, наплавляют порошковыми проволоками марок ПП-АН103 и ПП-АН104 (гр. Е - У20Х12М и У20Х12ВФ). Структура наплавленного слоя - аустенит и карбиды.
Детали из стали Гатфильда, например, крестовины стрелочных переводов наплавляют порошковой проволокой ПП-АН105 (гр. С – Г13Н4); в структуре наплавленного металла – аустенит.
Прессовый инструмент, ножи для горячей резки, штампы для горячей штамповки наплавляют порошковой проволокой ПП-АН 130 (гр. Н - 25Х5ФМС); структура наплавленного металла - мартенсит.
Детали ходовой части гусеничных тракторов, звенья агломерационных машин, крановые колеса наплавляют порошковой лентой марки ПЛ-АН126 (" ПЛ" - порошковая лента), соответствующей стали 20Х2ГМ (гр. А), обеспечивающей в структуре наплавленного металла перлит и феррит
Наплавка слоя нержавеющей стали выполняется порошковой лентой ПЛ-АН134 (гр. D - 10Х20Н10Б): структура наплавленного металла - аустенит.
Электролитическое хромирование
Различают: коррозионностойкое, износоустойчивое, пористое, декоративное электролитическое хромирование. Различают три группы деталей, наращиваемых хромом:
1) детали, наращиваемые с целью восстановить размеры и создать посадки с натягом;
2) детали, работающие на трение при малых и средних давлениях и окружных скоростях (валы, плунжеры, цилиндры, поршни, мерительный инструмент);
3) детали, работающие при повышенных давлениях и знакопеременных нагрузках (для которых необходима максимальная прочность связи слоя хрома с деталью).
При нанесении хромового покрытия необходимо осуществлять следующие операции.
1- удаление с поверхности деталей смазки и загрязнений (промывка в бензине или керосине);
2- сушка (протирка сухой ветошью, обдув сжатым воздухом),
3- наружный осмотр в целях выявления дефектов;
4- удаление слоя хрома: а) с латунных и бронзовых деталей - в 20-25% растворе НСl при 18-25 °С; б) с остальных деталей - в 10 -15 % растворе NaОН при 18-25 °С;
5- промывка в холодной проточной воде, а затем - в горячей при температуре 70 - 80 °С;
6- сушка (то же, что и 2);
7- магнитный контроль для выявления трещин в деталях;
8- шлифование или полирование поверхности,
9- контроль качества поверхности;
10- изоляция нехромируемых участков (полихлорвиниловой пленкой, цапон-лаком, клеем АК-20, БФ);
11- зачистка мест подключения контактов;
12- закрепление деталей в подвесочных приспособлениях;
13-монтаж и установка анодов;
14- обезжиривание деталей (раствор: 40 - 50 г/л тринатрийфосфата +10-12 г/л NаОН + 25 - 30 г/л жидкого стекла, температура раствора 60 - 70 °С, выдержка на катоде 3 -5 мин., на аноде - 1 - 2 мин.);
15- промывка теплой проточной водой;
16- химическое декапирование в течение 0,25 - 1,0 мин в растворе Н2SO4 при 18-25 °С,
17- промывка проточной водой;
18- электрохимическое декапирование в электролите хромирования при плотности тока, I =36 - 35 А/дм2, при температуре 50±2 °С;
19- хромирование в электролите (табл.2)
Таблица 2. - Растворы электролитов хромирования по вариантам, г/л
Компоненты электролита и режимы |
1 |
2 |
3 |
4 |
хромовый ангидрид |
120-150 |
200-250 |
300-350 |
225-300 |
Н2SО4 |
1,2-1,5 |
2,0-2,5 |
3,0-3,5 |
|
сернокислый стронции |
- |
- |
- |
5,5-6,5 |
КSiF6 |
- |
- |
- |
18-20 |
|
||||
температура, °С |
50-65 |
45-60 |
40-50 |
50-65 |
плотность тока, А/дм2 |
30-100 |
20-60 |
15-30 |
40-100 |
выход по току, % |
15-16 |
12-14 |
10-12 |
18-20 |
21- промывка в холодной проточной воде;
22- промывка- нейтрализация в течение 0,5 - 1,0 мин в 3 - 5 % растворе Nа2СОз при температуре 18-25 °С;
23- промывка в холодной проточной воде;
24- промывка в горячей проточной воде;
25- сушка в печи при температуре 120 - 130 °С,
26- контрольный обмер деталей, снятие с подвесок, удаление изоляционного слоя;
27- термическая обработка при температуре 200 - 250 °С в течение 2-3 часов для удаления водорода из хромового слоя;
28- шлифование до номинальных размеров;
29- окончательный контроль качества и размеров.
Большие детали хромируют не в стационарных ваннах, а при помощи переносных, устанавливаемых на требуемые участки (например, внутренние полости деталей выступают в роли ванны хромирования). Для лучшего удержания смазки на деталях выполняют пористое хромирование. При этом используют электролит с соотношением:
Cr2O3/Н2SО4 = 95 - 120.
Для увеличения пористости после хромирования применяют анодное травление при плотности тока, i, равной 40 - 60 А/дм2 в течение 5-12 минут в том же растворе.
Электролитическое железнение
Электролитическое железо, полученное из хлористых электролитов содержит до 99,99 % железа, 0,0001 % углерода, 0,0001 % серы и менее 0,0002 % фосфора. Добавление в электролит сахара или глицерина приводит к повышению содержания углерода и твердости слоя.
Процесс ведут с использованием растворимых (стальных) и нерастворимых (угольных) электродов. Применяют хлористые и сернокислые электролиты (табл.3).
Таблица 3 - Составы электролитов железнения по вариантам, г/л.
Компоненты электролита и режимы процесса | 1 | 2 | 3 | 4 |
хлористое железо | 200-250 | 300-350 | 600-680 | - |
сернокислое железо | - | - | - | 300 |
NaС1 | 100 | - | - | 150 |
НС1 | - | - | - | 0,4-0,7 |
рН | 0,8-1,2 | 0,8-1,2 | 0,8-1,5 | - |
температура раствора, °С | 70-80 | 70-80 | 70-80 | 95-98 |
плотность тока, А/дм2 | 20-40 | 20-50 | 20-60 | 10-15 |
выход по току, % | 85-92 | 85-95 | 85-95 | 90 |
Осадок электролитического железа, полученный в концентрированной хлористой ванне при температуре равной температуре кипения и плотности тока 10-12 А/дм2 получается пластичным и мелкозернистым. При осаждении при тех же режимах из сернокислых электролитов получаются хрупкие и крупнозернистые осадки. Пластичные осадки железа в сернокислых ваннах можно получить при нормальной температуре при плотности тока 0,1 - 0,2 А/дм2. Хрупкость электролитического железа связана с поглощением им водорода. Так, например, электролитическое железо полученное из хлористой ванны при 100 °С содержит 0,002- 0,003 % Н2 и имеет твердость НВ 100-400, а из сернокислой ванны при тех же условиях - 0,085 % Н2 и твердость НВ 200-300.
Термическая обработка - отжиг при температуре 500-600 °С уменьшает содержание водорода в слое и твердость на 40-45 %, внутренние напряжения - на 15-20 %.
С целью восстановления кроме электролитического хромирования и железнения применяют электролитическое никелирование и цинкование.
Электромеханическая обработка
Электромеханическая обработка (ЭМО) основана на сочетании термического и силового воздействия на поверхностный слой обрабатываемой детали. Сущность этого способа заключается в том, что в процессе обработки через место контакта инструмента с изделием проходит ток большой силы и низкого напряжения, вследствие чего выступающие гребешки подвергаются сильному нагреву, под давлением инструмента деформируются и сглаживаются, а поверхностный слой металла упрочняется.
Принципиальная схема ЭМО на токарном станке показана на рис. 20. От сети напряжением 220 - 380 В ток проходит через понижающий трансформатор, а затем - через место контакта детали с инструментом. Сила тока и вторичное напряжение регулируется в зависимости от площади контакта, исходной шероховатости поверхности и требований к качеству поверхностного слоя
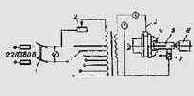
Рис.20
На рис.20: 1 - рубильник; 2 - реостат; 3 - вторичная обмотка; 4 - патрон; 5 - деталь; 6 -задняя бабка, 7 - инструмент.
Процесс ЭМО имеет разновидности: электромеханическое сглаживание (ЭМС), электромеханическую высадку металла (ЭМВ). Высадка является основной операцией электромеханического восстановления деталей, а поэтому часто под ЭМВ подразумевается сам способ восстановления.
С точки зрения металловедения, процессы ЭМО можно отнести к особому типу поверхностной термомеханической обработки (ТМО). При этом наблюдается получение особой мелкодисперсной и твердой структуры лишь в поверхностном слое, обладающем высокими физико-механическими и эксплуатационными свойствами
Процесс восстановления деталей методом ЭМО основан на перераспределении материала восстанавливаемой детали. При этом различают два способа восстановления: без добавочного материала и путем закатывания добавочного металла.
При осуществлении восстановления посадочных поверхностей нормально изношенных деталей без добавочного металла (рис. 21) технологический процесс состоит из двух операций: высадки металла и сглаживания посадочной поверхности
до определенного размера.
В первом случае обработка проводится пластиной 2 из твердого сплава, ширина поверхности контакта которой численно меньше подачи примерно в три раза, а во втором случае - твердосплавной пластиной 3, ширина контакта которой значительно превышает подачу.
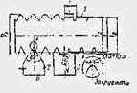
Рис. 21
При восстановлении деталей с введением дополнительного металла (рис.22) производится глубокая высадка изношенной поверхности детали 1 пластиной 2, затем для лучшего направления проволоки (добавочного металла) производится некоторое сминание вершин выступов, после чего в канавку вставляется конец проволоки 3 и производится электромеханическое сглаживание пластиной 4 при малой окружной скорости. При этом вводимая проволока имеет принудительное направление.

Рис. 22
Классификация наплавочных материалов
Наплавочные материалы классифицируют по различным признакам. Принятое Международным институтом сварки (МИС) подразделение наплавочных материалов предусматривает классификацию их по химическому составу наплавленного металла.
Нелегированные или низколегированные стали в зависимости от содержания углерода относят к группам: А (содержание углерода менее 0,4%) и В (содержание углерода более 0,4%). Твердость наплавленного металла группы А - НRС40, группы В -НRС60.
Аустенитные высокомарганцовистые стали относят к группе С; в рабочем состоянии они имеют твердость НRС50.
К группе В принадлежат аустенитные хромоникелевые стали с твердостью в рабочем состоянии НRС40.
Хромистые стали с твердостью НRС45 относятся к группе Е.
Быстрорежущие стали, группа К, обладают высокой твердостью в рабочем виде - НRС62.
Примерно такую же твердость (НRС60) имеют высокохромистые специальные чугуны - группа С.
Соответственно, к группам Н, N, Qa, Qb и Р принадлежат хромовольфрамовые теплостойкие стали, кобальтовые сплавы с хромом и вольфрамом, никелевые сплавы с хромом и бором, никелевые сплавы с молибденом и карбидные зернистые и спеченные сплавы.
В отечественной практике принята классификация, учитывающая химический состав наплавленного металла, его микроструктуру, условия эксплуатации и назначение наплавляемых деталей.
Большое значение для качества наплавленного металла играет его микроструктура. В ряде случаев используется классификация применяемых в промышленности наплавочных материалов по этому принципу.
1. Наплавочные материалы, обеспечивающие структуру мартенсита или продуктов его распада.
2. Наплавочные материалы, обеспечивающие получение аустенитной структуры.
3. Доэвтектические и эвтектические сплавы со структурой, состоящей из дендритов, аустенита и эвтектики.
4. Наплавочные материалы, которые при наплавке обеспечивают получение структуры заэвтектических чугунов, представляющей собой ледебурит и первичные карбиды.
Наплавочные материалы, дающие наплавленный металл с преимущественно мартенситной основой и мелкими специальными карбидами.Классификация способов восстановления
1. Сварка - технологический процесс образования неразъемного соединения деталей машин, конструкций и сооружений путем их местного сплавления или совместного деформирования, в результате чего возникают прочные связи между атомами соединяемых тел. Существуют свыше 60 методов сварки, наиболее распространенными из которых являются
1.1. Ручная дуговая - применяется для заварки трещин, обломов, приварки накладок, вставок, заплат.
1.2. Автоматическая и механизированная дуговая - то же и сварка тонколистового материала.
1.3 Аргонно-дуговая - сварка алюминия и коррозионностойких сталей.
1.4. Газовая - заварка трещин, обломов, сварка тонколистового материала.
1.5. Контактная - сварка тонколистового материала.
1.6 Трением - стыковая сварка деталей и их элементов при повышенных требованиях к качеству сварного соединения I 7. Термитная - сварка крупногабаритных и массивных деталей
1.8. Электрошлаковая - приварка обломов, сварка крупногабаритных деталей.
1.9. Электроннолучевая - сварка ответственных деталей с повышенной точностью.
1.10. Ультразвуковая - сварка цветных металлов, пластмасс, сталей
1.11. Высокочастотная - сварка коррозионностойких сталей, пластмасс.
1.12. Магнитно-импульсная - сварка разнородных материалов
1.13. Взрывом - то же.
1 14. Давлением - сварка деталей и элементов различных по конфигурации.
1.15. Диффузионная в вакууме - сварка ответственных и мелких деталей с повышенной точностью
1.16. Кузнечная - сварка неответственных деталей с невысокой точностью при повышенных требованиях к прочности сварного соединения,
Примечание. Материал выносится на самостоятельное изучение и рассматривается на семинарском занятии.
2. Наплавка - нанесение слоя металла заданного состава на деталь или режущую часть инструмента методами сварки для образования поверхностного слоя, обладающего заданными свойствами (повышенной прочностью, износостойкостью, кислотостойкостью и т.д.), а также для восстановления изношенной поверхности. Основные способы наплавки:
2.1. Дуговая под флюсом - наплавка деталей диаметром более 50 мм при повышенных требованиях к качеству наплавленного металла и толщине слоя наплавленного металла более 1 мм.
2.2. Дуговая в среде С02 - наплавка стальных деталей диаметром более 16 мм широкой номенклатуры.
2.3 Дуговая с газопламенной защитой - наплавка стальных и чугунных деталей работающих в различных условиях.
2.4 Вибродуговая - наплавка стальных деталей работающей в различных условиях при невысоких требованиях к сопротивлению усталости.
2.5 Дуговая порошковой проволокой или лентой - наплавка износостойких слоев на детали, работающие в условиях интенсивного изнашивания, ударных нагрузок, в узлах трения.
2.6. Дуговая в среде аргона - наплавка алюминиевых деталей и деталей из коррозионностойких сталей.
2.7. Контактная - наплавка гладких цилиндрических деталей с износом не более 1мм.
2.8. Газовая - наплавка цилиндрических и профильных деталей с местным износом при повышенных требованиях к износостойкости.
2.9. Плазменная - наплавка ответственных деталей при повышенных требованиях к износостойкости и сопротивлению усталости.
2.10. Многоэлектродная под флюсом - наплавка деталей со значительным износом
по величине и площади
2.11. Лежачим электродом - наплавка плоских поверхностей и поверхностей со сложной конфигурацией со значительным износом.
2.12. Электроимпульсная - наплавка наружных цилиндрических поверхностей с износом до 0,5 мм с ограничением температуры нагрева детали.
2.13. Электроискровая - наращивание и упрочнение поверхности с износом до 0,2 мм при невысоких требованиях к сплошности покрытия.
2.14. Электрошлаковая - наплавка деталей с износом более 6 мм.
215. Жидким металлом - наплавка деталей со значительным износом (более 3 мм) при повышенных требованиях к износостойкости и невысоких требованиях к стойкости против ударных нагрузок.
2.16. С одновременным деформированием - наплавка деталей с наружным шлицевым профилем.
2 17. С одновременным резанием - наплавка и обработка износостойких материалов в нагретом состоянии, обработка которых в холодном состоянии затруднена.
2.18. Лазерная - наплавка износостойких материалов на ответственные детали со сложным профилем.
2.19. Высокочастотная - наплавка износостойких материалов на рабочие органы и лезвия почвообрабатывающих и землеройных машин.
2.20. Высокочастотная в огнеупорной среде - наплавка проушин и цевок звеньев гусениц тракторов.
3. Нанесение газотермических покрытий:
3.1. Пламенное, порошковыми материалами без оплавления (на ацетилене или пропан-бутановой смеси) - восстановление и упрочнение наружных и внутренних цилиндрических поверхностей неподвижных сопряжений при невысоких требованиях к прочности сцепления с основным материалом.
3.2. Пламенное, порошковыми материалами с оплавлением - то же, но при повышенных требованиях к износостойкости и сцеплению с основным материалом.
3.3. Плазменное, порошковыми материалами - восстановление и упрочнение наружных и внутренних цилиндрических поверхностей,
34. Плазменное проволокой сплошного сечения - то же.
3.5. Детонационное - нанесение износостойких покрытий с особыми свойствами.
3.6. Ионно-плазменное - нанесение износостойких и защитных покрытий с особыми свойствами толщиной не более 0,02 мм.
3.7. Дуговое - нанесение покрытий на наружные и внутренние цилиндрические поверхности при невысоких требованиях прочности сцепления с основным материалом.
3.8. Высокочастотное - то же.
4. Холодное пластическое деформирование:
4.1. Раздача - восстановление наружных поверхностей полых деталей с нежесткими требованиями к внутреннему размеру.
4.2. Раздача с одновременной вытяжкой - восстановление специальным деформирующим инструментом наружных поверхностей и длинных полых деталей с нежесткими требованиями к внутреннему размеру.
4.3. Вытяжка - восстановление длины деталей с нежесткими требованиями к наружному размеру.
4.4 Раскатка - закрепление дополнительных ремонтных деталей в отверстиях.
4.5. Дорнование и калибровка - восстановление поверхностей отверстий после осадки или термического воздействия.
4.6. Протягивание - то же.
4.7. Осадка - восстановление наружных и внутренних поверхностей деталей при нежестких требованиях к длине.
4.8. Правка - восстановление формы.
4.9. Накатка - восстановление поверхности неответственных деталей, восстановление рифленной поверхности.
4.10. Обжим - восстановление внутренней поверхности детали при нежестких требованиях к размеру наружной.
4.1 I Чеканка - восстановление формы детали, упрочнение сварных швов.
5. Горячее пластическое деформирование:
5.1. Давление в закрытом штампе - восстановление формы и элементов детали за счет перераспределения металла из нерабочих поверхностей на рабочие для компенсации износа.
5.2. Гидротермическая раздача - восстановление наружных поверхностей полых деталей с нежесткими требованиями к внутреннему размеру.
5.3. Термопластический обжим - восстановление внутренних поверхностей полых деталей.
5.4. Накатка - восстановление зубчатых профилей шестерен и звездочек.
5.5 Ротационное деформирование - восстановление зубчатых и шлицевых поверхностей.
5 6. Обжим - то же, что 4.10.
5.7 Правка-то же, что 4.8.
5.8 Вытяжка - то же, что 4.3.
5.9. Осадка - то же, что 4.7.
5.10. Раздача - то же, что 4.1.
5.11. Выдавливание - местное деформирование с целью восстановления профиля и размеров рабочих поверхностей.
5.12. Оттяжка - восстановление формы рабочих поверхностей и режущих кромок.
5.13. Термомеханическая обработка - восстановление физико - механических характеристик металла, упрочнение.
6. Гальванические процессы:
6.1. Железнение - восстановление наружных и внутренних поверхностей с износом, не превышающим 0,2 - 0,5 мм при невысоких требованиях к прочности сцепления покрытия с основным металлам и требованиях повышенной твердости.
6.2. Хромирование - восстановление наружных и внутренних поверхностей с износом менее 0,2 мм при повышенных требованиях к износостойкости слоя.
63. Химическое и электролитическое никелирование - восстановление наружных и внутренних поверхностей с износом не более 0,05 мм,
6.4. Цинкование - защитное покрытие от коррозии.
6.5. Меднение - восстановление наружных и внутренних поверхностей деталей из медных сплавов.
6.6 Электролитическое натирание цинком и железоцинковыми сплавами - восстановление внутренних и наружных поверхностей при невысоких требованиях к твердости поверхности.
6.7. Нанесение гальванополимерных покрытий - восстановление внутренних и наружных поверхностей цилиндрических деталей.
6.8. Кадмирование - защитное антикоррозионное покрытие.
7. Нанесение полимерных материалов:
7.1. Напылением (газопламенное, в электростатическом поле, в псевдоожиженном слое, центробежным намазыванием) - восстановление формы поверхности облицовок и оперений, восстановление антифрикционных и электроизоляционных покрытий, восстановление посадочных поверхностей, заделка трещин, пробоин.
7.2. Литье под давлением, опрессовкой - восстановление антифрикционных, электроизоляционных и декоративных покрытий
7.3. Намазывание жидких прокладок, герметиков - восстановление герметичности соединений.
8. Применение дополнительных деталей:
8.1. Обрезка и приварка быстроизнашивающихся элементов - восстановление рабочих органов почвообрабатывающих, землеройных и мелиоративных машин, экструдеров, смесителей.
8.2. Бандажирование - восстановление наружных поверхностей, например, крановых колес.
8.3. Приварка элементов и вкладышей - восстановление размеров профильных поверхностей.
8.4. Постановка втулок и компенсационных шайб - восстановление отверстий и размерных цепей.
9. Химико-термическая обработка:
9.1. Цементация и нитроцементация - поверхностное упрочнение.
9.2. Повторное азотирование - восстановление деталей с износом не более 0,02 мм, поверхностное упрочнение.
9.3. Диффузионное хромирование - восстановление деталей с износом не более 0,05 мм, поверхностное упрочнение.
9.4. Сульфохромирование - восстановление деталей с износом не более 0,01 мм, поверхностное упрочнение.
9.5. Диффузионное цинкование - восстановление деталей из медных сплавов с износом не более 0,8 мм.
9.6. Диффузионное борирование - поверхностное упрочнение.
10. Электромеханическая обработка:
10.1. Высаживание и выглаживание - восстановление поверхностей неподвижных сопряжений с износом до 0,2 мм
11. Электрофизическая обработка:
11.1. Электроконтактная подводная, электроабразивная, анодно-механическая, электроэрозионная - обработка наплавленных поверхностей имеющих высокую твердость.
12. Пайка:
12.1. Легкоплавкими припоями, тугоплавкими припоями, пайка - сварка - восстановление герметичности соединений трубопроводов, восстановление инструмента.
13. Термическая обработка:
13.1. Отпуск, нормализация, отжиг, закалка, улучшение - восстановление физико-механических свойств и структуры материала, упрочнение.
Контроль качества
Качество восстановленных деталей оценивают степенью соответствия полученных физико-механических свойств и геометрических параметров заданным техническими условиями на восстановление или ремонтным чертежом.
Выполняют следующие виды контроля:
- летучий;
- промежуточный;
- окончательный.
Летучий контроль производится выборочно на отдельных деталях, как на отдельных операциях, так и на готовых изделиях.
Промежуточный контроль производится пооперационно и по группам операций. Выполняется самими рабочими, бригадиром или мастером.
Окончательный контроль проходят все детали. Выполняется работниками ОТК предприятия.
При обработке резанием проверяют: 1) соответствие размеров, формы, шероховатости заданным чертежом или техническими условиями; выполняют универсальным измерительным инструментом, калибрами и т.п. 2) периодически проверяют состояние технологического оборудования, режимы обработки.
При сварке и наплавке проверяют качество швов, толщину наплавленного металла, его твердость. Ответственные детали после осмотра подвергают магнитной, цветной или другой дефектоскопии.
Герметичность контролируют керосином или воздухом при определенном давлении на специальных стендах.
Гальванические покрытия контролируют по внешнему виду осажденного металла. Прочность сцепления оценивается путем нанесения острым инструментом двух рисок в виде креста и рассматривания под лупой на предмет наличия отслоения покрытия. Твердость покрытия измеряется микротвердомером, например, ПМТ - 3.
На термоучастках контролю подлежит соблюдение режимов термообработки и твердость деталей.
и задачи курса. Причины выхода
Введение. Цель и задачи курса. Причины выхода машин из строя.
ЛЕКЦИЯ 1О
Материалы для наплавки. Себестоимость восстановления. Годовой экономический эффект от восстановления деталей
До последнего времени при выборе материала для наплавки доминировал эмпирический подход. При этом условия эксплуатации деталей оценивались исключительно качественно. Например, условия ударно-абразивного воздействия на деталь описываются следующими определениями: "незначительные", "умеренные", "значительные" ударные нагрузки, т.е. они весьма условны, так как не основаны на объективных методах испытания.
И.В.Петровым был предложен количественный критерий ударно-абразивного воздействия - коэффициент динамичности, Кд. Он определяется, как отношение твердости образца из стали 110Г13Л после износа к его исходной твердости при данных условиях эксплуатации (известно, что данная сталь способна наклепываться под воздействием ударных нагрузок). Зная величину Кд для конкретных условий работы детали можно более точно выбрать материал для ее восстановительной или упрочняющей наплавки.
Кроме условий эксплуатации деталей, при выборе наплавочных материалов следует учитывать их стоимость и дефицитность.
и повторного использования материалов. Классификация
Техническая и экономическая целесообразность восстановления деталей и повторного использования материалов. Классификация способов восстановления деталей.
Техническая и экономическая целесообразность восстановления деталей и повторного использования материалов
Поскольку, как восстановление деталей, так и повторное использование различных материалов связано с определенными материальными и трудовыми затратами, то перед началом проведения работ по восстановлению или переработке материалов необходимо оценить насколько целесообразно с технической и экономической точек зрения их осуществление.
Техническая целесообразность восстановления учитывает: 1) уникальность подлежащей восстановлению детали; 2) серийность восстановительных работ для рядовых деталей; 3) степень износа деталей; 4) наличие условий для сбора, подготовки и восстановления деталей; 5) наличие материалов; 6) ресурс восстановленной детали.
Экономическая целесообразность определяется путем укрупненных расчетов себестоимости восстановления:
Св = (

где d- число восстанавливаемых поверхностей детали;
Суд- удельная себестоимость восстановления единицы площади (длины) i-ой поверхности принятым способом, грн/дм2 или грн/дм;
Si- площадь (длина) i-ой поверхности;
Кпд,- коэффициент повторяемости дефекта i-ой поверхности;
Дп- коэффициент, учитывающий затраты на подготовительные работы (при восстановлении для собственных нужд Дп=1,03; при централизованном восстановлении Дп= 1,1);
Цн- первоначальная цена восстанавливаемой детали.
Для решения вопроса об экономической целесообразности восстановления необходимо сравнить себестоимость восстановления (Св) с ценой новой детали (Цнов). Восстановление имеет экономическую целесообразность в случае, когда соблюдается условие; Св<Цнов.
Повторное использование материалов включает в себя два основных этапа: сбор и переработку. Техническая целесообразность проведения, как первого, так и второго этапа учитывает: 1)ценность и дефицитность материала подлежащего переработке; 2)содержание полезного продукта в отработанном материале; 3)возможность сбора, хранения и сортировки отработанного материала; 4)наличие, вид, количество загрязнений и посторонних примесей в нем; 5)возможность отделения полезного продукта от примесей , 6)потери при переработке (выход годного); 7)качество получаемого продукта.
Экономическая целесообразность повторного использования материалов определяется при сравнении затрат на переработку отработанного и цены на "новый" материал. Как и в случае восстановления, повторное использование экономически оправдано, если затраты на него меньше, чем цена "нового" материала.
химические основы наплавки. Флюсы. Формирование
Наплавка. Физико- химические основы наплавки. Флюсы. Формирование переходной зоны
при наплавке.
Наплавка по сравнению с другими способами восстановления дает возможность получать на поверхности деталей слой необходимой толщины и нужного химического состава, обладающий заданным комплексом свойств. В общем объеме работ по восстановлению деталей на ремонтных предприятиях различные способы составляют, %:
- наплавка под слоем флюса -31;
- вибродуговая - 12;
- в среде углекислого газа -20;
- порошковой проволокой без флюса и газовой защиты - 10;
- плазменная -1,5;
- электроконтактное напекание - 6;
- гальванические способы - 5;
- электромеханическая обработка - 1;
- электрошлаковая наплавка-1,5;
- наплавка жидким металлом - 2;
- восстановление полимерами - 5;
- другие способы - 5.
-
Газопламенное нанесение порошковых материалов. Металлизация.
Газопламенное нанесение порошковых материалов. Металлизация. Наплавка взрывом. Детонационное нанесение порошковых материалов
Электромеханическая обработка. Применение пластмасс
Электромеханическая обработка. Применение пластмасс и клеев. Восстановительная
термообработка.
Технология восстановления деталей: очистка деталей;
Технология восстановления деталей: очистка деталей; дефектация и сортировка; восстановление; контроль качества
Механизм образования связи между слоями
Для возникновения связи между металлами необходимо, чтобы поверхностные атомы были сближены на расстояния, при которых между ними возникло бы энергетическое взаимодействие, т.е. на расстояния порядка 10-8 – 10-7 см, характерные для расположения атомов в кристаллической решетке.
Для такого сближения атомов необходимо, чтобы жидкий металл смачивал твердый. Чтобы получить хорошее сцепление, необходимо возникшие при смачивании междуатомные связи сохранить после полной кристаллизации наплавляемого металла. Для первичного акта возникновения связи необходимо, чтобы имелись: а) чистая поверхность раздела; б) достаточная подвижность атомов хотя бы одного из металлов, которая допускает некоторое приспосабливание решеток соединяемых металлов.
Если при кристаллизации жидкого металла на поверхности твердого решетка образующейся фазы полностью совпадает с решеткой выходящего на поверхность твердого кристалла, то новый кристалл как бы продолжит в своем росте уже имевшийся. Чаще, однако, вновь образующиеся кристаллы имеют собственную решетку, отличную по типу и параметрам от решетки твердого металла, и соединение между ними происходит через промежуточный слой с искаженной кристаллической решеткой (переходной слой).
Металлизация
Металлизация - это один из распространенных способов получения металлических покрытий поверхностей нанесением на эти поверхности расплавленного металла. Сущность метода заключается в том, что металл, расплавленный дугой (при электрометаллизации) или ацетиленокислородным пламенем и распыленный сжатым воздухом (давлением 0,6 МПа) покрывает поверхность восстанавливаемой детали.
Процесс дуговой металлизации осуществляется металлизатором. Аппарат (см. рис 19) действует
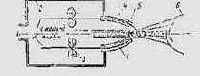
Рис.19
следующим образом: с помощью протяжных роликов по направляющим наконечникам непрерывно подаются две проволоки (1), к которым подведен электрический ток. Дуга, возникающая между проволоками, расплавляет металл. Одновременно по воздушному соплу 5 в зону дуги подается сжатый воздух (давление 0,6 МПа). Скорость движения частиц металла в струе достигает 120 - 300 м/с. Высокая скорость и малое время движения частиц, не превышающее сотых долей секунды, обусловливает пластическое деформирование частиц в момент удара их о твердую поверхность детали 6 и заполнение частицами неровностей и пор, сцепление частиц между собой и поверхностью. Таким образом, формируется сплошное покрытие толщиной от нескольких микрон до 10 мм (обычно для тугоплавких металлов толщина слоя от 1 до 1,5 мм, а для легкоплавких - от 2,5 до 3 мм).
В зависимости от источника расплавления металла металлизацию разделяют на:
1 - газопламенную; 2 - дуговую; 3 - высокочастотную; 4 - плазменную.
Наибольшее распространение на практике нашла дуговая металлизация.
В зависимости от цели восстановления и условий эксплуатации деталей для металлизации применяют проволоки различных марок (табл.1).
Таблица 1. - Марки проволок для дуговой металлизации
Операции | Материал проволоки |
Восстановление поверхностей под неподвижные посадки | Стали: 08, 10, 15, 20 |
Получение износостойких покрытий | Стали: 45, У7, У8, У10. Проволоки марок Нп-40, Нп-ЗОХГСА, Нп-ЗОХ13 |
Металлизация деталей, работающих при высоких температурах | Хромоникелевые стали |
Восстановление подшипников скольжения | Антифрикционные сплавы: 50 %А1+50 % Al |
Заделка трещин, раковин и нанесение антикоррозионных покрытий на чугунные детали | Цинк марок Ц1, Ц2 |
Заделка трещин в деталях из алюминиевых сплавов | Сплавы: АД, АМц, АМг |
Применяя разнородные материалы проволок можно получить композиционные покрытия. При нанесении слоя покрытия на деталь температура нагрева последней достигает 50 -70 °С, что позволяет наносить металлические покрытия на любые материалы (металлы, пластмассу, дерево, резину).
Недостатками процесса металлизации являются: 1. Металлизированный слой не повышает прочности детали. Поэтому металлизация не годится для восстановления деталей с ослабленным сечением. 2. Сцепляемость покрытия с деталью невысока. Поэтому не следует восстанавливать детали, работающие в условиях: а) сухого трения; б) динамических нагрузок.
Методы измерения износа
Существует несколько методов измерения износа, нашедшие большее или меньшее применение в науке и технике.
1. По потере веса детали или образца. Определяется величина абсолютного износа:
т1 – т2 ,
где m1 и m2: - масса образца или детали до начала изнашивания и после, соответственно;
либо величина относительного износа:
100 (т1 - т2)/т1 %.
Этот метод недостаточно точный, так как происходит взвешивание всего образца или детали, в то время как изнашиванию подвергается лишь его отдельная часть.
2. Метод определения линейного износа. Сущность метода заключается в измерении размеров трущихся тел до и после определенного периода эксплуатации (эксперимента). Определяется величина абсолютного и относительного износа. Этот метод, несмотря на недостаток присущий предыдущему методу, нашел на практике наибольшее распространение. Для осуществления метода применяют универсальные измерительные инструменты: микрометры, микрометрические нутромеры, индикаторные приборы.
3. Метод искусственных баз. Сущность метода - в изменении размеров суживающегося углубления, сделанного на изнашиваемой поверхности, профиль которого известен. Может быть нанесен отпечаток в виде пирамиды, конуса или высверлено коническое углубление, вышлифована лунка. Включает в себя:
- метод отпечатков. Искусственная база создается при вдавливании алмазной пирамидки с углом при вершине 136 о. Величина износа, Dh), определяется по формуле:

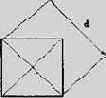
Рис.5
где d1, и d2 - размер диагонали отпечатка (рис.5) до начала изнашивания и после его завершения, соответственно.
Метод хорошо зарекомендовал себя при измерении износа плоских поверхностей.
- метод накерненных отпечатков. На поверхность, на которой определяется износ, ударом молотка с помощью керна с конической рабочей частью (угол при вершине, a, - 120 - 140 °) делают отпечаток. Величина износа определяется по формуле: Dh = с (d1 – d2) , где с = 0,5tg(90 - a/2).
- метод вырезанных лунок. Отличается от предыдущих методов тем, что на исследуемую поверхность наносится искусственная база с помощью резца имеющего рабочую поверхность в форме трехгранной пирамиды.
4. По количеству изношенного металла в масле. Метод применяют для определения износа деталей работающих в условиях жидкостного трения. После определенного периода эксплуатации из резервуара сливают масло и весовым методом определяют количество попавшего в него металла.
5. Метод радиоактивных изотопов. Позволяет осуществлять непрерывный контроль за ходом изнашивания в процессе эксплуатации. До начала измерений необходимо активизировать металл исследуемой детали одним из следующих способов:
1) введением радиоактивного изотопа при плавке;
2) нанесением радиоактивного электролитического покрытия;
3) диффузионным насыщением;
4) установкой радиоактивных вставок;
5) облучением нейтронами.
При эксплуатации детали с продуктами износа, пропорционально им, в масло попадают атомы радиоактивного индикатора. По интенсивности излучения в пробе масла судят о количестве металла попавшего в масло за исследуемый период времени.
Очистка деталей
Детали, сдаваемые на восстановление, очищают до такого состояния от загрязнений, чтобы их можно было осмотреть и выявить дефекты. От качества и полноты проведенных очистных работ зависит культура производства при восстановлении, производительность труда, долговечность отремонтированных деталей.
Классификация загрязнений и способы их очистки
1. Остатки смазочных материалов. Удаляют в растворах синтетических моющих средств.
2. Нагары. Это - твердые углеродистые частицы, образовавшиеся в результате сгорания топлива и масел. Удаляют в расплавах солей, в растворяюще-эмульгирующих средствах с доочисткой инструментом.
3. Лаковые отложения. Это - результат термического окисления тонких масляных пленок. Удаляют в растворяюще-эмульгирующих растворах с доочисткой инструментом и галтовкой.
4. Осадки. Это - липкая мазеобразная масса, откладывающаяся, как правило, в маслока-налах и грязеуловителях. Включает в себя продукты окисления масла и топлива, сажу, пыль, воду, частицы износа. Удаляют в кислотных растворах и расплавах солей, песком, ручным и механизированным инструментом.
5. Накипь. Образуется на деталях системы охлаждения. Удаляется в кислотных растворах, косточковой крошкой, очисткой ручным или механизированным инструментом.
6. Продукты коррозии и механического изнашивания деталей. Удаляют в растворах кислот, ручным и механизированным инструментом.
7. Старые лакокрасочные покрытия. Удаляют в растворах щелочных средств и с помощью смывок.
Для удаления различных загрязнений применяется целая гамма очищающих средств. Некоторые из них приведены в таблице 3.
Таблица 3.-Классификация очищающих средств
Очищающие средства | Состав | Представители | Температурный интервал применения, °С |
СМС | Синтетические ПАВ и натриевые соли органических кислот | МЛ-51, МЛ-52, Лабомид-101, МС-8, Темп- 100 | 70-100 |
Щелочные моющие | Щелочи, щелочные соли | Каустик | 80-100 |
Растворители | Углеводороды и их галлоидные производные | Керосин, дизтопливо, трихлорэтилен | 20-60 |
Растворяюще-эмульгирующие (РЭС), в т.ч. РЭС-1 | Углеводороды, ПАВ, стабилизаторы | АМ-15, ДВП-1 | 20-50 |
РЭС-2 | Хлорированные углеводороды, ароматические углеводороды | Ритм | 20 |
Переработка лома и отходов черных металлов
Производство черных металлов основано на применении сырых материалов с определенными стандартными свойствами и качеством. Вторичные черные металлы - основная часть металлургического сырья, поэтому в Украине действует ГОСТ 2787-84 "Лом и отходы черных металлов (шихтовые)".
Вторичные черные металлы используются при производстве стали и чугуна лишь потому, что имеют определенную металлургическую ценность.
Металлургической ценностью называется степень его эквивалентности заменяемому им первичному сырью (передельному чугуну и т.п.), т. е. способность металлолома превращаться под воздействием труда в продукт металлургического производства. Различные виды и классы металлолома имеют различную металлургическую ценность, которая характеризуется коэффициентом сравнительной металлургической ценности. Этот коэффициент определяется соотношением затрат на производство единицы металлургической продукции одинакового качества из первичного сырья и заменяющего его металлолома. В ресурсах вторичных металлов имеются виды и классы металлолома как с пониженной (стружка), так и с более высокой металлургической ценностью.
Классификация лома и отходов черных металлов заключается в распределении их по видам, категориям, группам и классам в зависимости от химического состава, назначения, качества и габаритов в соответствии с действующим стандартом. Весь металлолом разделен на три вида, две категории, 82 группы, два класса. Виды металлолома - стальной, чугунный и доменный присад - представляют собой классификационное деление лома и отходов по содержанию углерода и по назначению.
Стальной металлолом (стальные лом и отходы) - это лом и отходы черных металлов, содержащие до 2 % С, предназначенные в основном для сталеплавильных агрегатов, а также для вагранок.
Чугунный металлолом (чугунные лом и отходы) - это лом и отходы черных металлов, содержащие более 2 % С. предназначенные в основном для вагранок, а также для сталеплавильных печей.
Дробление применяется в основном для переработки стальной вьюнообразной стружки.
Брикетирование применяется как один из способов окускования чугунной и стальной стружки. Брикетирование производят различными методами: 1) с применением связующих материалов (жидкого стекла, цемента и др.), 2) с применением электрического тока, 3) с использованием энергии взрыва.
Переплав в шихтовые слитки применяется как способ переработки для окускования стружки легированной стали и сплавов. После переплава в небольших дуговых печах даже смешанной стружки получают слитки тяжеловесной металлошихты. Они имеют усредненный химический состав.
Разделка на копрах, прессах или взрывом применяется для переработки металлолома в виде особенно тяжелых, негабаритных и часто бесформенных массивов. Для копровой разбивки металлолома применяют специальные сооружения - копры. Копровая разбивка (станин крупных чугунных отливок и т.д.) основана на разрушении хрупких металлических массивов с помощью падающего на них груза - копровой бабы.
Разделка металлолома взрывом применяется только в тех случаях, когда металлические массивы невозможно разрушить другими способами. Заряды взрывчатых веществ закладывают в специально сделанные углубления - шпуры либо накладывают или вводят прямо в массив, после чего производят взрыв.
Как уже отмечалось, при сборе, хранении, переработке и других операциях нельзя смешивать лом и отходы различных групп, категорий и металлов (углеродистых с легированными, легированных или углеродистых - с цветными и т.д.). В противном случае происходит образование смешанного металлолома, который требует обязательной сортировки.
Сортировка вторичных черных металлов включает разделение их на виды, группы и классы с выделением лома для дальнейшей переработки, а также отбор из него цветного и взрывоопасного лома, неметаллических примесей. Для сортировки смешанного металлолома применяют следующие основные способы опознания его составляющих:
1) внешние признаки; 2) склонность к намагничиванию; 3) искровая проба;
4) спектральный анализ; 5) химический анализ.
Переработка нестандартных металлоотходов.
При специальных видах металлообработки образуется большое количество металлоотходов, которые не могут быть классифицированы в соответствии с ГОСТ 2787. На металлургических заводах такими являются мелкофракцнонные отходы при зачистке поверхностных дефектов абразивными кругами на слитках, слябах, поковках и прокате легированных сталей и сплавов (легированные пылевидные отходы). На машиностроительных и литейно-механических заводах при удалении заусениц и зачистке поверхностных дефектов чугунного и стального литья, шлифовке разнообразных деталей (углеродистые пылевидные отходы). В инструментальных цехах машиностроительных предприятий большое количество инструментальных пылевидных отходов образуется при изготовлении и заточке инструментов из твердых сплавов и быстрорежущих сталей.
Использование мелкофракционных отходов невозможно пока от них не отделены частицы абразива. Однако разделение отходов на металлическую и неметаллическую составляющую часто затруднено.
Металлическая составляющая углеродистых пылевидных отходов обладает сильномагнитными свойствами, а неметаллическая составляющая - немагнитна. Поэтому такие отходы лучше всего обогащать методом сухой магнитной сепарации. Затем отходы подвергают грохочению. Полученный концентрат может быть использован в порошковой металлургии или же после окускования для переплавки. Абразивная пыль может быть использована при выплавке синтетических шлаков, применяемых для улучшения качества стали.
Переработка лома и отходов цветных металлов.
Лом и отходы цветных металлов так же, как и вторичные черные металлы, должны быть подготовлены к использованию, т.е. пройти переработку. Переработка вторичных цветных металлов состоит обычно из следующих основных производственных процессов: 1) разделка; 2) сортировка; 3) приведение в габаритное состояние; 4) обработка стружки; 5) обогащение шлаков; 6) оплавление алюминиевого, свинцового и цинкового лома.
Разделка лома цветных металлов заключается в удалении из него приделок черных металлов и неметаллических материалов, а также в разделении механически соединенных различных сплавов.
Из кабельной продукции наиболее сложно разделать силовой бронированный кабель. Обычно его рубят или режут на куски длиной до 1,5 м. С каждого куска снимают железную ленту и джутовую изоляцию, разрубают свинцовую оболочку и удаляют ее, снимают с медных или алюминиевых жил кабеля бумажную изоляцию.
При разделке аккумуляторного лома свинцовые пластины вынимают из коробок, отбивают крышки, срубают клеммы, удаляют прокладки между пластинами.
Радиаторный лом перерабатывается на аллигаторных ножницах, при помощи керосинореза или вручную.
Таким же образом разделывают и другие виды лома цветных, металлов. Сортировка его производится по внешним признакам (цвет, масса, твердость и т.п.), по склонности к намагничиванию, капельным методом химического анализа.
Приведение лома и отходов цветных металлов в габаритное состояние производят пакетированием и брикетированием, ножничной и огневой резкой и другими способами, применяя соответствующее оборудование (пакетирпрессы, брикетирпрессы, гидравлические и аллигаторные ножницы различных типов и т.д.).
Обработка стружки цветных металлов (ее обезжиривание, сушка, дробление, магнитная сепарация) производится в центрифугах, печах различной конструкции, на стружкодробилках и магнитных сепараторах.
Пластмассы
Пластмассовые отходы возникают в промышленности при получении материалов, их переработке, изготовлении полуфабрикатов и изделий, а также в сфере потребления в виде отслуживших свой срок изделий.
Отходы производства: а) применяют в том же самом производственном процессе (это замкнутый оборот материала); б) в другом производственном процессе после соответствующей подготовки; в) вообще не применяют.
Многоразовая переработка ведет к изменению структуры и свойств материала, причем ухудшение свойств является неконтролируемым. Это связано со снижением средней молекулярной массы за счет переработки (при переработке термопласта подвергают воздействию высоких температур, сдвиговых напряжений и окислению; эти условия вызывают механодеструкцию материала). Наряду с молекулярной массой снижаются: прочность при растяжении и изгибе, сопротивление раздиру, относительное удлинение при разрыве, модуль эластичности, ползучести, жесткость, ударная вязкость, теплостойкость, возрастает проницаемость для жидкостей, газов и паров, а стойкость в тех же средах снижается. Поэтому регенераты, как правило, используют для производства изделий с более низкими потребительскими свойствами.
Повторное использование термопластов включает в себя: 1) сбор вторичного пластмассового сырья; 2) переработку термопластичного вторичного сырья; 3) преобразование пластмассового вторичного сырья в химическое сырье.
Основные требования при заготовке отходов из термопластов в сфере производства - обеспечение однотипности и чистоты. Особо важно, чтобы в отходы не попадали металлические включения.
При сборе отходов из термопластов в сфере бытового потребления выделяют два основных способа заготовки: а) выборочный сбор отходов пластмасс; б) выделение отходов пластмасс из бытового мусора. Второй способ заготовки подразумевает дополнительную сепарацию пластмассовых отходов.
Перечень основных операций подготовки отходов термопластов к переработке приведен в табл.4.
Таблица 4. - Операции и методы подготовки термопластов к переработке
Цель операции |
Операция |
Метод |
Изменение формы и размеров |
Грубое измельчение |
Распиловка (ленточные, дисковые, цепные пилы) |
Резание (рычажные, ударные и гидравлические ножницы) |
||
Дробление (валковая дробилка) |
||
Резание при низких и высоких температурах (ножевые дробилки) |
||
Тонкое измельчение |
Тонкое размалывание (ударно-отражательная или дисковая мельницы) |
|
Уплотнение |
Спрессовывание (пакетировочные прессы, питательные вальцы), спекание |
|
Агломерация (скоростные смесители, дисковые смесители, агломерация горячим паром) |
||
Грануляция |
Стренговая |
|
Ленточная |
||
Горячая обрубка |
||
Изменение |
Предварительная очистка |
Промывка (моечные машины) |
качества |
||
Тонкая очистка |
Промывка ( душевые установки, разбрызгивательные ванны, моечные шнековые машины, гидроциклоны) |
|
Сушка |
Центрифугование. Сушка горячим воздухом |
|
Отделение металлов |
Магнитное отделение. Индуктивное отделение. Осаждение. Флотация |
|
Дегазация |
Вакуумная дегазация |
|
Фильтрование |
Фильтрование расплава через сито |
|
Смешение Пластикация |
Сухое смешение (силосный смеситель, мешалки) Дозирование Смешение в расплаве (экструдеры, вальцы) Механический разогрев и дополнительный подвод теплоты (вальцы, экструдеры, закрытые смесители) |
|
Преобразование пластмассового вторичного сырья в низкомолекулярное химическое сырье включает в себя пиролиз полимеров, их гидролиз, гликолиз и метанолиз.
Пиролиз - это термическое разложение органических продуктов в присутствии кислорода или без него с целью получения низкомолекулярного химического сырья. При этом могут образовываться газообразные (пиролизный газ), жидкие (пиролизное масло) или твердые (кокс и др.) продукты пиролиза.
Область рабочих температур определяется перерабатываемым продуктом. Например, отходы ПХВ и побочные продукты выше 200 °С отщепляют хлороводород, а выше 400 °С разлагаются на технический углерод и углеводороды. Жидкофазный пиролиз полистирола при температурах выше 350 °С ведет к образованию стирола с большим выходом. Низкомолекулярный полиэтилен пиролизуется при 400 - 450 °С, при этом получают алифатические богатые олефинами масла, и алифатические воски. В табл. 5 приведены примеры низко- и высокотемпературного пиролиза отходов термопластов.
Таблица 5.- Примеры низко- и высокотемпературного пиролиза отходов термопластов
Перерабатываемое сырье |
Характеристика технологии и оборудования |
Низкомолекулярный полиэтилен, полистирол Бутылки из полистирола Измельченные старые шины Бытовой мусор Старые шины, смеси пластмассовых отходов, отработанный кабель Резиновые отходы, смешанные пластмассовые отходы |
Непрерывнодействующий реактор; 400-500 °С; продукт - горючее масло Реактор с псевдоожиженным слоем; ожиженный слой-песок, поток воздуха; 350-600 °С; продукты - частично окисленные масла Реактор с прямым обогревом и с псевдоожиженным слоем; ожиженный слой - пиролизный технический углерод, горячий воздух; 400-550 °С. продукты - горючее масло, сильно окисленное Барабанный реактор с косвенным обогревом, 400 °С, продукты - чистый пиролизный газ для коммунального газоснабжения, кокс Вращающийся барабанный реактор с косвенным обогревом; 700 °С; атмосфера азота, продукты - пиролизные масла, газ, технический углерод, ZпО Шахтные печи с прямым обогревом и ограниченный подачей кислорода; продукт - пиролизный газ |
Широкое распространение при переработке отходов пластмасс пиролиз нашел в Германии (фирма Ruhrcyemie AG), США (фирмы Procedyne Corp. Hydrocarbon Res. Inc.), Японии ( фирмы Japan Gasoline Co., Kawasaki Heavy Ind. и др.). Например, в городах Гифу и Кусатсу (Япония) в 1972 году внедрен метод двухступенчатого пиролиза. Он позволяет получать высококачественное химическое сырье из отходов. На первой стадии применяют микроволновый реактор-нагреватель, который работает при частоте 2,450 МГц. Диэлектрический разогрев отходов проводят, добавляя твердый NаОН и несколько капель воды к неполярным полимерам или опрыскивая поливинилхлорид и старые шины водным раствором NаОН. На первой стадии происходит дегидрохлорирование и образование соляной кислоты. Вторую стадию расщепления проводят в обогреваемом до 400 - 500 °С в червячном реакторе.
Гидролиз является реакцией, обратной поликонденсации. С его помощью при направленном действии воды по местам соединения компонентов поликонденсаты разрушаются до исходных соединений. Гидролиз происходит под действием экстремальных температур и давлений.
Фирмой Вауеr (Германия) разработан непрерывный способ гидролиза, при котором измельченный пористый материал с помощью дозирующего шнека подается в двухчервячный экструдер. В первой зоне экструдера пористый материал уплотняется, затем из него удаляется по возможности весь воздух. Уплотненный пористый материал в твердом состоянии доуплотняется в реакционной зоне. Температура цилиндра может достигать 300 °С. В реакционную зону под высоким давлением вводится вода, и материал, хорошо смешиваясь с нею, быстро превращается в пасту. Полностью гидролизованный материал при температуре около 200 °С выводится через систему понижения давления. При этом происходит удаление остатков воды. Продолжительность процесса составляет от 5 до 30 мин., производительность установки 150 кг/ч.
По сравнению с гидролизом для расщепления отходов ПЭТФ более экономичен другой способ - гликолиз. Деструкция происходит при высоких температурах и давлении в присутствии этиленгликоля и с участием катализаторов до получения чистого дигликольтерефталата.
В настоящее время все же самым распространенным методом переработки отходов ПЭТФ является их расщепление с помощью метанола – метанолиз. Процесс протекает при температуре выше 150 °С и давлении 1,5 МПа, ускоряется катализаторами. На практике применяют и комбинацию методов гликолиза и метанолиза.
В Японии разработан способ преобразования вспененного полистирола. Полистирол в присутствии никелевого катализатора гидрируется при 350 °С, получается этилбензол, который можно снова использовать для получения стирола.
Отходы реактопластов после измельчения можно в определенных количествах добавлять в формовочные массы без значительного изменения свойств последних.
Для подготовки и смешения отходов реактопластов хорошо себя зарекомендовали установки разработанные фирмами Hull (США) и Meiki (Япония). Бракованные и отслужившие свой срок изделия, облой, литники измельчают в двухмолотковых мельницах. Размолотый материал просеивают, отделяя частицы более 0,5 мм, и в смесительной емкости смешивают со свежим сырьем. Пыль отсасывают. Производительность установок около 50 кг/ч.
При введении в бетон - основной строительный материал - производственных отходов реактопластов получают бетон с повышенными теплоизоляционными свойствами. Добавки в бетон измельченных отходов резины в количестве от 0,5 до 1 % мас. улучшают экплуатационно-технические свойства пустотелых бетонных блоков.
В дорожном строительстве отходы термопластов применяют для модификации битумов. Целесообразно вводить измельченные отходы ПВХ в асфальтовую смесь при ремонте дорожного покрытия, так как это способствует повышению его морозо- и теплостойкости.
В сельском хозяйстве отходы вспененного полистирола применяют для улучшения почвы. Таким образом, на длительное время повышается воздухо- и водопроницаемость тяжелых глинистых почв. При этом также облегчается обработка земли, ускоряется прогрев почвы, улучшается ее структура.
Пластмассы и эластомеры являются высококачественными горючими материалами, которые дают высокую температуру горения.
При сжигании они позволяют сберечь приблизительно равное по массе количество мазута (теплота сгорания обычного бытового мусора составляет 2900 - 8400 кДж/кг; теплота сгорания пластмасс выше более чем в 2 раза). Загружать в сжигательные установки материал следует в размолотом состоянии. При этом образуются отработанные газы с температурой около 1000 °С. Согласно требований охраны окружающей среды дымовые газы, которые могут содержать токсичные компоненты (аммиак, хлор, хлороводород, циановодород, нитрозные газы, сернистый газ), перед выбросом в атмосферу должны быть подвергнуты очистке.
В Чехии разработана установка для сжигания отходов пластмасс и эластомеров, в которой за 1 час сжигается 1 м3 отходов с добавлением 20 кг дизельного топлива.
Заключение по всему курсу
Изучение курса не ставило своей целью получение студентами энциклопедических знаний по технологиям восстановления или по технологиям переработки отходов. Напротив, во главу угла ставилась цель привить студентам навыки творческого мышления путем постановки конкретных задач и совместного поиска путей их решения.
Подводя итог прочитанному материалу, необходимо выделить следующие основные моменты.
Первое. Выбирая тот или иной способ восстановления деталей и материалы, применяемые для этого, следует исходить из конкретных условий эксплуатации: рассмотреть нагрузки, при которых детали работают, воздействие среды, выяснить причины выхода их из строя.
Второе. Выполнение восстановительных работ должно быть предварено оценкой их экономической и технической целесообразности.
Третье. Технология восстановления должна отвечать ряду требований: обеспечивать в максимально возможном объеме возвращение деталям служебных свойств: быть максимально простой в осуществлении; не исключать возможности повторного восстановления; не требовать применения дорогих и дефицитных материалов; не быть энергоемкой; допускать применение средств механизации и автоматизации на всех этапах выполнения; отвечать требованиям техники безопасности и соответствовать природоохранным нормам.
Четвертое. Любая работа имеет технический и экономический результат. Поэтому обязательным моментом, завершающим восстановительные работы, должна стать оценка стойкости отреставрированных деталей, а также экономический эффект от внедрения выбранной технологии.
Подобными критериями следует пользоваться и при организации переработки и повторном использовании материалов, т.е. определить ценность того или иного материала, способ его переработки, затраты, необходимые для превращения отхода в сырье или продукт, оценить технический и экономический эффект от проведенных работ.
Повторное использование металлов
После окончания срока службы машин, металлоконструкций и других предметов черные и цветные металлы, из которых они изготовлены, сохраняют свои основные физические и химические свойства. Благодаря этой особенности металлы могут неоднократно использоваться в народном хозяйстве. Амортизационные металлические изделия и металлоотходы при обработке металлов образуют металлический лом, переплавляя который получают металлы для новых изделий.
Причины выхода машин из строя
Классификация причин разрушения деталей машин.
Наблюдения за износом и повреждениями деталей машин при эксплуатации позволили выделить пять основных видов разрушения деталей.
Деформация и изломы (хрупкий, вязкий, усталостный изломы, остаточная деформация, контактные усталостные повреждения). Механический износ (истирание металлических пар, абразивный износ, питтингование). Эрозионно-кавитационные повреждения (жидкостная эрозия, кавитация, газовая эрозия). Коррозионные повреждения (атмосферная коррозия, коррозия в электролитах, газовая коррозия) Коррозионно-механические повреждения (коррозионная усталость, коррозионное растрескивание, коррозия при трении).Рассмотрим некоторые примеры характерных разрушений деталей машин. Остаточная деформация. Этому виду разрушения подвержены бандажи и крановые колеса, рельсы, напряженные болты, подшипники качения. Характер повреждения - изменение геометрической формы (удлинение, изгиб, вмятины) Причины разрушения - длительное действие переменных контактных, растягивающих или сжимающих напряжений, повышение температуры металла.
Вязкий излом. Подвержены связи и анкерные болты, несущие элементы ферм, напряженные болты. Разрушение сопровождается значительной деформацией Поверхность излома матовая, волокнистая. Причина разрушения значительные перегрузки из-за нарушения нормальных условий эксплуатации
Хрупкий излом. Таким образом разрушаются сварные соединения, фасонные детали, болты, пальцы, втулки с повышенной твердостью Разрушение происходит при незначительной деформации. Поверхность излома имеет кристаллическое строение Причины разрушения - наличие ударных нагрузок, дефекты термообработки, повышенное содержание фосфора в стали, наличие концентраторов, трещин.
Усталостный излом. Подвержены рамы, оси, шатуны, болты, сварные соединения, подвергающиеся воздействию длительных знакопеременных, нагрузок. Характер повреждений - образование трещин. Причина разрушения - понижение прочности металла, действие знакопеременных нагрузок, циклические, термические напряжения, наличие концентраторов напряжений.
Абразивный износ. Характерен для деталей ходовой части тракторов, исполнительных механизмов формовочных машин, пескометов, открытых передач и т.д. Характер повреждения - постепенное изменение размеров. На поверхности наблюдаются риски параллельные направлению трения. Причины разрушения - взаимодействие трущихся поверхностей с абразивными частицами.
Истирание металлических пар. Подвержены подшипники скольжения, валы, оси, направляющие, цепные передачи, втулки и т.д. Характер повреждений - постепенное изменение геометрических размеров деталей. Причина разрушения - длительное трение сопряженных деталей.
Заедание. Присуще для шестерен зубчатых передач, подшипников качения и т.д. Характер повреждения - адгезия, вырывание частиц металла из контактных поверхностей. Причина разрушения - нарушение жидкостного трения при высоких скоростях.
Далее следует рассмотреть условия эксплуатации и способы повышения долговечности некоторых деталей машин.
Болты и шпильки резьбовых соединений в процессе эксплуатации подвергаются действию статических (при предварительной затяжке) и переменных напряжений. Их изготавливают из сталей: 10, 15, 20, 35, 40, 35Х, 40Х и др. При эксплуатации основные виды повреждений: усталостные изломы и деформация. Для повышения долговечности: необходимо повысить предел прочности стали, уменьшить концентрацию напряжений, произвести обкатку резьбы роликом.
Колеса зубчатых передач в процессе эксплуатации подвержены изгибу зубьев, контактному сжатию, трению и ударам при изменении частоты вращения. Они изготавливаются из сталей: 35, 40, 45, 35Х. 40Х, 40ХН. 38ХГН, 12ХНЗА, 40ХНМА, пластмасс, капролона. Основные виды повреждений: излом зуба (при перегрузке), выкрашивание и изнашивание зубьев. Для повышения долговечности следует выполнить: коррегирование зуба, поверхностную закалку, цементацию, азотирование поверхности зубьев.
Червяки и колеса червячных передач подвержены в процессе эксплуатации трению витков червяка о рабочую поверхность зубьев колеса, изгибу зубьев колеса.
Изготавливают, червяки - из конструкционной стали, колеса - из бронзы Бр.010Ф1 или Бр.А9Ж4, чугуна СЧ20 или СЧ25. Основные виды повреждений - пластическая деформация, излом зубьев колеса. Для повышения долговечности следует выполнить: коррегирование зуба колеса, закалку или цементацию рабочей поверхности витков червяка.
Валы и оси в процессе эксплуатации подвергаются изгибу, кручению, трению скольжения между цапфой и опорой. Изготавливают из сталей: 40, 45, 40Х, 45Х, 38ХГН, 37ХНЗА. Основные виды повреждений: усталостные поломки, изнашивание и задиры цапф. Для повышения долговечности уменьшают количество концентраторов, шлифуют цапфы, производят поверхностную закалку, наклеп галтелей.
Опоры скольжения подвергаются трению скольжения между опорой и цапфой. Изготавливают из антифрикционных материалов, баббитов, чугунов, металлокерамики. Основные виды повреждений при эксплуатации: изнашивание, заедание, усталостное разрушение поверхностей трения. Для повышения долговечности улучшают условия жидкостного трения, повышают жесткость опор и точность изготовления.
В подшипниках качения имеет место трение тел качения о наружные и внутренние кольца. Тела качения и кольца изготавливают из сталей: ШХ15, ШХ9, ШХ15СГ, 9X18, 15Х, 18ХГТ, 20Х2Н4А; сепараторы из низкоуглеродистой стали, бронзы, латуни. Основные виды повреждений при эксплуатации: излом колец, разрушение тел качения, изнашивание тел качения и колец, усталостное выкрашивание, заедание. Для повышения долговечности предлагается обеспечивать податливость корпуса в нагруженной части подшипника.
Применение клеев
Приклеивание тонких втулок на цапфы валов - один из способов восстановления изношенных цапф валов и подшипников. Подшипник растачивают до удаления следов износа, а на цапфу вала наклеивают тонкостенную втулку, наружный диаметр которой равен внутреннему диаметру подшипника. Цапфу вала протачивают так, чтобы толщина стенки втулки была не менее 2 мм. Затем внутреннюю поверхность втулки и наружную поверхность вала смазывают клеем. Втулку насаживают, не поворачивая, во избежание образования воздушных пузырьков
Приклеивание накладок на плоские направляющие. При эксплуатации деревообрабатывающих, металлорежущих станков наиболее сильно изнашиваются направляющие поверхности станин и других деталей, перемещающихся друг относительно друга. Трудоемкость ремонта направляющих может достигать 30-40 % трудоемкости ремонта станка. В настоящее время при ремонте плоских направляющих применяют эпоксидный клей.
Изношенные направляющие: 1) строгают или грубо пришабривают для обеспечения плотного прилегания накладок; 2) промывают и высушивают; 3) покрывают тонким слоем клея; 4) выдерживают; 5) устанавливают накладки и закрепляют их по краям штифтами. Штифты смазывают клеем и ставят в заранее подготовленные отверстия. 6) на накладки устанавливают груз. После приклеивания накладки обрабатывают. При повторном ремонте изношенные накладки отрывают, а поверхность направляющих очищают от остатков клея. Затем повторяют операции 1-6. Максимальная толщина накладок - 6 мм. Материалом накладок может служить любой антифрикционный материал (чугун, бронза, текстолит).
Для склеивания деталей, наклеивания дополнительных элементов из различных материалов, восстановления и монтажа фланцевых и шпоночных соединении, восстановления посадочных мест под втулки и кольца, устранения течей и неплотностей трубопроводов, емкостей, теплообменных аппаратов, корпусов насосов и т.д. применяют следующие клеи отечественного производства:
- К-153 (эпоксидно-тиоколовый), двухкомпонентный холодного отверждения;
- ЭД-20 и ЭД-16 (клеи на основе эпоксидно-диановой смолы), трехкомпонентные, холодного отверждения;
- ЭПК (эпоксидно-полиамидный), двухкомпонентный, холодного отверждения;
- УП-5-230, УП-5-231 (эпоксидные), двухкомпонентные, холодного отверждения;
- "СПРУТ-9М" (полиуретановый), трехкомпонентный, холодного отверждения;
- "СПРУТ -МП" (полиэфирный), трехкомпонентный, холодного отверждения;
- "СТЫК-3-8" (полиуретановый), однокомпонентный, холодного отверждения;
- К-17 (карбомидо-формальдегидный), двухкомпонентный,
- 88НП (полихлоропреновый), однокомпонентный, холодного отверждения;
- "ЛЕЙКОНАТ" (изоциановый), однокомпонентный, горячего отверждения.
Из клеев иностранных производителей наибольшее распространение нашли клеи фирм DEVCON (США) и LOCTITE (США):
- Plastic steel (содержит 80 % стального порошка, 20 % эпоксидной смолы и модификаторов);
- Plastic steel SF (эпоксидный состав со сверхбыстрым отверждением -3-5 минут);
- DEVCON BR (содержит 80 % бронзовой пудры и 20 %"эпоксидной смолы и модификаторов;
- LOCTITE –S 415,LOCTITE – S 495, LOCTITE – 638.
Применение пластмасс
Пластмассы в ремонтной практике наносят на поверхность деталей для восстановления их размеров, повышения износостойкости и улучшения герметизации. Покрытия из пластмасс снижают шум от трения и повышают коррозионную стойкость изделий. Пластмассы наносят следующими способами: а) литьем под давлением: б) горячим прессованием; в) вихревым способом, г) газопламенным способом; д) центробежным способом. Наибольшее распространение в отечественной ремонтной практике нашли акриловые пластмассы.
Акриловые, пластмассы содержат в качестве связующих материалов акриловые смолы - продукты полимеризации метил-метакрилата и сополимеризации метил-метакрилата со спиртом. К ним относят: а) акрилат АТС -1; б) бутакрил; в) эпоксидно-акриловые пластмассы СХЭ - 2 и СХЭ - 3. Это - термопластические быстротвердеющие пластмассы холодного отверждения. Их получают путем смешивания порошка и жидкости. Масса имеет консистенцию сметаны и затвердевает без подогрева и давления. С помощью пластмасс восстанавливают: направляющие станин станков; регулировочные клинья и прижимные планки механизмов всех видов; резьбы гаек ходовых винтов.
Для устранения дефектов в сварных швах, микротрещин, восстановления нарушенных неподвижных посадок, уплотнения резьбовых соединений и т.п. применяют анаэробные составы, отверждающиеся в зазоре между металлическими поверхностями при прекращении контакта с атмосферным кислородом: АНАТЕРМ 1У, УНИГЕРМ 6 -11.
Затвердевшая пластмасса износостойка, хорошо работает в паре с чугуном, сталью, бронзой, имеет малый коэффициент трения. Она стойка к щелочам, бензину, скипидару, пресной и морской воде, маслам.
Раствор пластмассы готовят непосредственно перед применением. Рекомендуются следующие пропорции порошка и жидкости ( П : Ж ): 1 : 0,75; 1 : 1; 1 : 1,5; 1 : 2. С повышением доли жидкого компонента увеличивается время отверждения и усадка. Пластмассы наносят кистью или лопаткой.
При восстановлении подшипников скольжения, имеющих незначительный равномерный износ, изношенную поверхность просто смазывают пластмассой. Для восстановления используют эпоксидную композицию следующего состава:
- эпоксидная смола ЭД-б - 100 мас. частей;
- порошок графита - 30;
- полиэтиленполиамин - 10
Роль термодиффузии при формировании переходной зоны
Распределение легирующих элементов при наплавке происходит в поле градиента температуры. Перемещение атомов под действием градиента температуры называется термодиффузией. В отличие от атомарной диффузии, перемещение атомов при которой происходит в поле градиента концентрации, термодиффузия вызывает их движение в противоположном направлении. После определенного периода времени наступает стационарное состояние распределения вещества вдоль всей длины тела (поток атомов при этом равен нулю). В этом случае справедливо равенство:
dc/dx = - (CQ*/RT2)dT/dx ,
где dc/dx и dT/dx - градиент концентрации и градиент температуры, соответственно,
с - концентрация диффундирующего вещества, молярные доли;
R - универсальная газовая постоянная, кДж/моль град;
Q* - теплота переноса при термодиффузии, кДж/моль;
Т – абсолютная температура, К.
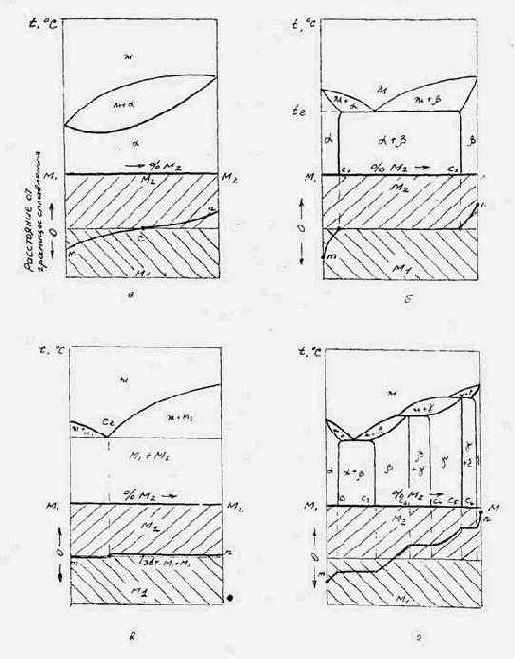
Рис.7
Пользуясь экспериментальными данными, рассчитывают величину теплоты переноса. По ее величине и знаку определяют направление и интенсивность перемещения атомов при осуществлении процесса наплавки или любого другого процесса связанного с градиентом температуры. При Q*>0 атомы вещества движутся в более холодную сторону; при Q*< 0 - в более горячую. Так, например, при термодиффузии углерода и кремния в чугунных образцах Q*C= 0,028кДж/моль; Q*Si - 0,12бкДж/моль.
Себестоимость восстановления
В общем виде себестоимость восстановления деталей (СВ) на конкретном предприятии может быть рассчитана по формуле:
Св = СИЗ + ЗПЛ + сОБ + НЦ+ Н3 + СБР + См .
где Сиз и См - стоимость, соответственно, изношенной детали и материалов для ее восстановления; Зпл - заработная плата за осуществление восстановительных работ; сОБ - расходы на содержание и эксплуатацию оборудования: Нц и Н3 - расходы, соответственно, цеховые и заводские; Свр - потери от брака.
Стоимость изношенных деталей, как правило, равна стоимости металлолома того же веса. Однако если детали доставляются с другого предприятия, то их стоимость примерно на 20% выше за счет сбора, сортировки, хранения и транспортировки к месту проведения восстановительных работ.
Стоимость материалов складывается из стоимости отдельных компонентов:
См =S(Qi× Ці) ,
где Q1 и Ц1 - соответственно, количество и цена 1-го компонента.
Заработную плату определяют с учетом всего комплекса операций и системы оплаты труда. В общем виде:
Зпл = (Т1С1/б0 + Т2С2/60 +......+Т6С6/60)КПКдКС ,
где Т1 .....Т6 - нормы времени на выполнение операций с 1 по VI разряды;
С1.....С6 - почасовые тарифные ставки с I по VI разряды;
Кп , Кд, КС - коэффициенты учитывающие, соответственно, премиальные доплаты на отпуска, выполнение гос. обязанностей и т.п. отчисления.
В качестве примера можно привести следующие данные из практики судоремонта. Стоимость восстановления головки поршня двигателя К6Z57/80F составляет 11,6% стоимости новой; стоимость восстановления гребного вала ледокола типа "Красин" составляет 16,8% стоимости нового.
Технологии наплавки
При осуществлении того или иного процесса наплавки происходит оплавление поверхности металла - основы, расплавление присадочного материала, соединение их и кристаллизация образовавшейся смеси. Соотношение долей основного и присадочного металлов в наплавленном слое определяет его состав, микроструктуру и свойства. При восстановительной наплавке нелегированным металлом доля основного металла не оказывает существенного влияния на свойства наплавленного слоя. Напротив, при упрочняющей наплавке легированным металлом увеличение доли основного металла приводит к ухудшению свойств наплавленного слоя.
Ручную электродуговую наплавку выполняют на постоянном и переменном токе штучными неплавящимися или плавящимися электродами. В качестве неплавящегося электрода чаще всего используют графитовые (угольные) стержни. На наплавляемую поверхность наносят слой наплавочной смеси или пасты соответствующего состава и расплавляют теплом дуги. Толщина наплавленного слоя -1-3 мм. Угольным электродом по слою смеси чаще всего наплавляют плоские поверхности. Более распространена наплавка плавящимися покрытыми электродами. Достоинства способа: простота и маневренность; недостатки: низкая производительность (1-3 кг/ч), тяжелые условия труда, снижение усталостной прочности наплавленных деталей.
Достоинствами механизированной наплавки являются: непрерывность процесса, достигаемая в результате использования электродной проволоки или ленты в виде больших мотков; подвод тока к электроду на минимальном расстоянии от дуги, позволяющий применять токи большой силы без перегрева электрода.
Из всех способов механизированной наплавки наибольшее распространение получила наплавка под флюсом. Схема этого способа показана на рис.8. Электродная проволока 1 непрерывно с постоянной скоростью подается в дуговой промежуток. Подвод тока к проволоке осуществляется в непосредственной близости от дуги при помощи втулки 2. В дуге 3 проволока плавится.
Капли металла, пройдя дуговой промежуток, смешиваются с расплавленным металлом изделия 4 и образуют сварочную ванночку 5. После кристалли зации получается наплавленный валик 6, покрытый шлаковой коркой 7 и нерасплавившимся флюсом 8. Избыток флюса ссыпается, а остывшая шлаковая корка удаляется. Формируется однородный наплавленный металл без пор и раковин. Производительность процесса одноэлектродной наплавки под слоем флюса невелика.
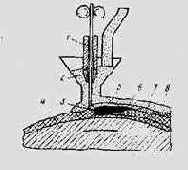
Рис.8
Поэтому наряду с одноэлектродной наплавкой применяют и другие разновидности этого способа: наплавку электродной лентой, многоэлектродную и многодуговую наплавку, наплавку с поперечным колебанием электрода (рис.9,а,б,в,г)
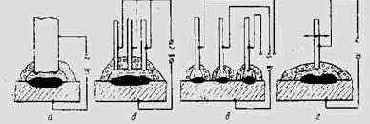
Рис.9
При наплавке электродной лентой (рис.9,а) достигаются малая глубина проплавления основного металла и возможность наплавить за один проход валик шириной до 100 мм. При многоэлектродной наплавке (рис. 9,б) в зону дуги одновременно подаются несколько электродов, подключенных к одному полюсу источника сварочного тока. Дуга периодически перемещается с одного электрода на другой; при этом образуется общая сварочная ванна, формируется широкий валик. При многодуговой наплавке (рис. 9, в) применяется несколько наплавочных аппаратов или один аппарат с изолированными друг от друга несколькими электродами, каждый электрод питается от отдельного источника тока.
При наплавке деталей малого диаметра, глубоких внутренних поверхностей и ряда высоколегированных сплавов затруднено удаление шлаковой корки. Этого недостатка лишена механизированная наплавка открытой дугой и наплавка в защитных газах. При наплавке открытой дугой в качестве электрода используется порошковая проволока. Для защиты металла от кислорода и азота воздуха в ее сердечник вводят, кроме легирующих элементов, газо- и шлакообразующие компоненты и раскислители (при наплавке крупных деталей используют не порошковую проволоку, а ленту). Иногда используют голую легированную проволоку, содержащую в небольших количествах РЗМ
Наплавку в защитных газах чаще выполняют плавящимся электродом. В каче стве защитных газов используют углекислый газ, аргон, азот.
Вибродуговая наплавка.
Схема процесса показана на рис.10. Характерной особенностью способа является применение вибрирующего плавящегося электрода. Электрод в виде голой проволоки подается в дугу специальным аппаратом, который обеспечивает вибрацию электрода вдоль его оси. В результате процесс состоит из циклов, в каждом из которых происходят: 1) замыкание электрода с наплавляемой поверхностью; 2) размыкание и образование дуги; 3) подача электрода к изделию до замыкания. Длительность циклов определяется частотой вибрации электрода. Частота вибрации электродов обычно составляет 30 - 100 пер/с; амплитуда -0,75 - 1,0 диаметра электрода. Производительность вибродуговой наплавки мала (0,5 - 3,0 кг/ч), поэтому восстанавливать этим способом крупные детали с большим износом не рекомендуется. На рис. 10: 1- кассета с электродной проволокой;2 – механизм подачи проволоки; 3 - электромагнит вибратора; 4 - вибрирующий рычаг; 5 - опорный узел; 6 - хоботок; 7 –изделие.

Рис.10
Электрошлаковая наплавка (ЭШН)
Схема процесса показана на рис. 11.
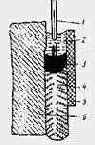
Рис.11
В пространстве, образованном наплавляемой поверхностью 6 и формирующим устройством 5, создается ванна расплавленного флюса-шлака 2, в которую непрерывно подается металлический электрод 1. Ток, проходя между электродом и наплавляемым изделием, нагревает расплавленный шлак и поддерживает высокую температуру и электропроводность. Шлак расплавляет электрод и оплавляет поверхность изделия. Ниже шлаковой ванны образуется металлическая ванна 3, которая, затвердевая, дает слой 4, прочно сплавленный с металлом изделия. Процесс наплавки начинают на графитовых, медных или стальных подкладках. Формирующее устройство в виде охлаждаемого водой медного ползуна медленно перемещается вверх с помощью специального механизма.
При электрошлаковой наплавке в качестве электродов используют проволоку, литые стержни и пластины, трубы, в качестве шлака - флюс АН-25. Благодаря применению больших токов (несколько тысяч ампер) достигают очень высокой производительности - до 150 кг наплавленного металла в час. ЭШН плоских поверхностей может производиться при вертикальном, нижнем и наклонном положениях наплавляемой поверхности.
Для торцовой наплавки деталей сложной формы используется прием стыкошлаковой наплавки (рис.12).
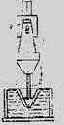
Рис.12
Процесс начинается наведением шлаковой ванны на дне водоохлаждаемой формы. Электродом служит хвостовик детали 1 с приваренной пластиной или прутком из легированного металла 2, которые расплавляются в первую очередь. В момент погружения хвостовика 1 в шлак происходит его разогрев, а затем он погружается в металлическую ванну. Таким образом успешно восстанавливают зубья экскаваторов, сверла и метчики большого диаметра и т.п.
Плазменную наплавку применяют в тех случаях, когда необходимо наплавить слой толщиной от 0,5 до 5,0 мм при строго регламентированной доле основного металла. Применяют несколько разновидностей плазменной наплавки. Присадочный материал нужного состава подают в плазменную дугу или выделенную плазменную струю в виде проволоки, ленты спрессованных металлокерамических колец, пластин, пасты или порошка. На рис.13 показана схема плазменной наплавки с токоведущей присадочной проволокой.
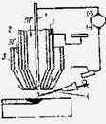
Рис.13
Источником тепла для расплавления присадочной проволоки является двухдуговой разряд. Одна дуга (маломощная) горит между вольфрамовым электродом 1 и соплом 2, вторая (основная) - между вольфрамовым электродом и проволокой 4. Через сопло 3 подается защитный газ. Основной металл разогревается теплом перегретого расплавленного металла проволоки и факелом плазменной струи. По этой схеме наплавляются: бронзы, латуни, нержавеющие стали и т.п.
На рис. 14 показана схема плазменно-порошковой наплавки.
Порошок нужного состава вдувают в дугу через специальные каналы в горелке. Во внутреннем рабочем сопле 2 формируется плазменная струя, по соплу 3 подается присадочный порошок, а по соплу 4 - защитный газ. Источник 5 служит для зажигания дуги между электродом 1 и соплом 2; в плазменной струе этой дуги плавится порошок. Источник 6 формирует плазменную дугу прямого действия, которая оплавляет поверхность изделия и является дополнительным источником тепла для плавления присадочного порошка. Производительность указанных способов невелика (0,5-10 кг наплавленного металла в час). Более высокой производительностью (до 30 кг/час) обладает плазменная наплавка с подачей в ванну двух плавящихся электродов.
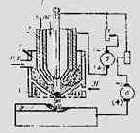
Рис.14
При индукционной наплавке в качестве источника нагрева используются токи высокой частоты. Нагрев осуществляется с помощью индуктора, присоединенного к машинному или ламповому генератору ТВЧ. Практическое применение нашли два способа индукционной наплавки: 1) с использованием твердого присадочного материала, наносимого на наплавляемую поверхность в виде порошка, пасты или прессованных брикетов; 2) с использованием жидкого присадочного материала, расплавляемого в отдельной индукционной печи и определенными порциями подающегося на разогретую поверхность наплавляемой детали. Наплавку твердым присадочным материалом применяют для повышения износостойкости бил и молотков дробилок, лап культиваторов, лемехов плугов (рис.15). На рисунке. 1- деталь, 2 - смесь порошков сплава и флюса, 3 - индуктор. В качестве присадочного материала используют порошок сплава сормайт 1, а также композиции сормайт - релит, сормайт - феррохром. Применяют также индукционную наплавку клапанов двигателей внутреннего сгорания. Присадочный материал в виде литых колец из сплава ВЗК или НХ15С2Р2 укладывают в предварительно проточенную канавку на тарелке клапана, а затем расплавляют с помощью специальных индукторов.

Рис.15
Наплавку жидким присадочным металлом в свою очередь подразделяют на: 1) наплавку заливкой жидкого присадочного сплава; 2) наплавку намораживанием. При наплавке заливкой жидкого металла толщина наплавляемого слоя должна быть более 5 мм, а соотношение массы наплавленного металла к массе металла - основы достигает 30 %. Преимущества этого метода: а) нет необходимости в изготовлении и применении сварочной проволоки, ленты и т.д.; б) возможность наплавки "ненаплавляемых" пар металлов (чугун на чугун, чугун на сталь и др.). При наплавке заливкой жидкого присадочного сплава (рис. 16) наплавляемую деталь 1, поверхность которой покрыта слоем защитного флюса 2, нагревают с помощью индуктора 4 токами высокой частоты и помещают в литейную форму 3; расплавленный металл заливают в пространство между наплавляемой поверхностью и внутренней поверхностью формы. После затвердевания расплав формирует наплавленный слой, имеющий надежное сцепление с металлом - основой.
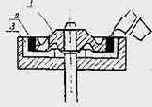
Рис.16
Разновидностью описанного способа является "дуплекс - заливка". При ее осуществлении по наплавляемой поверхности детали, помешенной в литейную форму, перепускают большое количество расплава. В результате этого поверхность разогревается. Последняя порция расплава кристаллизуется на ней и формирует наплавленный слой. Излишки жидкого металла сливают в стоящую рядом с первой литейную форму.
Наплавкой намораживанием (рис.17) компенсируют износы от 0,5 до 3 мм. При ее осуществлении наплавляемую деталь 1 нагревают в тигле с расплавленным шлаком 2, а затем быстро переносят в тигель с расплавленным присадочным металлом 3 и выдерживают в течение 0,5 - 1,5 секунд. За это время на наплавляемой поверхности кристаллизуется ("намораживается") слой указанной толщины.
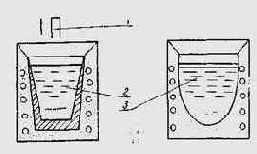
Рис.17
Для надежного сплавления присадочного металла с металлом - основой последний должен быть нагрет до температуры, большей tн:

где tp , tм.о- температура расплава и металла - основы, соответственно; b2, b1 -теплоаккумулирующие способности жидкого и твердого металлов, соответственно.
Восстановительная термообработка
В результате эксплуатации либо предварительной обработки в металле возникают микропоры, микротрещины, являющиеся первопричиной разрушения металла. При этом снижается плотность металла. Степень пораженности порами определяется как отношение уменьшения плотности к ее первоначальному значению:
Dr/r×100%.
Восстановительная термообработка (ВТО) частично или полностью устраняет указанные дефекты металла. Различают: 1) НВТО - низкотемпературную восстановительную термообработку; 2) ВВТО - высокотемпературную восстановительную термообработку; 3) ВТСО - нагрев в сочетании с нагрузкой; 4) ВХТО - нагрев в сочетании с насыщением химическими элементами.
При ВТО происходят изменения трех видов: а) залечивается поврежденность, б) восстанавливается структура; в) изменяется напряженно - деформированное состояние. Предложено несколько объяснений залечивания микронесплошностей: 1) вакансионный механизм рассасывания микронесплошностей; 2) выделение вторичных фаз.
Циклический характер термической обработки (ВЦТО) интенсифицирует как один, так и второй механизм.
Режимы ВТО сталей различных классов
1. Сталь мартенситного класса ЭИ-756 (12 % С, 11 % Сг, 0,78% Мо, 0,17% V, 0,5-0,8 % Мп, 2 % W). ВВТО и ВЦТО по режиму: температура - 1050 °С, общее время - 150 мин, время цикла - 15 мин, охлаждение на воздухе. При Dr/r начальном - 2,13 % после ВВТО Dr/r конечное - 1,26 %; после ВЦТО Dr/r конечное - 0,72 %.
2. Сталь перлитного класса 12Х1МФ (0,13 % С, 1 % Сг, 0,35 % Мо, 0,2 % V, 0,5 % Мп). ВВТО и ВЦТО по режиму: температура - 1000 °С, общее время 150 минут, время цикла -15 минут, охлаждение на воздухе. При Dr/r начальном - 1 % после ВВТО Dr/r конечное - 0,8 %; после ВЦТО Dr/rконечное – 0,4 %.
3. Сталь аустенитного класса 12Х18Н12Т (0,12 % С, 17-19 % Сг, 1-2 % Мп, 11-13 % Ni). ВВТО и ВЦТО по режиму: температура - 1050 °С, общее время 150 минут, время цикла -15 минут, охлаждение на воздухе. При Dr/r начальном - 2,1 % после ВВТО Dr/r конечное - 1,6 %; после ВЦТО Dr/r конечное - 0,8 %.
Восстановление
В зависимости от масштабов производства применяют технологии:
а) подефектную;
б) групповую;
в) маршрутно-групповую;
г) маршрутную.
Подефектная технология предполагает устранение каждого дефекта в отдельности. Комплектование деталей в партии производится только по наименованиям. Групповая технология предполагает комплектование деталей по конструктивным и технологическим особенностям. Групповая технология базируется на следующих принципах:
- общность геометрических форм деталей;
- общность материала, точности обработки, термической обработки;
- наличию однотипных дефектов;
- возможность применения однотипных способов восстановления.
Маршрутная технология предусматривает восстановление одноименных деталей партиями, скомплектованными по наличию общих сочетаний дефектов. Применяется на крупных предприятиях с узкой номенклатурой и большой программой. Маршрутно - групповая технология предусматривает восстановление деталей широкой номенклатуры. При этом детали запускаются партиями.
При восстановлении сопряжений применяют следующие технологии. Восстановление под индивидуальный размер. Более ценную деталь обрабатывают до выведения следов износа. Более простую и дешевую, работающую с ней в паре, изготавливают заново либо наращивают и подгоняют под первую.
Восстановление под ремонтный размер. Эта технология наиболее прогрессивная и распространенная. Более дорогую деталь обрабатывают до определенного (ремонтного) размера. Сопрягаемую деталь изготавливают под этот же (ремонтный) размер. Детали можно изготавливать на разных предприятиях, указывая на чертеже ремонтные размеры. Постановка дополнительных элементов. Изношенные или поврежденные части деталей удаляют, а на их место устанавливают новые; деталь обрабатывают под номинальный размер.
Восстановление деталей наплавкой взрывом
Процесс заключается в следующем. На жесткое основание устанавливают изделие. Над ним располагают пластину присадочного металла, поверх которой укладывают заряд гранулированного взрывчатого вещества. После взрыва детонатора взрывается основной заряд и возникает плоская детонационная волна. Взрыв вызывает соударение пластины присадочного металла с поверхностью изделия и на поверхности контакта возникает давление в десятки тысяч Паскалей. Металл течет, деформируясь пластически. Оксидные пленки дробятся. Перемешивание основного и присадочного металлов отсутствует; тем не менее, образуется металлическая связь дислокационного характера, так как при взрыве протекает совместное пластическое деформирование основного и присадочного металлов.
Наплавку осуществляют на открытых полигонах, в специальных производственных помещениях, вакуумных камерах и др.
Улучшение конечных показателей народного хозяйства
Улучшение конечных показателей народного хозяйства в последнее время приходится достигать без увеличения прироста материальных и трудовых ресурсов. Поэтому ресурсосбережение является важнейшим источником удовлетворения возрастающих потребностей народного хозяйства в сырье, топливе. Вовлечение в оборот вторичных ресурсов называется ресурсосбережением.
Ресурсосбережение предусматривает два пути:
- восстановление изношенных деталей:
- повторное использование материалов и отходов производства.
Долговечность значительной части машин и механизмов находится на уровне, не соответствующем настоящему уровню науки и техники. При этом машины и механизмы зачастую выходят из строя из-за поломки отдельных деталей. Для восстановления их работоспособности необходимо большое количество запасных частей. Например, на предприятиях угольного машиностроения от 30 до 50 % мощностей используется для выпуска запасных частей, на предприятиях сельскохозяйственного машиностроения расход металла при производстве запасных частей в два раза превышает расход металла на изготовление новых машин, а их стоимость примерно в 15 раз превышает стоимость вновь выпускаемых машин.
Ежегодно в различных отраслях промышленности и в сельском хозяйстве изымается из эксплуатации большое количество металла, пластмасс, древесины и т.д. из-за физического, морального износа машин, механизмов. При соответствующей переработке они могут быть повторно использованы.
Ресурсосбережение также связано с понятием безотходного производства. Безотходное производство подразумевает использование как продукции выпускаемой тем или иным предприятием, так и отходов, образующихся на различных стадиях производства. Например, основная продукция МК им. Ильича - металлопрокат и изделия из него, продукция из отходов - материал для отсыпки дорог и изготовления стройматериалов, получаемый из металлургического шлака, товарный графит, получаемый из железографитовой пыли.
Изучаемый курс называется «Восстановление деталей и повторное использование материалов».
Задачи изучения курса:
1) изучить причины выхода из строя различных деталей,
2) научиться устанавливать экономическую и техническую целесообразность проведения восстановительных работ и повторного использования материалов,
3) научиться правильно выбирать технологию восстановления деталей и переработки материалов,
4) освоить методики определения экономической и технической эффективности проведенных операций.
Защитные газы
Для защиты расплавленного металла и дуги при наплавке получили определенное распространение инертные (аргон и гелий) и активные (углекислый газ, кислород, водород) газы. Из них наиболее широко применяют аргон и углекислый газ.
Аргон надежно защищает сварочную зону от соприкосновения с воздухом и не вступает во взаимодействие с расплавленным металлом. Его применяют при наплавке неплавящимся (вольфрамовым) и плавящимся электродами, при плазменной наплавке и напылении. Наплавка в чистом аргоне по существу представляет собой простую переплавку основного и электродного металлов.
Углекислый газ является активным газом. В дуге он частично распадается на оксид углерода и кислород. Поэтому в процессе наплавки происходит интенсивное окисление некоторых примесей, однако обеспечивается надежная защита металла от азота воздуха. Используют углекислый газ при наплавке плавящимся электродом.
В последние годы все более широкое распространение получают смеси инертных и активных газов. Их применение позволяет повысить устойчивость дуги, улучшить формирование шва, уменьшить разбрызгивание и химическое воздействие на металл сварочной ванны (по сравнению с активными газами), повысить плотность наплавленного металла и увеличить производительность процесса.