Неорганическое стекло
Неорганическое стекло следует рассматривать как особого вида затвердевший раствор — сложный расплав высокой вязкости кислотных и основных оксидов.
Стеклообразное состояние является разновидностью аморфного состояния вещества. При переходе стекла из расплавленного жидкого состояния в твердое аморфное в процессе быстрого охлаждения и нарастания вязкости беспорядочная структура, свойственная жидкому состоянию, как бы «замораживается». В связи с этим неорганические стекла характеризуются неупорядоченностью и неоднородностью внутреннего строения.
Стеклообразующий каркас стекла представляет собой неправильную пространственную сетку, образованную кремнекислородными тетраэдрами SiO4.
В состав неорганических стекол входят стеклообразующие оксиды кремния, бора, фосфора, германия, мышьяка, образующие структурную сетку и модифицирующие оксиды натрия, калия, лития, кальция, магния, бария, изменяющие физико-химические свойства стекломассы. Кроме того, в состав стекла вводят оксиды алюминия, железа, свинца, титана, бериллия и др., которые самостоятельно не образуют структурный каркас, но могут частично замещать стеклообразующие оксиды и этим сообщать стеклу нужные технические характеристики. В связи с этим промышленные стекла являются сложными многокомпонентными системами.
Стекла классифицируют по стеклообразующему веществу, по содержанию модификаторов и по назначению.
В зависимости от химической природы стеклообразующего вещества стекла подразделяют на силикатные (SiO2), алюмосиликатные (А12О3— SiO2), боросиликатные (В2О3—SiO2), алюмоборосиликатные (А12О3—В2О3—SiO2), алюмофосфатные (А12О3—Р2О5) и др. По содержанию модификаторов стекла бывают щелочными (содержащими оксиды Na2O, K2O), бесщелочными и кварцевыми. По назначению все стекла подразделяют на технические (оптические, светотехнические, электротехнические, химико-лабораторные, приборные, трубные); строительные (оконные, витринные, армированные, стеклоблоки) и бытовые (стеклотара; посудные, бытовые зеркала и т.
п.).
Технические стекла в большинстве относятся к алюмоборо-силикатной группе и отличаются разнообразием входящих оксидов. Стекла выпускаются промышленностью в виде готовых изделий, заготовок или отдельных деталей.
При нагреве стекло плавится в некото ром температурном интервале, который зависит от состава. Свойства стекла, как и всех аморфных тел, изотропны. Плотность стекла колеблется от 2200 до 6500 кг/м8
(для стекла с оксидами свинца или бария она может достигать 8000 кг/м3).
Механические свойства стекла характеризуются высоким сопротивлением сжатию (500—2000 МПа), низким пределом прочности при растяжении (30-90 МПа) и изгибе (50-150 МПа). Модуль упругости высокий (45—100 МПа).
Важнейшими специфическими свойствами стекол являются их оптические свойства: светопрозрачность, отражение, рассеяние, поглощение и преломление света. Обычное неокрашенное листовое стекло пропускает до 90 %, отражает примерно 8 % и поглощает около 1 % видимого и частично инфракрасного света; ультрафиолетовое излучение поглощается почти полностью. Кварцевое стекло является прозрачным для ультрафиолетового излучения. Коэффициент преломления стекол составляет 1,47—1,96.
Термостойкость стекла характеризует его долговечность в условиях разных изменений температуры. Она определяется разностью температур, которую стекло может выдержать без разрушения при его резком охлаждении в воде. Для большинства видов стекол термостойкость колеблется от 90 до 170°С, а для кварцевого стекла она составляет 800-1000 °С. Химическая стойкость стекол зависит от образующих их компонентов: оксиды SiO2, ZrO2, TiO2, В2О6, А12Оа, CaO, MgO, ZnO обеспечивают высокую химическую стойкость, а оксиды Li2O, Na2O, K2O и BaO, наоборот, способствуют химической коррозии стекла. Механическая прочность и термостойкость стекла могут быть повышены путем закалки и термического упрочнения.
Закалка заключается в нагреве стекла и последующем быстром и равномерном охлаждении в потоке воздуха или в масле.
При этом сопротивление статическим нагрузкам увеличивается в 3—6 раз, ударная вязкость в 5— 7 раз. При закалке повышается также термостойкость стекла.
Термохимическое упрочнение основано на глубоком изменении структуры стекла и свойств его поверхности. Стекло подвергается закалке в подогретых кремнийорганических жидкостях, в результате чего на поверхности материала образуются полимерные пленки; этим создается дополнительное, по сравнению с результатом обычной закалки, упрочнение. Повышение прочности и термостойкости можно получить травлением закаленного стекла плавиковой кислотой, в результате чего удаляются поверхностные дефекты, снижающие его качество.
Силикатные триплексы представляют собой два листа закаленного стекла (толщиной 2—3 мм), склеенные прозрачной эластичной полимерной пленкой. При разрушении триплекса образовавшиеся неострые осколки удерживаются на полимерной пленке. Триплексы бывают плоскими и гнутыми.
Термопан — трехслойное стекло, состоящее из двух стекол и воздушного промежутка между ними. Эта воздушная прослойка обеспечивает теплоизоляцию.
Применение технических стекол. Для остекления транспортных средств используют преимущественно триплексы, термопан и закаленные стекла.
Оптические стекла, применяемые в оптических приборах и инструментах, подразделяют на кроны, отличающиеся малым преломлением, и флинты — с высоким содержанием оксида свинца и большими значениями коэффициента преломления.
Остекление кабин и помещений, где находятся пульты управления мартеновских и дуговых печей, прокатных станов и подъемных кранов в литейных цехах, выполняется стеклами, содержащими оксиды железа и ванадия, которые поглощают около 70 % инфракрасного излучения в интервале длин волн 0,7—3 мкм.
Кварцевое стекло вследствие высокой термической и химической стойкости применяют для изготовления тиглей, чаш, труб, наконечников, лабораторной посуды. Близкое по свойствам к кварцевому стеклу, но более технологичное кварцоидное (кремнеземное) стекло используют для электроколб, форм для точного литья и т.д.
Неполярные и слабополярные термопласты
Неполярными или слабополярными являются полимеры с симметричной структурой молекул или со слабополярными связями, например С—Н.
Полиэтилен (продукт полимеризации этилена) стал одним из самых распространенных пластиков. Это объясняется тем, что в нем высокие электроизоляционные характеристики сочетаются с достаточной механической прочностью, стойкостью к нагреву и низким температурам, действию влаги, кислот и щелочей, хорошей перерабатываемостью и сравнительно низкой стоимостью ввиду доступности сырья.
Основными недостатками полиэтилена является склонность к старению (окислению), особенно при нагреве, и горючесть. Первый недостаток устраняется присадками антистарителей (ароматические амины, сажа и др.). Для уменьшения горючести вводят в состав массы трехокись сурьмы или совмещают полимер с хлорированными углеводородами.
Полипропилен. Его недостатком является более высокая чувствительность к действию кислорода в атмосферных условиях. Он быстрее стареет. Во избежание старения его стабилизируют аминами и газовой сажей.
Полистирол. Являясь продуктом полимеризации стирола, представляет собой бесцветную прозрачную смолу с малым удельным весом и высокими электроизоляционными свойствами. При нормальной температуре полистирол прочнее полиэтилена ?в=50-60 МН/м2, но отличается малой нагревостойкостью (~75-80°С) и склонен к растрескиванию. Это основные недостатки полистирола.
Полистирол стоек к действию кислот (кроме азотной), щелочей и озона. Он мало изменяет свои характеристики под действием влаги, но на открытом воздухе (особенно под влиянием света) постепенно желтеет и легко растрескивается. Полистирол обладает высокой прозрачностью (до 95%) и высоким коэффициентом преломления (n=1,60), что позволяет использовать его в качестве оптических стекол. Он, в частности, применяется для остекления строевых огней.
Полистирол широко применяют для изготовления высокочастотных пластмасс, пленок, лаков и т. д. Разнообразно применение сополимеров, содержащих полистирол.
Политетрафторэтилен (фторопластом-4) представляет собой молочно-белый, жирный на ощупь продукт. Многие отличительные свойства фторопластов связаны с высокой энергией связи С—F, равной 450 кДж/моль.
Ввиду высокой энергии этой связи фторопласт имеет неразветвленные линейные молекулы. Необлученный фторопласт является одним из самых стойких веществ. На него практически не действуют ни кислоты, ни щелочи, ни органические вещества. Он не горюч, не смачивается водой и отличается исключительно высокой влагостойкостью. Он разрушается только под действием жидких щелочных металлов и растворяется при высокой температуре (~270°С) в перфторированных керосинах. Электроизоляционные качества фторопласта-4 очень высоки и мало изменяются при изменении температуры и рабочей частоты.
Недостатками фторопласта-4 являются холодная текучесть, увеличивающаяся при механических нагрузках, и низкая короностойкость. При высокой температуре, начиная с 250°С, происходит термическая деструкция фторопласта-4, которая протекает особенно интенсивно начиная с 400° С. Некоторые продукты деструкции весьма токсичны.
Непрерывное литье
Достоинства этого метода в том, что допустима неограниченная длина отливки, также осуществима высокая производительность.
Недостатки этого метода – форма изделий представляет собой деталь с однородным сечением.
Несамопроизвольная кристаллизация
В реальных условиях процессы кристаллизации и характер образующейся структуры в значительной мере зависят от имеющихся готовых центров кристаллизации. Такими центрами, как правило, являются тугоплавкие частицы неметаллических включений, оксидов, интерметаллических соединений, образуемых примесями. К началу кристаллизации центры находятся в жидком металле в виде твердых включений. При кристаллизации атомы металла откладываются на активированной поверхности примеси, как на готовом зародыше. Такая кристаллизация называется несамопроизвольной или гетерогенной. При несамопроизвольной кристаллизации роль зародышей могут играть и стенки формы.
Наличие готовых центров кристаллизации приводит к уменьшению размера кристаллов при затвердевании. Эффект измельчения структуры значительно увеличивается при соблюдении структурного и размерного соответствия примесной фазы с основным металлом, которое способствует сопряжению их кристаллических решеток.
В жидком металле могут присутствовать и растворенные примеси, которые также вызывают измельчение структуры. Адсорбируясь на поверхности зарождающихся кристаллов, они уменьшают поверхностное натяжение на границе раздела жидкость - твердая фаза и линейную скорость роста кристаллов. Это способствует уменьшению Акр и появлению новых зародышей, способных к росту. Примеси, понижающие поверхностное натяжение, называют поверхностно-активными.
Общие требования, предъявляемые к конструкционным материалам
Конструкционными называют материалы, предназначенные для изготовления деталей машин, приборов, инженерных конструкций, подвергающиеся механическим нагрузкам. Делали машин и приборов характеризуются большим разнообразием форм, размеров, условий эксплуатации. Они работают при статических, циклических и ударных нагрузках, при низких и высоких температурах, в контакте с различными средами. Эти факторы определяют требования к конструкционным материалам, основные из которых эксплуатационные, технологические и экономические.
Эксплуатационные требования имеют первостепенное значение. Для того, чтобы обеспечить работоспособность конкретных машин и приборов, конструкционный материал должен иметь высокую конструкционную прочность.
Конструкционной прочностью называется комплекс механических свойств, обеспечивающих надежную и длительную работу материала в условиях эксплуатации.
Механические свойства, определяющие конструкционную прочность и выбор конструкционного материала, рассмотрены ниже. Требуемые характеристики механических свойств материала для конкретного изделия зависят не только от силовых факторов, но и воздействия на него рабочей среды и температуры.
Среда - жидкая, газообразная, ионизированная, радиационная, в которой работает материал, оказывает существенное и преимущественно отрицательное влияние на его механические свойству, снижая работоспособность деталей. В частности, рабочая среда может вызывать повреждение поверхности вследствие коррозионного растрескивания, окисления и образования окалины, изменение химического состава поверхностного слоя в результате насыщения нежелательными элементами. Кроме того, возможны разбухание и местное разрушение материала в результате ионизационного и радиационного облучения. Для того чтобы противостоять рабочей среде, материал должен обладать не только механическими, но и определенными физико-химическими свойствами: стойкостью к электрохимической коррозии, жаростойкостью, радиационной стойкостью, влагостойкостью, способностью работать в условиях вакуума и др.
В некоторых случаях важно также требование определенных магнитных, электрических, тепловых свойств, высокой стабильности размеров деталей (особенно высокоточных деталей приборов).
Технологические требования направлены на обеспечение наименьшей трудоемкости изготовления деталей и конструкций. Технологичность материала характеризуют возможные методы его обработки. Она оценивается обрабатываемостью резанием, давлением, свариваемостью, способностью к литью, а также прокаливаемостью, склонностью к деформации и короблению при термической обработке. Технологичность материала имеет важное значение, так как от нее зависят производительность и качество изготовления деталей.
Экономические требования сводятся к тому, чтобы материал имел невысокую стоимость и был доступным. Стали и сплавы по возможности должны содержать минимальное количество легирующих элементов. Использование материалов, содержащих легирующие элементы, должно быть обосновано повышением эксплуатационных свойств деталей. Экономические требования, так же как и технологические, приобретают особое значение при массовом масштабе производства.
Таким образом, качественный конструкционный материал должен удовлетворять комплексу требований.
Определения и классификация
Термической обработкой называют технологические процессы, состоящие из нагрева и охлаждения металлических изделий с целью изменения их структуры и свойств. Термической обработке подвергают слитки, отливки, полуфабрикаты, сварные соединения, детали машин, инструменты. Основные виды термической обработки - отжиг, закалка, отпуск и старение. Каждый из указанных видов имеет несколько разновидностей.
Отжиг - термическая обработка, в результате которой металлы или сплавы приобретают структуру, близкую к равновесной: отжиг вызывает разупрочнение металлов и сплавов, сопровождающееся повышением пластичности и снятием остаточных напряжений. Температура нагрева при отжиге зависит от состава сплава и конкретной разновидности отжига; скорость охлаждения с температуры отжига обычно невелика, она лежит в пределах 30-200°С/ч.
Закалка - термическая обработка, в результате которой в сплавах образуется неравновесная структура. Неравновесные структуры при термической обработке можно получить только в том случае, когда в сплавах имеются превращения в твердом состоянии: переменная растворимость, полиморфные превращения твердых растворов, распад высокотемпературного твердого раствора по эвтектоидной реакции и др. Для получения неравновесной структуры сплав нагревают выше температуры фазового превращения в твердом состоянии, после чего быстро охлаждают, чтобы предотвратить равновесное превращение при охлаждении. Для охлаждения используют различные жидкости, отраженные в таблице:
Охлаждающая среда | Температура
охлаждающей среды, оС |
Вода | 20 - 80 |
10%-ный раствор в воде: NaCl, NaOH | 20 |
Масло минеральное | 20-200 |
Конструкционные и инструментальные сплавы закаливают для упрочнения. Сильно упрочняются при закалке сплавы, претерпевающие в равновесных условиях эвтектоидное превращение. Прочность возрастает либо вследствие мартенситного фазового перехода, либо вследствие понижения температуры эвтектоидной реакции, приводящих к измельчению зерен, образующих эвтектоидную смесь.
Если в результате закалки при температуре 20-25°С фиксируется состояние высокотемпературного твердого раствора, значительного упрочнения сплава непосредственно после закалки не происходит; основное упрочнение создается при повторном низкотемпературном нагреве или во время выдержки при температуре 20-25°С.
Отпуск и старение — термическая обработка, в результате которой в предварительно закаленных сплавах происходят фазовые превращения, приближающие их структуру к равновесной.
Сочетание закалки с отпуском или старением практически всегда предполагает получение более высокого уровня свойств (твердости, характеристик прочности, коэрцитивной силы, удельного электрического сопротивления и др.) по сравнению с отожженным состоянием.
В большинстве сплавов после закалки получают пересыщенный твердый раствор. В этом случае основной процесс, происходящий при отпуске или старении,— распад пересыщенного твердого раствора. Температуру и выдержку выбирают таким образом, чтобы равновесное состояние сплава при обработке не достигалось, как это происходит при отжиге. Скорость охлаждения с температуры отпуска или старения за редким исключением не влияет на структуру и свойства сплавов.
Термин “отпуск” используют обычно применительно к сталям и другим сплавам, испытывающим при закалке полиморфное превращение. Термин “старение”-применительно к сплавам, не претерпевающим при закалке полиморфного превращения.
Любой технологический процесс термической обработки состоит из трех основных этапов: нагрев, изотермическая выдержка и охлаждение. Нагрев, а иногда и весь процесс термической обработки (отжиг) проводят в термических печах.
Термическую обработку применяют, например, для уменьшения остаточных напряжений в изделиях, рекристаллизации пластически деформированных полуфабрикатов, уменьшения внутрикристаллической ликвации в слитках или отливках.Соответствующие операции термической обработки являются разновидностями отжига: отжиг (нагрев) для уменьшения напряжений, рекристаллизационный отжиг, диффузионный отжиг (гомогенизация). Состояние сплавов после теплового воздействия становится более равновесным.
Органические полимеры
Органическими называют обширный класс веществ, содержащих в своей основе углерод. Кроме углерода в этих веществах содержится обычно водород, кислород, азот, сера, фосфор. Соединения, в которых содержатся также и другие элементы, называют элементоорганическими. Органические вещества обладают молекулярной структурой, т. е. состоят из отдельных молекул, внутри которых атомы связаны преимущественно весьма прочными ковалентными связями. Между собой молекулы связаны сравнительно слабыми поляризационными силами.
Большинство органических веществ не содержит свободных электронов и ионов, поэтому они являются диэлектриками. Так как силы поляризационной связи между отдельными молекулами невелики, то органические вещества с малой молекулярной массой являются при обычной температуре газами или жидкостями. Вещества с более высокой молекулярной массой являются твердыми уже при обычной температуре.
Ввиду поляризационного характера связи, обусловливающего большие расстояния между молекулами, и малого атомного веса элементов, образующих органические соединения, они отличаются невысоким удельным весом. Поляризационный характер связи определяет также невысокую механическую прочность. Органические вещества сравнительно легкоплавки и за некоторыми исключениями отличаются низкой нагревостойкостью. Подавляющее большинство из них горючи. Легкое горение органических веществ объясняется тем, что связи атомов углерода между собой и с водородом в молекулах органических веществ значительно менее прочным, чем связи углерода и водорода с кислородом. Поэтому при реакциях окисления выделяется большое количество тепла, которое разлагает органические вещества перед горением, облегчая их реакцию с кислородом. Горению органических веществ благоприятствует и то, что конечные продукты их окисления — газы легко удаляются от очага горения и не препятствуют его развитию.
Легкая горючесть большинства органических материалов является их существенным недостатком.
Однако в последнее время получен ряд плохо горючих или негорючих элементоорганических соединений. Так, замена водорода органических веществ фтором практически полностью препятствует их воспламенению или горению. Хлор, вводимый в больших количествах в органические вещества, также препятствует их горению и гасит пламя, обрывая развитие цепных реакций горения. Существенно затрудняется горючесть и при образовании кремнийорганических соединений. Различия в свойствах отдельных органических веществ объясняются различиями в их составе и строении.
Особенно широкое распространение в качестве электроизоляционных материалов получили полимеры.
По происхождению полимеры могут быть природными материалами (целлюлоза, натуральный каучук, янтарь и др.) или синтетическими продуктами (бакелит, полистирол, полиэтилен и др.). Они приобретают все возрастающее значение в технике и быту благодаря удачному сочетанию многих важных качеств, особенно у новых синтетических высокополимеров. Часто они отличаются высокими электроизоляционными свойствами в широком диапазоне рабочих напряжений и частот (вплоть до СВЧ), при высокой влажности окружающей среды и в широком интервале рабочих температур. Они обладают также хорошими тепло- и звукоизоляционными свойствами. Как правило, не подвержены коррозии, гниению и во многих случаях отличаются высокой химической стойкостью.
Ввиду малой плотности, сочетающейся с достаточной прочностью, на основе полимеров можно получить материалы (пластмассы, ткани) с высокой удельной прочностью. Многие полимеры отличаются ценными специальными свойствами: прозрачностью, радиопрозрачностью, диамагнетизмом, антифрикционными свойствами, высокой эластичностью и т. д.
Большинство полимеров легко поддаются различным видам технологической обработки (литье, прессование, вытяжка, обработка резанием, распыление и т. д.) и на их основе производят весьма разнообразные по свойствам продукты: пластмассы и резины, электроизоляционные лаки и лакокрасочные материалы, клеи, компаунды, волокнистые и пленочные материалы.Они находят широкое применение в промышленности и в быту.
Большинство полимеров может быть получено из дешевого сырья — природных и попутных газов нефтедобычи и переработки нефти, угля в сочетании с водой и воздухом. Поэтому производство полимерных материалов развивается быстрыми темпами.
По структуре полимеры делятся на линейные, линейно-разветвленные и сетчатые: аморфные, кристаллитные и кристаллитно-ориентированные.

Основные виды полимерных молекул и структур полимерных материалов. Молекулы - линейные (а), разветвленные (б), сетчатые (в); структуры - аморфные (г), кристаллитные (3), кристаллитно-ориентированные (е).
Органоволокниты
Органоволокниты представляют собой композиционные материалы, состоящие из полимерного связующего и упрочнителей (наполнителей) в виде синтетических волокон. Такие материалы обладают малой массой, сравнительно высокими удельной прочностью и жесткостью, стабильны при действии знакопеременных нагрузок и резкой смене температуры. Для синтетических волокон потери прочности при текстильной переработке небольшие; они малочувствительны к повреждениям.
В органоволокнитах значения модуля упругости и температурных коэффициентов линейного расширения упрочнителя и связующего близки. Происходит диффузия компонентов связующего в волокно и химическое взаимодействие между ними. Структура материала бездефектна. Пористость не превышает 1-3 % (в других материалах 10-20 %). Отсюда стабильность механических свойств органоволокнитов при резком перепаде температур, действии ударных и циклических нагрузок. Ударная вязкость высокая (400-700 кДж/м2). Недостатком этих материалов является сравнительно низкая прочность при сжатии и высокая ползучесть (особенно для эластичных волокон).
Органоволокниты устойчивы в агрессивных средах и во влажном тропическом климате; диэлектрические свойства высокие, а теплопроводность низкая. Большинство органоволокнктов может длительно работать при температуре 100—150°С, а на основе полиимидного связующего и полиоксадиазольных волокон — при 200—300°С.
Пластичность и хрупкость. Твердость
Способность материала получать большие остаточные деформации, не разрушаясь, носит название пластичности. Свойство пластичности имеет решающее значение для таких технологических операций, как штамповка, вытяжка, волочение, гибка и др. Мерой пластичности является удлинение ? при разрыве. Чем больше ?, тем более пластичным считается материал. К числу весьма пластичных материалов относятся отожженная медь, алюминий, латунь, малоуглеродистая сталь и др. Менее пластичными являются дюраль и бронза. К числу слабо пластичных материалов относятся многие легированные стали.
Противоположным свойству пластичности является свойство хрупкости, т. е. способность материала разрушаться без образования заметных остаточных деформаций. Материалы, обладающие этим свойством, называются хрупкими. Для таких материалов величина удлинения при разрыве не превышает 2—5%, а в ряде случаев измеряется долями процента. К хрупким материалам относятся чугун, высокоуглеродистая инструментальная сталь, стекло, кирпич, камни и др. Диаграмма растяжения хрупких материалов не имеет площадки текучести и зоны упрочнения.
![]() |
Кривые растяжения материалов: а-хрупкого, б-пластичного
![]() |
По-разному ведут себя пластичные и хрупкие материалы и при испытании на сжатие. Испытание на сжатие производится на коротких цилиндрических образцах, располагаемых между параллельными плитами. Диаграмма сжатия образца имеет вид кривой, показанной на рисунке.
Здесь, как и для растяжения, обнаруживается площадка текучести с последующим переходом к зоне упрочнения. В дальнейшем, однако, нагрузка не падает, как при растяжении, а резко возрастает. Происходит это в результате того, что площадь поперечного сечения сжатого образца увеличивается; сам образец вследствие трения на торцах принимает бочкообразную форму. Довести образец пластического материала до разрушения практически не удается. Испытуемый цилиндр сжимается в тонкий диск и дальнейшее испытание ограничивается возможностями машины. Поэтому предел прочности при сжатии для такого рода материалов найден быть не может.
Иначе ведут себя при испытании на сжатие хрупкие материалы. Диаграмма сжатия этих материалов сохраняет качественные особенности диаграммы растяжения. Предел прочности хрупкого материала при сжатии определяется так же, как и при растяжении. Разрушение образца происходит с образованием трещин по наклонным или продольным плоскостям.
Сопоставление предела прочности хрупких материалов при растяжении с пределом прочности при сжатии показывает, что эти материалы обладают, как правило, более высокими прочностными показателями при сжатии, нежели при растяжении. Существуют материалы, способные воспринимать при растяжении большие нагрузки, чем при сжатии. Это обычно материалы, имеющие волокнистую структуру, — дерево и некоторые типы пластмасс. Этим свойством обладают и некоторые металлы, например магний.
Полиморфизм

Железо, титан, кобальт, олово, углерод, сегнетоэлектрики, кварц и многие другие материалы могут существовать в различных полиморфных модификациях.
Естественно, полиморфные, модификации отличаются между собой не только структурой, но и свойствами. Например, ?-олово, устойчивое ниже 13° С, является хрупким полупроводником, а ?-олово— весьма вязкий металл.

Полиморфизм играет в материаловедении и технологии важную практическую роль. Переводя материал из одной полиморфной модификации в другую, можно управлять его свойствами. Например, практически освоено получение алмазов из графита нагревом его под давлением 100000 атм. до температур примерно 2000° С.
Полярные термопласты
Полярными являются полимеры с несимметричной структурой молекул, которым присущи собственные дипольные моменты. Одной из основных особенностей полярных диэлектриков по сравнению с неполярными являются значительно более высокие. Поэтому, как правило, они не пригодны для изоляции в цепях высоких и сверхвысоких частот. Их часто называют низкочастотными диэлектриками.
Вследствие полярности они легче притягивают влагу и полярные примеси. Большинство из них смачиваются водой. Удельное электросопротивление у этих материалов обычно ниже, чем у неполярных. Многие из них обладают высокой химической стойкостью, высокой механической прочностью и эластичностью. После дополнительной пластификации их нередко применяют в виде гибких резинообразных продуктов.
Полихлорвинил (поливинилхлорид, винипласт) получается полимеризацией хлористого винила. Благодаря асимметричному распределению электроотрицательных атомов хлора он заметно полярен. При нормальной температуре полихлорвинил — твердая хрупкая слегка желтоватая смола, отличающаяся высокой химической устойчивостью. Он стоек против действия воды, кислот и щелочей, озона, спирта, бензина и керосина, но растворим в дихлорэтане, хлорбензоле, частично в ацетоне, бензоле и др. Его нагревостойкость (60—70°) и морозостойкость (-25°) невысоки. Он горит с большим трудом и при устранении внешнего источника пламени гаснет. Его электроизоляционные свойства вполне удовлетворительны, но под воздействием электрических искр полихлорвинил легко разлагается, образует проводящие мостики и выделяет хлористый водород. Полихлорвинил легко окрашивается в разные цвета.
Политрифтормонхлорэтилен (фторопласт-3) отличается от фторопласта-4 тем, что один атом фтора заменен на значительно больший по размеру атом хлора, вследствие чего появляется асимметрия в структуре

т. е. возрастает полярность, уменьшается степень кристалличности, увеличивается диэлектрическая проницаемость и значительно возрастают потери, но удельное электросопротивление, электрическая прочность, дугостойкость и влагостойкость у фторопласта-3 остаются высокими.
Температура плавления понижается примерно до 210° (ниже температуры разложения), чем значительно облегчается переработка материала в изделия. Механическая прочность фторопласта-3 значительно выше, чем фторопласта-4. Применяется фторопласт-3 как химически стойкая, и нагревостойкая изоляция.
Полиэфирные смолы представляют собой продукты конденсации многоосновных кислот и спиртов. Двухосновные кислоты при полимеризации с двухатомными спиртами дают линейные термопластичные полимеры. Например, при конденсации терефталевой кислоты с этиленгликолем образуется получивший в последнее время широкое применение продукт — полиэтилентерефталат, или лавсан.
Полимер содержит 65—75% кристаллической фазы, имеет температуру плавления около 240—260°С. Полиэтилентерефталат отличается хорошими диэлектрическими свойствами. Он весьма влагостоек и отличается высоким поверхностным электросопротивлением во влажной атмосфере.
Важной особенностью полиэтилентерефталата является его высокая механическая прочность в ориентированных полимерах, достигающая 350-450 МН/м2. Полиэтилентерефталат применяется чаще всего в виде волокнистой и пленочной изоляции для электрических машин и конденсаторов. Из полиэтилентерефталатовой пленки готовят также аэростаты.
Получение монокристаллов
Большое научное и практическое значение имеют монокристаллы. Монокристаллы отличаются минимальными структурными несовершенствами. Получение монокристаллов позволяет изучать свойства металлов, исключив влияние границ зерен. Применение в монокристаллическом состоянии германия и кремния высокой чистоты дает возможность использовать их полупроводниковые свойства и свести к минимуму неконтролируемые изменения электрических свойств.
Монокристаллы можно получить, если создать условия для роста кристалла только из одного центра кристаллизации. Существует несколько методов, в которых использован этот принцип. Важнейшими из них являются методы Бриджмена и Чохральского.
Метод Бриджмена (рис. а) состоит в следующем: металл, помещенный в тигель с коническим дном 3, нагревается в вертикальной трубчатой печи 1 до температуры на 50-100 °С выше температуры его плавления. Затем тигель с расплавленным металлом 2 медленно удаляется из печи. Охлаждение наступает в первую очередь в вершине конуса, где и появляются первые центры кристаллизации. Монокристалл 4 вырастает из того зародыша, у которого направление преимущественного роста совпадает с направлением перемещения тигля. При этом рост других зародышей подавляется. Для непрерывного роста монокристалла необходимо выдвигать тигель из печи со скоростью, не превышающей скорость кристаллизации данного металла.
![]() |
Схемы установок для выращивания монокристаллов
Метод Чохральского (рис. б) состоит в вытягивании монокристалла из расплава. Для этого используется готовая затравка 2 - небольшой образец, вырезанный из монокристалла по возможности без структурных дефектов. Затравка вводится в поверхностный слой жидкого металла 4, имеющего температуру чуть выше температуры плавления. Плоскость затравки, соприкасающаяся с поверхностью расплава, должна иметь кристаллографическую ориентацию, которую желательно получить в растущем монокристалле 3 для обеспечения наибольших значений тех или иных свойств.
Затравку выдерживают в жидком металле для оплавления и установления равновесия в системе жидкость-кристалл. Затем затравку медленно, со скоростью, не превышающей скорости кристаллизации, удаляют из расплава. Тянущийся за затравкой жидкий металл в области более низких температур над поверхностью ванны кристаллизуется, наследуя структуру затравки. Для получения симметричной формы растущего монокристалла и равномерного распределения примесей в нем ванна 5 с расплавом вращается со скоростью до 100 об/мин, а навстречу ей с меньшей скоростью вращается монокристалл.
Диаметр растущего монокристалла зависит от скорости выращивания и температуры расплава. Увеличение скорости выращивания ведет к выделению большей теплоты кристаллизации, перегреву расплава и уменьшению диаметра монокристалла, и, наоборот, уменьшение скорости выращивания приводит к уменьшению количества теплоты кристаллизации, понижению температуры расплава и увеличению диаметра монокристалла.
Полупроводниковые лазеры (КПД > 90%)
В последние годы интенсивно развиваются работы по созданию полупроводниковых источников когерентного излучения — полупроводниковых лазеров, которые открывают возможность непосредственного преобразования энергии электрического тока в энергию когерентного излучения.
![]() |
На рис. а сплошной линией показана кривая распределения электронов, отвечающая равновесному состоянию, пунктиром — неравновесному состоянию, при котором концентрация электронов в зоне проводимости и дырок в валентной зоне выше равновесной. Заполнение зон электронами, соответствующее такому инверсионному состоянию, показано на рис. б. Особенность его заключена в том, что кванты света с энергией, равной ширине запрещенной зоны, поглощаться системой не могут. Поглощение такого кванта должно сопровождаться переводом электрона с верхнего уровня валентной зоны на нижний уровень зоны проводимости. Так как на верхнем уровне валентной зоны электронов практически нет, а на нижнем уровне зоны проводимости нет свободных мест, то вероятность подобного процесса весьма низка. Это создает благоприятные условия для протекания стимулированного излучения и нарастания фотонной лавины. Квант света стимулирует рекомбинацию электрона и дырки (n-переход), сопровождающуюся рождением точно такого же кванта. Так как эти кванты практически не поглощаются системой, то в дальнейшем они оба участвуют в возбуждении стимулированного излучения, порождая два новых кванта, и т. д. Для того чтобы заставить один и тот же фотон участвовать в возбуждении стимулированного излучения многократно, на противоположных стенках рабочего тела лазера помещают строго параллельные одно другому зеркала (рис. в), которые отражают падающие на них фотоны и возвращают их в рабочий объем лазера. Усилению подвергаются только те фотоны, которые движутся практически строго вдоль оси, так как только эти фотоны испытывают многократные отражения от зеркал. Все другие фотоны выбывают из рабочего объема либо сразу, либо после незначительного числа отражений. В результате возникает остронаправленное излучение вдоль оси, характеризующееся высокой степенью монохроматичности.
Полупроводниковые лазеры обладают высоким к. п. д., который приближается к 100%. Другим замечательным свойством полупроводниковых лазеров является возможность прямой модуляции когерентного излучения изменением тока, текущего через p-n-переход. Это позволяет применять полупроводниковые лазеры для целей связи и телевидения.
Поверхностно-пластическая деформация
Дробеструйный наклёп

Упрочнение поверхности,
снятие поверхностных напряжений.
Центробежный шариковый наклёп

Превращения в сплавах системы железо-цементит
Диаграмма состояния Fe-Fe3C характеризует фазовый состав и превращения в системе железо - цементит (6,69 % С). Особенность диаграммы - наличие на оси составов двух шкал, показывающих содержание углерода и цементита. Координаты характерных точек диаграммы приведены в таблице. Точка А определяет температуру плавления чистого железа, а точка D - температуру плавления цементита. Точки N и G соответствуют температурам полиморфных превращений железа. Точки H и Р характеризуют предельную концентрацию углерода соответственно в высокотемпературном и низкотемпературном феррите. Точка Е определяет наибольшую концентрацию углерода в аустените. Значения остальных точек будут ясны после проведенного анализа диаграммы.
Обозначение точки на диаграмме | Температура,
°С |
Концентрация углерода, % |
А
Н J В N D Е С F G Р S К |
1539 1499 1499 1499
1392 1260 1147 1147 1147 911 727 727 727 |
0
0,1 0,16 0,51 0 6,69 2,14 4,3 6,69 0 0,02 0,8 6,69 |
![]() ![]() |
|
Превращения в сплавах системы Fe-Fe3C происходят как при затвердевании жидкой фазы, так и в твердом состоянии. Первичная кристаллизация идет в интервале температур, определяемых на линиях ликвидус (ABCD) и солидус (AHJECF). Вторичная кристаллизация вызвана превращением железа одной модификации в другую и переменной растворимостью углерода в аустените и феррите; при понижении температуры эта растворимость уменьшается. Избыток углерода из твердых растворов выделяется в виде цементита. Линии ES и PQ характеризуют изменение концентрации углерода в аустените и феррите соответственно. Цементит имеет почти неизменный состав (двойная вертикальная линия DFKL). Цементит, выделяющийся из жидкости, называют первичным; цементит, выделяющийся из аустенита - вторичным; цементит, выделяющийся из феррита - третичным.
Соответственно линию CD на диаграмме состояния называют линией первичного цементита, ES- линией вторичного цементита; PQ-линией третичного цементита. В системе железо - цементит происходят три изотермических превращения:
перитектическое превращение на линии HJB (1499°С)
ФН + ЖВ>AJ
эвтектическое превращение на линии ECF (1147 °С)
ЖС> [АE + Ц]
эвтектоидное превращение на линии PSK (727 °С)
АS> [ФР + Ц]
Эвтектическая смесь аустенита и цементита называется ледебуритом, а эвтектоидная смесь феррита и цементита - перлитом.
Эвтектоид - перлит (содержит 0,8 %С) и эвтектику-ледебурит (4,3 %С) рассматривают как самостоятельные структурные составляющие, оказывающие заметное влияние на свойства сплавов. Перлит чаще всего имеет пластинчатое строение и является прочной структурной составляющей. При охлаждении ледебурита до температур ниже линии SK входящий в него аустенит превращается в перлит, и при температуре 20-25°С ледебурит представляет собой смесь цементита и перлита. В этой структурной составляющей цементит образует сплошную матрицу, в которой размещены колонии перлита. Такое строение ледебурита служит причиной его большой твердости (> НВ 6000) и хрупкости. Присутствие ледебурита в структуре сплавов обусловливает их неспособность к обработке давлением, затрудняет обработку резанием.
Железоуглеродистые сплавы подразделяют на две группы: стали, содержащие до 2,14%С, и чугуны.
![]() |

![]() |
![]() |
Примесные полупроводники
Полупроводники любой степени чистоты содержат всегда примесные атомы, создающие свои собственные энергетические уровни, получившие название примесных уровней. Эти уровни могут располагаться как в разрешенной, так и в запрещенной зонах полупроводника на различных расстояниях от вершины валентной зоны и дна зоны проводимости. В ряде случаев примеси вводят сознательно для придания полупроводнику необходимых свойств. Рассмотрим основные типы примесных уровней.
Донорные уровни. Предположим, что в кристалле германия часть атомов германия замещена атомами пятивалентного мышьяка. Германий имеет решетку типа алмаза, в которой каждый атом окружен четырьмя ближайшими соседями, связанными с ним валентными силами (рис. а). Для установления связи с этими соседями атом мышьяка расходует четыре валентных электрона; пятый электрон в образовании связи не участвует. Он продолжает двигаться в поле атома мышьяка.

На языке зонной теории этот процесс можно представить следующим образом. Между заполненной валентной зоной и свободной зоной проводимости располагаются энергетические уровни пятого электрона атомов мышьяка (рис. в). Эти уровни размещаются непосредственно у дна зоны проводимости, отстоя от нее на расстоянии Eg ? 0,01 эВ. При сообщении электронам таких примесных уровней энергии Eg они переходят в зону проводимости (рис. г). Образующиеся при этом положительные заряды («дырки») локализуются на неподвижных атомах мышьяка и в электропроводности не участвуют.
Примеси, являющиеся источником электронов проводимости, называются донорами, а энергетические уровни этих примесей — донорными уровнями.
Полупроводники, содержащие донорную примесь, называются электронными полупроводниками, или полупроводниками n-типа, часто их называют также донорными полупроводниками.

На рис. в показана зонная структура германия, содержащего примесь индия. Непосредственно у вершины валентной зоны на расстоянии Еа ? 0,01 эВ располагаются незаполненные уровни атомов индия. Близость этих уровней к валентной зоне приводит к тому, что уже при относительно невысоких температурах электроны из валентной зоны переходят на примесные уровни (рис. г). Связываясь с атомами индия, они теряют способность перемещаться в решетке германия и в проводимости не участвуют. Носителями заряда являются лишь дырки, возникающие в валентной зоне.
Примеси, захватывающие электроны из валентной зоны полупроводника, называют акцепторными, а энергетические уровни этих примесей — акцепторными уровнями. Полупроводники, содержащие также примеси, называются дырочными полупроводниками, пли полупроводниками p-типа; часто их называют акцепторными полупроводниками.
Прямое включение: Обратное включение:


У диодов в качестве одного из основных параметров используют обратный ток Iобр, который измеряют при определенном значении обратного напряжения.
|
Закон изменения тока

![]() |
Прочность конструкционных материалов и критерии ее оценки
Конструкционная прочность - комплексная характеристика, включающая сочетание критериев прочности, надежности и долговечности.
Критерии прочности материала выбирают в зависимости от условий его работы. Критериями прочности при статистических нагрузках являются временное сопротивление или предел текучести, характеризующие сопротивление материала пластической деформации. Поскольку при работе большинства деталей пластическая деформация недопустима, то их несущую способность, как правило, определяют по пределу текучести. Для приближенной оценки статической прочности используют твердость НВ.
Большинство деталей машин испытывает длительные циклические нагрузки. Критерий их прочности - предел выносливости. По величине выбранных критериев прочности рассчитывают допустимые рабочие напряжения. При этом, чем больше прочность материала, тем больше допустимые рабочие напряжения и тем самым меньше размеры и масса детали. Однако повышение уровня прочности материала и, как следствие, рабочих напряжений сопровождается увеличением упругих деформаций.
Для ограничения упругой деформации материал должен обладать высоким модулем упругости (или сдвига), являющимся критерием его жесткости. Именно критерии жесткости, а не прочности обусловливают размеры станин станков, корпусов редукторов и других деталей, от которых требуется сохранение точных размеров и формы.
Возможно и противоположное требование. Для пружин, мембран и других чувствительных упругих элементов приборов, наоборот, важно обеспечить большие упругие перемещения. Для материалов, используемых в авиационной и ракетной технике, важное значение имеет эффективность материала по массе.
Таким образом, в качестве критериев конструкционной прочности выбирают те характеристики, которые наиболее полно отражают прочность в условиях эксплуатации.
Надежность - свойство материала противостоять хрупкому разрушению. Хрупкое разрушение вызывает внезапный отказ деталей в условиях эксплуатации.
Оно считается наиболее опасным из-за протекания с большой скоростью при напряжениях ниже расчетных, а также возможных аварийных последствий.
Для предупреждения хрупкого разрушения конструкционные материалы должны обладать достаточной пластичностью и ударной вязкостью. Однако эти параметры надежности, определенные на небольших лабораторных образцах без учета условий эксплуатации конкретной детали, достаточно показательны лишь для мягких малопрочных материалов. Необходимо также учитывать то, что в условиях эксплуатации действуют факторы, дополнительно снижающие их пластичность, вязкость и увеличивающие опасность хрупкого разрушения. К таким факторам относятся концентраторы напряжений (надрезы), понижение температуры, динамические нагрузки, увеличение размеров деталей.
Для того чтобы избежать внезапных поломок в условиях эксплуатации, необходимо учитывать трещиностойкость материала. Трещиностойкость - группа параметров надежности, характеризующих способность материала тормозить развитие трещины.
Количественная оценка трещиностойкости основывается на линейной механике разрушения. В соответствии с ней очагами разрушения высокопрочных материалов служат небольшие трещины эксплуатационного или технологического происхождения. Трещины являются острыми концентраторами напряжений, местные (локальные) напряжения, в вершине которых могут во много раз превышать средние расчетные напряжения.
Долговечность - свойство материала сопротивляться развитию постепенного разрушения, обеспечивая работоспособность деталей в течение заданного времени. Причины потери работоспособности разнообразны: развитие процессов усталости, изнашивания, ползучести, коррозии, радиационного разбухания и пр. Эти процессы вызывают постепенное накопление необратимых повреждений в материале и его разрушение. Обеспечение долговечности материала означает уменьшение до требуемых значений скорости его разрушения.
Для большинства деталей машин долговечность определяется сопротивлением материала усталостным разрушениям (циклической долговечностью) или сопротивлением изнашиванию.
Поэтому эти причины потери работоспособности материала требуют подробного рассмотрения.
Циклическая долговечность характеризует работоспособность материала в условиях многократно повторяющихся циклов напряжений. Цикл напряжения - совокупность изменения напряжения между двумя его предельными значениями ?max и ?min в течение периода Т.
Процессы постепенного накопления повреждений в материале под действием циклических нагрузок, приводящие к изменению его свойств, образованию трещин, их развитию и разрушению, называют усталостью, а свойство противостоять усталостивыносливостью.
Износостойкость - свойство материала оказывать в определенных условиях трения сопротивление изнашиванию. Изнашивание - процесс постепенного разрушения поверхностных слоев материала путем отделения его частиц под влиянием сил трения. Результат изнашивания называют износом. Его определяют по изменению размеров, уменьшению объема или массы. Износостойкость материала оценивают величиной, обратной скорости изнашивания.
Рекристаллизационный отжиг
Нагрев деформированных полуфабрикатов или деталей выше температуры рекристаллизации называют рекристаллизационным отжигом; в процессе выдержки происходит главным образом рекристаллизация. Скорость охлаждения при этой разновидности отжига не имеет решающего значения; обычно охлаждение по окончании выдержки проводят на спокойном воздухе. Цель отжига - понижение прочности и восстановление пластичности деформированного металла, получение определенной кристаллографической текстуры, создающей анизотропию свойств, и получение заданного размера зерна.
Рекристаллизационный отжиг часто используют в качестве межоперационной смягчающей обработки при холодной прокатке, волочении и других операциях холодного деформирования. Температуру отжига обычно выбирают на 100-200 °С выше температуры рекристаллизации. В некоторых металлах и твердых растворах рекристаллизация сопровождается образованием текстуры (преимущественной ориентации кристаллов в объеме детали), которая создает анизотропию свойств. Это позволяет улучшить те или иные свойства вдоль определенных направлений в деталях. В машиностроении и приборостроении широкое применение находят металлы и сплавы - твердые растворы, не имеющие фазовых превращений в твердом состоянии. В таких материалах единственной возможностью регулирования размера зерен является сочетание холодной пластической деформации с последующим рекристаллизационным отжигом.
Самопроизвольная кристаллизация
Самопроизвольная кристаллизация обусловлена стремлением вещества иметь более устойчивое состояние, характеризуемое уменьшением термодинамического потенциала G. С повышением температуры термодинамический потенциал вещества как в твердом, так и в жидком состоянии уменьшается, что показано на рисунке.

Изменение термодинамического потенциала в зависимости от температуры для металла в твердом и жидком состояниях
Температура, при которой термодинамические потенциалы вещества в твердом и жидком состояниях равны, называется равновесной температурой кристаллизации. Кристаллизация происходит в том случае, если термодинамический потенциал вещества в твердом состоянии будет меньше термодинамического потенциала вещества в жидком состоянии, т. е. при переохлаждении жидкого металла до температур ниже равновесной. Плавление - процесс, обратный кристаллизации, происходит при температуре выше равновесной, т. е. при перегреве. Разница между реальными температурами плавления и кристаллизации называется температурным гистерезисом.
Поскольку жидкий металл с присущим ему ближним порядком в расположении атомов обладает большей внутренней энергией, чем твердый со структурой дальнего порядка, при кристаллизации выделяется теплота. Между теплотой и температурой кристаллизации Тк существует определенная связь. Так как при равновесной температуре кристаллизации термодинамические потенциалы в жидком и твердом состояниях равны, то
|


Параметр ?S = Q/TK характеризует упорядоченность в расположении атомов при кристаллизации. В зависимости от сил межатомной связи теплота кристаллизации для различных металлов изменяется от 2500 Дж/моль (Na, К и др.) до 20000 Дж/моль (W и др.).
Когда кристаллизуется чистый элемент, отвод теплоты, происходящий вследствие охлаждения, компенсируется теплотой кристаллизации.
В связи с этим на кривой охлаждения, изображаемой в координатах температура-время, процессу кристаллизации соответствует горизонтальный участок:

Кривые охлаждения металла
При большом объеме жидкого металла выделяю щаяся при кристаллизации теплота повышает температуру практически до равновесной (кривая а); при малом объеме металла выделяющейся теплоты недостаточно, вследствие чего кристаллизация происходит с переохлаждением по сравнению с равновесной температурой (кривая б).
Разница между равновесной (Ts) и реальной (Тn) температурой кристаллизации называется степенью переохлаждения ?T. Степень переохлаждения зависит от природы металла. Она увеличивается с повышением чистоты металла и с ростом скорости охлаждения. Обычная степень переохлаждения металлов при кристаллизации в производственных условиях колеблется от 10 до 30 °С; при больших скоростях охлаждения она может достигать сотен градусов.
Степень перегрева при плавлении металлов, как правило, не превышает нескольких градусов.
В жидком состоянии атомы вещества вследствие теплового движения перемещаются беспорядочно. В то же время в жидкости имеются группировки атомов небольшого объема, в пределах которых расположение атомов вещества во многом аналогично их расположению в решетке кристалла. Эти группировки неустойчивы, они рассасываются и вновь появляются в жидкости. При переохлаждении жидкости некоторые из них, наиболее крупные, становятся устойчивыми и способными к росту. Эти устойчивые группировки атомов называют центрами кристаллизации (зародышами). Образованию зародышей способствуют флуктуации энергии, т. е. отклонения энергии группировок атомов в отдельных зонах жидкого металла от некоторого среднего значения. Размер образовавшегося зародыша зависит от величины зоны флуктуации.
Появление центров изменяет термодинамический потенциал системы ?Gобщ. С одной стороны, при переходе жидкости в кристаллическое состояние термодинамический потенциал уменьшается на V?G? (G1), с другой стороны, он увеличивается вследствие появления поверхности раздела между жидкостью и кристаллическим зародышем на величину, равную S? (G2):
|
![]() |
где V-объем зародыша; S-поверхность зародыша; ?- удельное поверхностное натяжение на границе кристалл-жидкость; ?G?-удельная разность термодинамических потенциалов при переходе жидкости в кристаллическое состояние.
Изменение термодинамического потенциала при образовании зародышей в зависимости от их размера
Если принять, что зародыш имеет форму куба с ребром А, то общее изменение термодинамического потенциала
|
Отсюда следует, что графическая зависимость изменения термодинамического потенциала от размера зародыша имеет максимум при некотором значении А, названном критическим. Зародыши с размером больше критического вызывают уменьшение ?Gобщ. и поэтому являются устойчивыми, способными к росту. Зародыши, имеющие размер меньше критического, нестабильны и растворяются в жидкости, поскольку вызывают увеличение ?Gобщ.


|


Скорость процесса и окончательный размер кристаллов при затвердевании определяются соотношением скоростей роста кристаллов и образования центров кристаллизации. Скорость образования зародышей измеряется числом зародышей, образующихся в единицу времени в единице объема; скорость роста - увеличением линейного размера растущего кристалла в единицу времени. Оба процесса связаны с перемещениями атомов и зависят от температуры. Графическая зависимость скорости образования зародышей и скорости их роста от степени переохлаждения представлена на рисунке.

Изменение скорости образования зародышей (с. з.) и скорости роста кристаллов (с. р.) в зависимости от степени переохлаждения
Для металлов, которые в обычных условиях кристаллизации не склонны к большим переохлаждениям, как правило, характерны восходящие ветви кривых.Это значит, что при равновесной температуре, когда степень переохлаждения равна нулю, скорость образования зародышей и скорость роста также равны нулю, т. е. кристаллизации не происходит. При небольших степенях переохлаждения, когда велик зародыш критического размера, а скорость образования зародышей мала, при затвердевании формируется крупнокристаллическая структура. Небольшие степени переохлаждения достигаются при заливке жидкого металла в форму с низкой теплопроводностью (земляная, шамотовая) или в подогретую металлическую форму. Увеличение переохлаждения происходит при заливке жидкого металла в холодные металлические формы, а также при уменьшении толщины стенок отливки. Поскольку при этом скорость образования зародышей увеличивается более интенсивно, чем скорость их роста, получаются более мелкие кристаллы.
Силицирование (Si)
Силицированием называется процесс насыщения поверхности стали кремнием. В результате силицирования сталь приобретает высокую коррозионную стойкость в морской воде, в различных кислотах и повышенную износостойкость. Кроме того, силицирование резко повышает окалиностойкость молибдена и некоторых других металлов и сплавов.
Силицированный слой представляет собой твердый раствор кремния в ?-железе. Силицированный слой несмотря на низкую твердость и значительную пористость после пропитки маслом при температуре 170—200° С имеет повышенную износостойкость.
Силицирование можно проводить в порошкообразных смесях, состоящих из 60% ферросилиция, 39% окиси алюминия и 1 % хлористого аммония, но наиболее часто применяют газовое силицирование. При газовом силицировании при температуре 1000°С в течение 2—4 ч образуется слой толщиной 0,5—1,0 мм.
Силицированию подвергают детали, применяемые в оборудовании химической, бумажной и нефтяной промышленности.
В последние годы разработаны и получают промышленное внедрение новые процессы поверхностного насыщения металлов — титанирование и цинкование.
Ситаллы
Ситаллы получают на основе неорганических стекол путем их полной или частичной управляемой кристаллизации. Термин «ситаллы» образован от слов: стекло и кристаллы. За рубежом их называют стеклокерамикой, пирокерамами. По структуре и технологии получения ситаллы занимают промежуточное положение между обычным стеклом и керамикой. От неорганических стекол они отличаются кристаллическим строением, а от керамических материалов — более мелкозернистой и однородной микрокристаллической структурой. Ситаллы подразделяют на фотоситаллы, термоситаллы и шлакоситаллы.

Схема кристаллизации стекла при образовании ситаллов с помощью катализаторов
Фотоситаллы получают из стекол литиевой системы с нуклеа-торами — коллоидными красителями. Фотохимический процесс протекает при облучении стекла ультрафиолетовыми или рентгеновскими лучами, при этом внешний вид стекла не изменяется. Процесс кристаллизации происходит при повторном нагревании изделия.
Термоситаллы получаются из стекол систем MgO—А12О3—CaO—A12O3—SiO2. Кристаллическая структура ситалла создается только в результате повторной термообработки предварительно отформованных изделий.
Структура ситаллов многофазная, состоит из зерен одной или нескольких кристаллических фаз, скрепленных между собой стекловидной прослойкой. Содержание кристаллической фазы колеблется от 30 до 95 % . Размер кристаллов обычно не превышает 1—2 мкм. По внешнему виду ситаллы могут быть непрозрачными и прозрачными.
Шлакоситаллы получают на основе доменных шлаков и катализаторов (сульфаты, порошки железа и др.); вводятся соединения фтора для усиления ситаллизации.
В отличие от обычного стекла, свойства которого определяются в основном его химическим составом, для ситаллов решающее значение имеют структура и фазовый состав. Причина ценных свойств ситаллов заключается в их исключительной мелкозернистости, почти идеальной поликристаллической структуре. Свойства ситаллов изотропны.
В них совершенно отсутствует всякая пористость. Усадка материала при его переработке незначительна. Большая абразивная стойкость делает их малочувствительными к поверхностным дефектам.
Плотность ситаллов лежит в пределах 2400—2950 кг/м8. Прочность ситалла зависит от температуры: до температуры 700—780°С прочность материала уменьшается незначительно, при более высоких температурах быстро падает. Жаропрочность ситаллов под нагрузкой составляет 800—1200 °С. Твердость их приближается к твердости закаленной стали (микротвердость 7000—10500 МПа). Они весьма износостойки. По теплопроводности ситаллы в результате повышенной плотности превосходят стекла. Стеклокристаллические материалы обладают высокой химической устойчивостью к кислотам и щелочам, не окисляются даже при высоких температурах. Они газонепроницаемы и обладают нулевым водопоглощением. Хорошие диэлектрики.
Применение ситаллов определяется их свойствами. Из ситаллов изготовляют подшипники, детали для двигателей внутреннего сгорания, трубы для химической промышленности, оболочки вакуумных электронных приборов, детали радиоэлектроники. Ситаллы используют в качестве жаростойких покрытий для защиты металлов от действия высоких температур. Их применяют в производстве текстильных машин, абразивов для шлифования, фильер для вытягивания синтетических волокон. Из ситаллов могут быть изготовлены лопасти воздушных компрессоров, сопла реактивных двигателей, они используются для изготовления точных калибров и оснований металлорежущих станков.
Слоистые пластмассы
Они состоят из пропитанных смолой и склеенных между собой листов наполнителя (древесного шпона, бумаги, ткани, стеклоткани и т. п.) и отличаются наибольшей прочностью. Однако из них наиболее трудно прессовать детали сложной конфигурации. Они отличаются максимальной анизотропией свойств. В электро- и радиотехнике, а также в приборостроении из материалов этой группы чаще всего применяют гетинакс (бумолит), текстолит и стеклопласты.
Гетинакс состоит из слоев бумаги, пропитанных смолой и спрессованных под давлением при нагреве в листы и плиты толщиной 0,2—40 мм или трубы. Гетинакс применяют в основном для различных панелей, изоляционных шайб и прокладок, колодок зажимов, каркасов катушек, проходных изоляторов, изоляции обмоток и т. д.
Текстолит состоит из слоев хлопчатобумажной ткани, пропитанных бакелитовой смолой и спрессованных под давлением при нагреве до 150—160° С. По сравнению с гетинаксом текстолит отличается повышенной твердостью и прочностью при ударных нагрузках и более высоким сопротивлением скалыванию вдоль слоев. Он характеризуется лучшей способностью обрабатываться механически без растрескивания и сколов. Текстолит дороже гетинакса. Тем не менее, благодаря высокой вибростойкости и хорошим технологическим качествам текстолит применяют не только как конструкционный, но и как электроизоляционный материал.
Текстолит применяют для изготовления щитков и панелей, изолирующих и тросовых роликов, бесшумных скоростных шестерен, вкладышей подшипников, амортизационных прокладок для поглощения вибраций.
Стеклопласт - пластик с наполнителем из стекловолокна. Применение стеклянных волокон вместо органических позволяет резко улучшить механические и электрические свойства, повысить нагревостойкость, снизить влагопоглощение. Если применяют наполнитель из стеклянной ткани, то пластик называется стеклотекстолитом.
В современных стеклопластах, применяя прочное бесщелочное стекловолокно и новые полимеры, удается реализовать очень высокую удельную прочность, значительно большую, чем у известных металлических материалов.
Поэтому в последние годы развивается тенденция по изготовлению основных силовых конструкций летательных аппаратов и авиационных двигателей из прочных стеклопластов. Из них готовят также обтекатели антенн и т. п. В конструкционных целях применяют аналогичные стеклопластам по структуре другие композиционные материалы: хаифилл — полимер, наполненный графитовым волокном, полимеры, наполненные борным, сапфировым волокном и т. п.
Пенопласт (вспененные полимеры) — важная разновидность современных пластмасс. Пенистой структуры достигают введением в смолу газообразователей (порофоров)— веществ, которые в процессе производства пластмассовых изделий разлагаются с выделением газов.
Пенопласты отличаются малым удельным весом, хорошими звуко-, тепло- и электроизоляционными свойствами: исключительно малой диэлектрической проницаемостью и малыми диэлектрическими потерями. Поэтому пенопласты являются хорошими радиопрозрачными материалами. Они применяются в обтекателях антенн как наполнители для повышения жесткости авиационных конструкций, как тепло-, звукоизоляционные перегородки. Эпоксидные пенопласты начинают широко применять в виде электроизоляционной влагостойкой пенистой заливочной массы — пенокомпаунда. Кремнийорганические пенопласты отличаются максимальной нагревостойкостью (длительно до 200—250°, кратковременно — 300—350°).
Для тепло- и злектроизоляции при более высоких температурах (длительно 500—600°) применяют иногда неорганические пенопласты — вспененная слюда вермикулит, пеностекло и пенокерамика.
Собственные полупроводники
Химически чистые полупроводники называются собственными полупроводниками. К ним относится ряд чистых химических элементов (германий, кремний, селен, теллур и др.) и многие химические соединения, такие, например, как арсенид галлия (GaAs), арсенид индия (InAs), антимонид индия (InSb), карбид кремния (SiC) и т. д.
На рис. а показана упрощенная схема зонной структуры собственного полупроводника. При абсолютном нуле его валентная зона укомплектована полностью, зона проводимости, расположенная над валентной зоной на расстоянии Eg является пустой. Поэтому при абсолютном нуле собственный полупроводник, как и диэлектрик, обладает нулевой проводимостью.
![]() |
Однако с повышением температуры вследствие термического возбуждения электронов валентной зоны часть из них приобретает энергию, достаточную для преодоления запрещенной зоны и перехода в зону проводимости (рис. б). Это приводит к появлению в зоне проводимости свободных электронов, а в валентной зоне - свободных уровней, на которые могут переходить электроны этой зоны. При приложении к такому кристаллу внешнего поля в нем возникает направленное движение электронов зоны проводимости и валентной зоны, приводящее к появлению электрического току. Кристалл становится проводящим.
Чем уже запрещенная зона и выше температура кристалла, тем больше электронов переходит в зону проводимости, поэтому тем более высокую электропроводность приобретает кристалл.
Из изложенного вытекают следующие два важных вывода.
Проводимость полупроводников является проводимостью возбужденной: она появляется под действием внешнего фактора, способного сообщить электронам валентной зоны энергию, достаточную для переброса их в зону проводимости. Такими факторами могут быть нагревание полупроводников, облучение их светом и ионизирующим излучением.

где ? – удельная проводимость;
Список литературы
Авиационное электрорадиоматериаловедение. Коровский Ш. Я., М. «Машиностроение», 1972, стр. 356. Гусев В. Г., Гусев Ю. М. Электроника: Учеб. пособие для приборостроит. спец. вузов.— 2-е изд., перераб. и доп.— М.: Высш. школа. 1991.— 622с.: ил. Зуев В. М. Термическая обработка металлов. Учебник для техн. училищ. — 2-е изд., перераб. и доп.— М.: Высш. школа, 1981. — 296 с., ил. Епифанов Г. И. Физика твердого тела. Учеб. пособие для втузов. Изд. 2-е, перераб. и доп. М., «Высш. школа», 1977. 288 с. с ил. Касаткин А. С. Основы электротехники: Учебное пособие для сред. ПТУ. – 3-е изд., стер. – М.: Высшая шк., 1986. – 287с.: ил. Колобнев И. Ф., Крымов В. В., Мельников А. В. Справочник литейщика. Цветное литье из легких сплавов. Изд. 2-е, перераб. И доп. М., “Машиностроение”, 1974, 416с. Лачин В. И., Савёлов Н. С. Электроника: Учеб. пособие. - Ростов н/Д: изд-во «Феникс», 2000. — 448 с. Лахтин Ю. М., Леонтьева В. П. Материаловедение: Учебник для высших технических учебных заведений. —3-е изд., перераб. и доп. — М.: Машиностроение, 1990. 528 с.: ил. Материаловедение: Учебник для высших технических учебных заведений. Б. Н. Арзамасов, И. И. Сидорин, Г. Ф. Косолапов и др.; Под общ. ред. Б. Н. Арзамасова.—2-е изд., испр. и доп.— М.: Машиностроение, 1986.—384 с., ил. Новиков И. И. Теория термической обработки металлов: Учебник для вузов. 4-е изд., перераб. и доп.: Металлургия, 1980. 460 с. Пасынков В. В., Сорокин В. С. Материалы электронной техники: Учебник для студ. вузов по спец. электронной техники. 3-е изд. — СПб.: Издательство «Лань», 2001. — 368 с., ил. Титце У., Шенк К. Полупроводниковая схемотехника: Справочное руководство. Пер. с нем.-М.: Мир, 1982.-512 с., ил. Цветное литье. Легкие сплавы. Под ред. Колобнева, М., “Машиностроение”, 1966, 391с.
Сплавы на основе алюминия
Свойства алюминия. Алюминий - металл серебристо-белого цвета. Он не имеет полиморфных превращений и кристаллизируется в решетке гранецентрированного куба.
Алюминий обладает малой плотностью, хорошими теплопроводностью и электропроводимостью, высокой пластичностью и коррозионной стойкостью. Примеси ухудшают все эти свойства.
Постоянные примеси алюминия Fe, Si, Cu, Zn, Ti. В зависимости от содержания примесей первичный алюминий подразделяют на три класса: особой чистоты А999 (?0,001% примесей), высокой чистоты А995, А99, А97, А95 (0,005-0,05% примесей) и технической чистоты А85, А8 и др. (0,15-1% примесей). Технический алюминий, выпускаемый в виде деформируемого полуфабриката (листы, профили, прутки и др.), маркируют АД0 и АД1. Механические свойства алюминия зависят от его чистоты и состояния. Увеличение содержания примесей и пластическая деформация повышают прочность и твердость алюминия. Ввиду низкой прочности алюминий применяют для ненагруженных деталей и элементов конструкций, когда от материала требуется легкость, свариваемость, пластичность. Так, из него изготовляют рамы, двери, трубопроводы, фольгу, цистерны для перевозки нефти и нефтепродуктов, посуду и др. Благодаря высокой теплопроводности он используется для различных теплообменников, в промышленных и бытовых холодильниках. Высокая электропроводимость алюминия способствует его широкому применению для конденсаторов, проводов, кабелей, шин и др.
Механические свойства алюминия
Марка | Сумма примесей, % | Состояние | ?в | ?0,2 | ?,% | HB |
MПа | ||||||
А995
А5 АО |
0,005
0.5 1 |
Литой
Литой Литой Деформированный и отожженный Деформированный |
50 75 90 90
140 |
-
- - 30 100 |
45
29 25 30 12 |
150 200
250 250 320 |
Из других свойств алюминия следует отметить его высокую отражательную способность, в связи с чем он используется для прожекторов, рефлекторов, экранов телевизоров.
Алюминий имеет малое эффективное поперечное сечение захвата нейтронов. Он хорошо обрабатывается давлением, сваривается газовой и контактной сваркой, но плохо обрабатывается резанием. Алюминий имеет большую усадку затвердевания. Высокая теплота плавления и теплоемкость способствуют медленному остыванию алюминия из жидкого состояния, что дает возможность улучшать отливки из алюминия и его сплавов путем модифицирования, рафинирования и других технологических операций.
Общая характеристика и классификация алюминиевых сплавов. Алюминиевые сплавы характеризуют высокой удельной прочностью, способностью сопротивляться инерционным и динамическим нагрузкам, хорошей технологичностью. Временное сопротивление алюминиевых сплавов достигает 500 — 700 МПа при плотности не более 2850 кг/м3. По удельной прочности некоторые алюминиевые сплавы приближаются или соответствуют высокопрочным сталям. Большинство алюминиевых сплавов имеют хорошую коррозионную стойкость (за исключением сплавов с медью), высокие теплопроводность и электропроводимость и хорошие технологические свойства (обрабатываются давлением, свариваются точечной сваркой, а специальные - сваркой плавлением, в основном хорошо обрабатываются резанием). Алюминиевые сплавы пластичнее магниевых и многих пластмасс. Большинство из них превосходят магниевые сплавы по коррозионной стойкости, пластмассы - по стабильности свойств.
Основными легирующими элементами алюминиевых сплавов являются Cu, Mg, Si, Mn, Zn; реже-Li, Ni, Ti. Многие легирующие элементы образуют с алюминием твердые растворы ограниченной переменной растворимости и промежуточные фазы. Это дает возможность подвергать сплавы упрочняющей термической обработке. Она состоит из закалки на пересыщенный твердый раствор и естественного или искусственного старения.
Легирующие элементы, особенно переходные, повышают температуру рекристаллизации алюминия.
При кристаллизации они образуют с алюминием пересыщенные твердые растворы. В процессе гомогенизации и горячей обработки давлением происходит распад твердых растворов с образованием тонкодисперсных частиц интерметаллидных фаз, препятствующих прохождению процессов рекристаллизации и упрочняющих сплавы. Это явление получило название структурного упрочнения, а применительно к прессованным полуфабрикатам - пресс-эффекта. По этой причине некоторые алюминиевые сплавы имеют температуру рекристаллизации выше температуры закалки. Для снятия остаточных напряжений в нагартованных полуфабрикатах (деталях), полученных холодной обработкой давлением, а также в фасонных отливках проводят низкий отжиг.
Конструкционная прочность алюминиевых сплавов зависит от примесей Fe и Si. Они образуют в сплавах нерастворимые в твердом растворе фазы. Независимо от формы (пластинчатой, игольчатой и др.) кристаллы этих фаз снижают пластичность, вязкость разрушения, сопротивление развитию трещин. Легирование сплавов марганцем уменьшает вредное влияние примесей, так как он связывает их в четвертую фазу, кристаллизирующуюся в компактной форме. Однако более эффективным способом повышения конструкционной прочности является снижение содержания примесей с 0,5-0,7% до 0,1-0,3% (чистый сплав), а иногда и до сотых долей процента (сплав повышенной чистоты). В первом случае к марке сплава добавляют букву Ч, например, Д16Ч, во втором-ПЧ, например, В95ПЧ. Особенно значительно повышаются характеристики пластичности и вязкости разрушения в направлении, перпендикулярном пластической деформации.
Алюминиевые сплавы классифицируют по технологии изготовления (деформируемые, литейные, спеченные), способности к термической обработке (упрочняемые и неупрочняемые) и свойствам.
Сплавы на основе магния
Свойства магния. Магний-металл серебристо-белого цвета. Он не имеет полиморфных превращений и кристаллизуется в плотноупакованной гексагональной решетке.
Магний и его сплавы отличаются низкой плотностью, хорошей обрабатываемостью резанием и способностью воспринимать ударные и гасить вибрационные нагрузки. Теплопроводность магния в 1,5, а электропроводимость — в 2 раза ниже, чем у алюминия. Примерно в 1,5 раза меньше, чем у алюминия, и его модуль нормальной упругости. Однако они близки по удельной жесткости. В зависимости от содержания примесей установлены следующие марки магния (ГОСТ 804-72): Мг96 (99,96% Mg), Мг95 (99,95% Mg), Мг90 (99,90% Mg). Примеси Fe, Si, Ni, Си понижают и без того низкие пластичность и коррозионную стойкость. При нагреве магний активно окисляется и при температуре выше 623°С на воздухе воспламеняется. Это затрудняет плавку и разливку магния и его сплавов. Порошок, тонкая лента, мелкая стружка магния представляют большую опасность, так как самовозгораются на воздухе при обычных температурах, горят с выделением большого количества теплоты и излучением ослепительно яркого света.
Общая характеристика и классификация магниевых сплавов. Достоинством магниевых сплавов является высокая удельная прочность. Временное сопротивление отдельных сплавов достигает 250-400 МПа. Основными легирующими элементами магниевых сплавов являются Al, Zn, Mn. Для дополнительного легирования используют цирконий, кадмий, церий, ниодим и др. Механические свойства сплавов магния при температуре 20-25°С улучшаются при легировании алюминием, цинком, цирконием. Цирконий и церий оказывают модифицирующее действие на структуру сплавов магния. Особенно эффективно модифицирует цирконий. Добавка 0,5-0,7% Zr уменьшает размер зерна магния в 80-100 раз. Это объясняется структурным и размерным соответствием кристаллических решеток. Кроме того, цирконий и марганец способствуют устранению или значительному уменьшению влияния примесей железа и никеля на свойства сплавов.
Они образуют с этими элементами промежуточные фазы большой плотности, которые при кристаллизации выпадают на дно тигля, очищая тем самым сплавы от вредных примесей.
Увеличение растворимости легирующих элементов в магнии с повышением температуры дает возможность упрочнять магниевые сплавы с помощью закалки и искусственного старения. Однако термическая обработка магниевых сплавов затруднена из-за замедленных диффузионных процессов в магниевом твердом растворе. Малая скорость диффузии требует больших выдержек при нагреве под закалку для растворения вторичных фаз. Благодаря этому такие сплавы можно закаливать на воздухе, они не склонны к естественному старению. При искусственном старении необходимы высокие температуры (до 200° С) и большие выдержки (до 16-24 ч). Наибольшее упрочнение термической обработкой достигается у сплавов магния, легированных неодимом.
Временное сопротивление и особенно предел текучести магниевых сплавов значительно повышаются с помощью термомеханической обработки, которая состоит в пластической деформации закаленного сплава перед его старением.
Из других видов термической обработки к магниевым сплавам применимы различные виды отжига: гомогенизация, рекристаллизационный отжиг и отжиг для снятия остаточных напряжений. Для деформируемых сплавов диффузионный отжиг совмещают с нагревом для горячей обработки давлением. Температура рекристаллизации магниевых сплавов в зависимости от их состава находится в интервале 150-300°С, а рекристаллизационного отжига - соответственно в интервале 250-350 °С. Более высокие температуры вызывают рост зерна и понижение механических свойств. Отжиг для снятия остаточных напряжений проводят при температурах ниже температур рекристаллизации.
Магниевые сплавы хорошо обрабатываются резанием (лучше, чем стали, алюминиевые и медные сплавы), легко шлифуются и полируются. Высокие скорости резания и небольшой расход энергии способствуют снижению стоимости обработки резанием деталей из магниевых сплавов по сравнению с другими сплавами.
Они удовлетворительно свариваются контактной роликовой и дуговой сваркой. Прочность сварных швов деформируемых сплавов составляет 90% от прочности основного металла.
К недостаткам магниевых сплавов, наряду с низкой коррозионной стойкостью и малым модулем упругости, следует отнести плохие литейные свойства, склонность к газонасыщению, окислению и воспламенению при их приготовлении. Небольшие добавки бериллия (0,02-0,05%) уменьшают склонность к окисляемости, кальция (до 0,2%) - к образованию микрорыхлот в отливках. Плавку и разливку магниевых сплавов ведут под специальными флюсами.
По технологии изготовления магниевые сплавы подразделяют на литейные (МЛ) и деформируемые (МА); по механическим свойствам-на сплавы невысокой и средней прочности, высокопрочные и жаропрочные; по склонности к упрочнению с помощью термической обработки-на сплавы, упрочняемые и неупрочняемые термической обработкой. Для повышения пластичности магниевых сплавов их производят с пониженным содержанием вредных примесей Fe, Ni, Си (повышенной чистоты). В этом случае к марке сплава добавляют строчные буквы «пч», например, МЛ5пч или МА2пч.
Способы измерения твёрдости
Под твердостью понимается способность материала противодействовать механическому проникновению в него посторонних тел. Такое определение твердости повторяет, по существу, определение свойств прочности. В материале при вдавливании в него острого предмета возникают местные пластические деформации, сопровождающиеся при дальнейшем увеличении сил местным разрушением. Поэтому показатель твердости связан с показателями прочности и пластичности и зависит от конкретных условий ведения испытания.
Наиболее широкое распространение получили пробы по Бринелю и по Роквеллу. В первом случае в поверхность исследуемой детали вдавливается стальной шарик диаметром 10 мм, во втором — алмазный острый наконечник. По обмеру полученного отпечатка судят о твердости материала. Испытательная лаборатория обычно располагает составленной путем экспериментов переводной таблицей, при помощи которой можно приближенно по показателю твердости определить предел прочности материала. Таким образом, в результате пробы на твердость удается определить прочностные показатели материала, не разрушая детали.
Стабилитроны
Полупроводниковые стабилитроны, называемые иногда опорными диодами, предназначены для стабилизации напряжений. Их работа основана на использовании явления электрического пробоя p-n-перехода при включении диода в обратном направлении.
Материалы, используемые для создания p-n-перехода стабилитронов, имеют высокую концентрацию примесей. При этом напряженность электрического поля в p-n-переходе значительно выше, чем у обычных диодов. При относительно небольших обратных напряжениях в p-n-переходе возникает сильное электрическое поле, вызывающее его электрический пробой. В этом режиме нагрев диода не носит лавинообразного характера. Поэтому электрический пробой не переходит в тепловой.
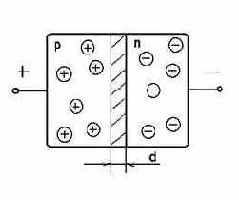
|
|||
|
U

![]() |
В качестве примера на рисунке приведены вольт-амперные характеристики стабилитрона при различных температурах, показано условное обозначение стабилитронов.
Стали, обеспечивающие жесткость, статическую и циклическую прочности
Детали машин и приборов, передающих нагрузку, должны обладать жесткостью и прочностью, достаточными для ограничения упругой и пластической деформации, при гарантированной надежности и долговечности. Из многообразия материалов в наибольшей степени этим требованиям удовлетворяют сплавы на основе железа — чугуна и особенно стали. Стали обладают высоким наследуемым от железа модулем упругости и тем самым высокой жесткостью, уступая в этом лишь бору, вольфраму, молибдену, бериллию, которые из-за высокой стоимости используются только в специальных случаях. Высокая жесткость и доступность обусловливают широкое применение сталей для изготовления строительных металлоконструкций, корпусных деталей, ходовых винтов станков, валов и многих других деталей машин.
Высокую жесткость стали сочетают с достаточной статической и циклической прочностью, значение которой можно регулировать в широком диапазоне изменением концентрации углерода, легирующих элементов и технологии термической и химико-термической обработки.
Применяемые в технике сплавы на основе меди, алюминия, магния, титана, а также пластмассы уступают стали по жесткости, прочности или надежности. Кроме комплекса этих важных для работоспособности деталей свойств, стали могут обладать и рядом других ценных качеств, делающих их универсальным материалом. При соответствующем легировании и технологии термической обработки сталь становится износостойкой, либо коррозионно-стойкой, либо жаростойкой и жаропрочной, а также приобретает особые магнитные, тепловые или упругие свойства. Стали свойственны также хорошие технологические свойства. К тому же она сравнительно недорога. Вследствие этих достоинств сталь - основной металлический материал промышленности.
Старение полимеров
Недостатком многих полимерных материалов, проявляющимся при эксплуатации, является изменение их размеров и свойств, называемое старением. Старение связано с физико-химическими превращениями, происходящими во многих полимерах в процессе работы, особенно при нагреве, механическом истирании, радиационном облучении и т. п.
Процессы превращения в зависимости от природы материала и действующих факторов могут быть весьма различными. Чаще всего это деструкция — реакция, протекающая с разрывом химической связи в главной цепи макромолекулы и образованием продуктов более низкого молекулярного веса. В зависимости от основной причины, вызвавшей ее, различают: термодеструкцию, механодеструкцию, фотохимическую и химическую, в частности окислительную, деструкции. Особенно склонны к процессам окислительной деструкции полиолефины.
Светодиоды
Излучающий диод, работающий в видимом диапазоне волн, часто называют светоизлучающим, или светодиодом.
Излучение возникает при протекании прямого тока диода в результате рекомбинации электронов и дырок в области p-n-перехода и в областях, примыкающих к указанной области. При рекомбинации излучаются фотоны.
Прохождение через p-n-переход тока в прямом направлении сопровождается инжекцией неосновных носителей: электронов в p-область и дырок в n-область. Инжектированные неосновные носители рекомбинируют с основными носителями данной области полупроводника и их концентрация быстро падает по мере удаления от p-n-перехода в глубь полупроводника. У многих полупроводников рекомбинация носит безызлучательный характер: энергия, выделяющаяся при рекомбинации, отдается решетке кристалла, т. е. превращается в конечном итоге в теплоту.
![]() |
Схематическое изображение структуры излучающего диода, его условное графическое обозначение (КПД ~ 10-70%). InAs, Sic, GAs.
Тензорезисторы
Ряд полупроводниковых материалов достаточно резко изменяет свое электросопротивление под влиянием механических напряжений. Этот эффект называется тензорезистивным, а материалы, в которых он имеет место, — тензорезисторами. Природа тензорезистивного эффекта у разных полупроводников может быть различной. У порошковых композиций, например у авиационных угольных регуляторов напряжения и в угольных микрофонах, она обусловливается преимущественно изменением электросопротивления за счет изменения площади и качества поверхности контактов; в однородных монокристаллах — изменением ширины валентной зоны и анизотропии эффективных масс электронов при деформировании; в монокристаллах с p-n-переходами - за счет изменений ширины перехода и потенциалов на нем.
В простейшем случае этот эффект оценивается коэффициентом тензочувствительности по напряжению:

характеризующему относительное изменение электросопротивления ?R/R0, приходящееся на единицу приложенного напряжения ?, или коэффициентом тензочувствительности по деформации:


где ?R – изменение сопротивления; ? – механическое напряжение; ? – коэффициент тензочувствительности по напряжению; ? – механическая деформация; K – коэффициент тензочувствительности по деформации.
Теоретическая и реальная прочности кристаллов на сдвиг

Рассмотрим кристалл
|
Тогда общая сила



Тогда


|
Отсюда - прочность кристалла в зависимости от периода
кристаллической решётки

В неискаженной решетке атомы двух соседних параллельных плоскостей занимают положения равновесия, отвечающие минимуму потенциальной энергии (рис. а). Силы взаимодействия между ними равны нулю. При постепенном смещении одной атомной плоскости относительно другой возникают касательные напряжения, препятствующие сдвигу и стремящиеся восстановить нарушенное равновесие (рис. б). Критическое скалывающее напряжение должно составлять десятую долю от модуля сдвига. В таблице приведено ?к для ряда металлических кристаллов, определенное из опыта и вычисленное теоретически. Сравнение этих величин показывает, что реальная прочность кристаллов на сдвиг на 3—4 порядка меньше теоретически вычисленной прочности этих кристаллов. Это свидетельствует о том, что сдвиг в кристаллах происходит не путем жесткого смещения атомных плоскостей друг относительно друга, а осуществляется таким механизмом, при котором в каждый момент имеет место смещение относительно малого количества атомов. Это привело к развитию дислокационной теории пластического течения кристаллов.


- напряжение сдвига
|
G – модуль сдвига
Металл |
?к, 10-7Па (эксперимен-тальное) |
G, 10-7 Па |
?к, 10-7Па (теоретическое) |
|
G/2? |
G/30 |
|||
Медь Серебро Никель Железо Магний Цинк Кадмий |
0,10 0,06 0,58 2,90 0,08 0,09 0,06 |
4620 2910 7800 6900 1770 3780 2640 |
735 455 1240 1100 280 600 420 |
154 97 260 230 59 126 88 |
Термоэлектрогенераторы и термоэлектрохолодильники
Рассмотрим цепь из p-n-полупроводников. Пусть левые концы образцов n- и p-полупроводника находятся при температуре более высокой, чем правые. В горячей области образуются в большей концентрации электроны и дырки. Путем диффузии они стремятся распространиться по всему объему. В результате горячая часть n-полупроводника зарядится положительно (частично ушли возбужденные электроны), а холодная - отрицательно; в р-полупроводнике горячая часть зарядится отрицательно (частично ушли возникшие дырки), а холодная — положительно.

В цепи, соединенной последовательно из разных материалов, появляется э. д. с., если места контактов поддерживаются при разных температурах. В этом сущность термоэлектрического эффекта Зеебека, используемого в термоэлектрогенераторах (ТЭГ). При появлении тока в цепи, состоящей из различных проводников, в местах контакта в дополнение к теплоте Джоуля выделяется или поглощается в зависимости от направления тока некоторое количество тепла, пропорциональное прошедшему через контакт количеству электричества:
Термоэлектрогенераторы применяют для питания радиоаппаратуры. Так же как и термопарный эффект, эффект Пельтье в p-n-переходах проявляется более энергично, чем в металлических парах. Если в лучших устройствах из металлических пар на контактах удавалось получать перепад температур 3—5° С, то в батареях из полупроводниковых p-n-элементов удается его довести до 60—70° С. Эффект используется для охлаждения радиоаппаратуры и ее термостатирования.
Полупроводниковые термостаты применяют для стабилизации температуры работы пьезокварцев и многих полупроводниковых радио- и вычислительных схем; холодильники - для повышения чувствительности схем с фоторезисторами.
Термореактивные полимеры
Ранее указывалось, что термореактивными являются полимеры с пространственной системой ковалентных связей. Они, как правило, более нагревостойки, тверды и хрупки, чем термопластичные полимеры. Модуль упругости у них выше, а коэффициент линейного расширения ниже, чем у термопластичных полимеров. В обычных растворителях, в которых растворяются термопластичные полимеры, они не растворимы. Термореактивные полимеры широко применяют в качестве основы пластмасс (особенно композиционных), компаундов, лакокрасочных материалов и электроизоляционных лаков, а также клеев.
Фенольноформальдегидные смолы. Бакелитовыми называются конденсационные термореактивные феноло- и крезолоформальдегидные смолы. Их изготовляют из сравнительно дешевого сырья фенола (или крезола) и формальдегида и они являются дешевой основой большого количества пластмасс, лаков и клеев. Так как бакелит хрупок, то выпускаемые на его основе пластмассы наполненные (композиционные).
Резол — наименее конденсированный продукт с линейными молекулами. Он плавится при нагревании, хорошо растворим в спирте, ацетоне, щелочах и феноле.
Резитол — продукт дальнейшей конденсации, в который переходит резол при нагреве до 90—100° С. В спирте и ацетоне он не растворяется, а лишь набухает. При обычной температуре резитол хрупок.
Резит — конечный продукт конденсации, в который переходит резол при нагреве до 150—160°С, не плавок, при 300° С он начинает обугливаться, не растворим в спирте и ацетоне и стоек по отношению к воде, бензину и маслам, серной и соляной кислотам, однако под действием азотной кислоты и щелочей разрушается. Благодаря наличию в структуре молекул групп ОН бакелит полярен и отличается в растворах высокими клеящими свойствами.
Из фенопластов, наполненных слюдяной и древесной мукой и называемых часто карболитами, изготовляют множество мелких деталей.Из более прочных пресспорошков - волокнитов с длинноволокнистыми наполнителями в виде хлопковых очесов, обрезков ткани, асбестового и стекловолокна делают более крупные детали — корпусы приборов, педали и рукоятки управления, коллекторы электрических машин, ролики тросового управления, основания печатных схем и т.
д. Изделия из фенопластов длительно нагревостойки до 120° С.
Существенные недостатки бакелитовых смол — их сравнительно низкое поверхностное сопротивление, особенно во влажной атмосфере, а также низкая стойкость против поверхностных разрядов.
Аминопласты — пресспорошки на основе карбамидофор-мальдегидных смол, наполненные чаще всего целлюлозным волокном, отличаются от фенопластов повышенной дугостойкостью. Бесцветные карбамидные смолы окрашивают в разнообразные, порой весьма яркие цвета. Недостатками аминопластов являются более высокая влагопоглощаемость, более низкая нагревостойкость, худшие технологические свойства, чем у фенопластов. Они также дороже фенопластов.
Полиэфиропласты. Важными представителями группы полиэфирных материалов с удачным сочетанием комплекса электроизоляционных, механических, химических и технологических свойств являются эпоксидные смолы.
Эпоксидные смолы получают в виде жидких, вязких или твердых продуктов в результате реакции конденсации соединений, содержащих концевые эпоксигруппы, послужившие основанием наименования этих смол. Эпоксидные смолы термопластичны и имеют ограниченное применение. Их используют присадкой к ним веществ, вызывающих необратимое отвердение, т. е. переход в термореактивное состояние за счет создания поперечных связок между молекулами.
Способность отвердевать при комнатных или невысоких температурах нагрева без выделения побочных продуктов и с малой усадкой 0,5-1% — ценное технологическое преимущество эпоксидных смол, вследствие которого они становятся незаменимыми как заливочные массы и компаунды.
Эпоксидные смолы отличаются хорошими электроизоляционными свойствами, но дугостойкость их невысока. Основное применение эпоксидных смол — изготовление компаундов, лаков, клеев, пластмасс.
Титан и сплавы на его основе
Свойства титана. Титан-металл серого цвета. Он имеет две полиморфные модификации. Полиморфное превращение (882 °С) при медленном охлаждении происходит по нормальному механизму с образованием полиэдрической структуры, а при быстром охлаждении - по мартенситному механизму с образованием игольчатой структуры.
Промышленный способ производства титана состоит в обогащении и хлорировании титановой руды с последующим ее восстановлением из четыреххлористого титана металлическим магнием. Полученную при этом титановую губку маркируют по твердости специально, выплавленных из нее образцов (ТГ-100, ТГ-110 и т. д.). Для получения монолитного титана губка размалывается в порошок, прессуется и спекается или переплавляется в дуговых печах в вакууме или атмосфере инертных газов.
Для уменьшения количества примесей и более равномерного их распределения по сечению слитка рекомендуется его двух-трехразовая переплавка. Характерную для титановых слитков крупнозернистую структуру измельчают путем модифицирования цирконием или бором. Полученный в результате переплава технический титан маркируют в зависимости от содержания примесей ВТ1-00 (? примесей ? 0,398%), ВТ1-0 (? примесей ?0,55%).
Механические свойства иодидного и технического титана
Титан | Сумма
примесей, % |
?в | ?0,2 | ? | ? | HB |
МПа | % | |||||
ВТ1-0 Иодидный | 0,3
0,093 |
450-600 250-300 | 380-500 100-150 | 20-25 50-60 | 50
70-80 |
2070 1300 |
Отличительными особенностями титана являются хорошие механические свойства, малая плотность, высокая удельная прочность и коррозионная стойкость. Низкий модуль упругости титана, почти в 2 раза меньший, чем у железа и никеля, затрудняет изготовление жестких конструкций. Механические свойства титана характеризуются хорошим сочетанием прочности и пластичности.
Высокая пластичность иодидного титана по сравнению с другими металлами, имеющими гексагональную кристаллическую решетку (Zn, Cd, Mg), объясняется большим количеством систем скольжения и двойникования.
Механические свойства титана сильно за висят от наличия примесей, особенно водорода, кислорода, азота и углерода, которые образуют с титаном твердые растворы внедрения и промежуточные фазы: гидриды, оксиды, нитриды и карбиды. Небольшое количество кислорода, азота и углерода повышает твердость, временное сопротивление и предел текучести, однако при этом значительно уменьшается пластичность, снижается коррозионная стойкость, ухудшаются свариваемость, способность к пайке и штампуемость. Поэтому содержание этих примесей в титане ограничено сотыми, а иногда тысячными долями процента. Аналогичным образом, но в меньшей степени, оказывают влияние на свойства титана железо и кремний. Очень вредная примесь в титане - водород. Присутствуя в весьма незначительном количестве, водород выделяется в виде тонких хрупких пластин гидридной фазы на границах зерен, что значительно охрупчивает титан. Водородная хрупкость наиболее опасна в сварных конструкциях из-за наличия в них внутренних напряжений. Допустимое содержание водорода в техническом титане находится в пределах 0,008-0,012%.
Технический титан хорошо обрабатывается давлением. Из него изготовляют все виды прессованного и катаного полуфабриката: листы, трубы, проволоку, поковки. Титан хорошо сваривается аргонодуговой и точечной сваркой. Сварной шов обладает хорошим сочетанием прочности и пластичности. Прочность шва составляет 90% прочности основного металла.
Титан плохо обрабатывается резанием, налипает на инструмент, в результате чего тот быстро изнашивается. Для обработки титана требуются инструменты из быстрорежущей стали и твердых сплавов, малые скорости резания при большой подаче и глубине резания, интенсивное охлаждение. К недостатку титана относятся также низкие антифрикционные свойства.
Влияние легирующих элементов на структуру и свойства титановых сплавов. Легирующие элементы по характеру влияния на полиморфные превращения титана подразделяют на три группы: ?-стабилизаторы, ?-стабилизаторы и нейтральные элементы.
Практическое значение для легирования титана имеет только алюминий, так как кислород и азот сильно охрупчивают титановые сплавы.
Алюминий - широко распространенный, доступный и дешевый металл. Введение его в титановые сплавы уменьшает их плотность и склонность к водородной хрупкости, повышает модуль упругости, прочность при 20-25°С и высоких температурах.
Добавка к сплавам титана с алюминием таких ?-стабилизаторов, как V, Mo, Mb, Mn, уменьшает склонность к образованию упорядоченной структуры (сверхструктуры). Снижая температуру полиморфного превращения титана, ?-стабилизаторы расширяют область твердых растворов на основе Ti?.
Твёрдость материала по Бринелю рассчитывают исходя из площади отпечатка.
|
[HB] = 1Па
Для стали

Для бронзы, латуни

Углеродистые стали
На долю углеродистых сталей приходится 80% от общего объема. Это объясняется тем, что эти стали дешевы и сочетают удовлетворительные механические свойства с хорошей обрабатываемостью резанием и давлением. При одинаковом содержании углерода по обрабатываемости резанием и давлением они значительно превосходят легированные стали. Однако углеродистые стали менее технологичны при термической обработке. Из-за высокой критической скорости закалки углеродистые стали охлаждают в воде, что вызывает значительные деформации и коробление деталей. Кроме того, для получения одинаковой прочности с легированными сталями их следует подвергать отпуску при более низкой температуре, поэтому они сохраняют более высокие закалочные напряжения, снижающие конструкционную прочность.
Главный недостаток углеродистых сталей - небольшая прокаливаемость (до 12 мм), что существенно ограничивает размер деталей, упрочняемых термической обработкой. Крупные детали изготовляют из сталей без термического упрочнения. По статической прочности углеродистые стали относятся преимущественно к сталям нормальной прочности. Углеродистые конструкционные стали выпускают обыкновенного качества и качественные.
Варикапы
Варикап — это полупроводниковый прибор, предназначенный для использования в качестве управляемой электрическим напряжением емкости. Варикап работает при обратном напряжении, приложенном к p-n-переходу.
Емкость p-n-перехода диода с увеличением обратного напряжения уменьшается. Максимальная емкость варикапа в зависимости от его типа составляет 5-300 пФ. Отношение минимальной и максимальной емкостей равно 1:5. Благодаря достаточно высокой добротности варикапы используются для построения колебательных контуров с управляемой напряжением резонансной частотой в области свч.

![]() |

С =

Влияние энергии химических связей на свойства материалов
Свойства материалов определяются химическим составом и внутренним строением. При одном и том же химическом составе свойства материалов могут существенно отличаться в зависимости от условий их получения и эксплуатации.
Так как любой материал представляет собой продукт взаимодействия огромного количества атомов одного или нескольких химических элементов, то его свойства прежде всего зависят от типа и энергии химической связи составляющих атомов. При любом характере химического сродства частицы тела стремятся расположиться в таком порядке и на таких расстояниях, которые обусловливают относительный минимум энергии всей системы, иными словами, ее наиболее устойчивое в данных условиях состояние. Эти равновесные расстояния между частицами обозначим R0.
При очень больших взаимных расстояниях атомы практически не взаимодействуют друг с другом, так что энергию их можно считать постоянной и равной нулю. При уменьшении расстояния между атомами проявляются силы притяжения и потенциальная энергия понижается. При некотором равновесном расстоянии R=Ro энергия W принимает минимальное значение, а результирующая сила взаимодействия F = dW/dR становится равной нулю. При дальнейшем сближении частиц возникнут силы отталкивания, так как внешние слои атомов, заряженные отрицательно, придут в тесное соприкосновение.

В условиях равновесия частицы располагаются в минимумах потенциальной кривой — в «потенциальных ямах». Величина Wmin характеризует энергию связи частиц, т. е. ту энергию, которую нужно затратить, чтобы разобщить структурные элементы тела. Максимум величины F представляет собой теоретическое усилие, которое может выдержать тело при упругом растяжении. Величина ?W — энергия перехода частиц из одного относительно устойчивого состояния в другое.
Знание кривых взаимодействия позволяет судить о ряде общих свойств тел и особенностях их поведения. Чем ниже расположена точка Wmin, тем выше энергия связи частиц тела, выше его температура плавления, больше модуль упругости, меньше температурный коэффициент линейного расширения и т. д. Хотя точный вид кривой взаимодействия зависит от конкретных свойств взаимодействующих частиц и от направления, в котором она исследуется, однако в общих чертах ее вид определяется типом и энергией химической связи. При воздействии на тело силовых полей частицы тела смещаются из равновесных положений. При этом могут наблюдаться три случая.
1. Ни одна частица не перемещается через вершины потенциальных кривых (не переходит через потенциальные барьеры). Тогда мы имеем дело с упругими безгистерезисными явлениями, при которых состояние системы при данном значении поля одинаково как в процессе его приложения (при возрастании напряженности поля), так и в процессе уменьшения напряженности поля.
2. Некоторые слабо связанные или все частицы силовое поле перебрасывает через потенциальные барьеры из одного относительно устойчивого состояния в другое, но после снятия внешнего воздействия под влиянием внутренних напряжений или теплового движения устанавливается статистически первоначальное состояние. Это бывает тогда, когда осуществляются переходы через потенциальные барьеры, сравниваемые по порядку со средней тепловой энергией частиц. В этом случае происходят упруго-гистерезисные процессы. Такие процессы характеризуют замкнутыми кривыми, называемыми циклами гистерезиса.
3. Если поле перемещает частицы через достаточно высокие потенциальные барьеры, то при снятии внешнего воздействия проявляется остаточный эффект. Он наблюдается при пластической деформации металлов, получении постоянных магнитов, электретов и т. д.
Если во втором или третьем случае, т. е. при переходе через потенциальные барьеры, процесс идет последовательно, то после перехода возникают «пробойные явления» — электрический ток, течение материала и т.п.
Влияние нагрева на структуру и свойства металлов
Процессы, происходящие при нагреве, подразделяют на две основные стадии: возврат и рекристаллизацию; обе стадии сопровождаются выделением теплоты и уменьшением свободной энергии. Возврат происходит при относительно низких температурах (ниже 0,3 Тпл.), рекристаллизация - при более высоких.
Возвратом называют все изменения тонкой структуры и свойств, которые не сопровождаются изменением микроструктуры деформированного металла, т. е. размер и форма зерен при возврате не изменяются.
Рекристаллизацией называют зарождение и рост новых зерен с меньшим количеством дефектов строения; в результате рекристаллизации образуются совершенно новые, чаще всего равноосные кристаллы.
Возврат, в свою очередь, подразделяют на две стадии: отдых и полигонизацию. Отдых при нагреве деформированных металлов происходит всегда, а полигонизация развивается лишь при определенных условиях.
Отдыхом холоднодеформированного металла называют стадию возврата, при которой уменьшается количество точечных дефектов, в основном вакансий; в ряде металлов, таких, как алюминий и железо, отдых включает также переползание дислокаций, которое сопровождается взаимодействием дислокаций разных знаков и приводит к заметному уменьшению их плотности. Перераспределение дислокаций сопровождается также уменьшением остаточных напряжений. Отдых уменьшает удельное электрическое сопротивление и повышает плотность металла.
Полигонизацией называют стадию возврата, при которой в пределах каждого кристалла образуются новые малоугловые границы. Границы возникают путем скольжения и переползания дислокаций; в результате кристалл разделяется на субзерна-полигоны, свободные от дислокаций.
![]() |
Схема полигонизации: а, б — наклепанный металл до и после полигонизации соответственно
Полигонизация в металлах технической чистоты и в сплавах твердых растворах -наблюдается только после небольших степеней деформаций и не у всех металлов.
Так, этот процесс редко развивается в меди и ее сплавах и хорошо выражен в алюминии, железе, молибдене и их сплавах. Полигонизация холоднодеформированного металла обычно приводит к уменьшению твердости и характеристик прочности. Блочная структура, возникшая благодаря полигонизации, весьма устойчива и сохраняется почти до температуры плавления. После формирования блочной структуры рекристаллизация не наступает, полигонизация и рекристаллизация оказываются конкурентами.
Пластически деформированные металлы могут рекристаллизоваться лишь после деформации, степень которой превышает определенное критическое значение, которое называется критической степенью деформации. Если степень деформации меньше критической, то зарождения новых зерен при нагреве не происходит.
Существует также температура рекристаллизации; это наименьшая температура нагрева, обеспечивающая возможность зарождения новых зерен. Температура рекристаллизации составляет некоторую долю от температуры плавления металла: Tрекр. =0,4Tпл. Для алюминия, меди и железа технической чистоты температурный порог рекристаллизации равен соответственно 100. 270 и 450 °С.

Схема изменения микроструктуры наклепанного металла при нагреве: а - наклепанный металл; б - начало первичной рекристаллизации; в - завершение первичной рекристаллизации; г, д - стадии собирательной рекристаллизации
Зарождение новых зерен при рекристаллизации происходит в участках с наибольшей плотностью дислокаций, обычно на границах деформированных зерен. Чем выше степень пластической деформации, тем больше возникает центров рекристаллизации. Они представляют собой субмикроскопические области с минимальным количеством точечных и линейных дефектов строения. Эти области возникают путем перераспределения и частичного уничтожения дислокаций; при этом между центром рекристаллизации и деформированной основой появляется высокоугловая граница.
С течением времени образовавшиеся центры новых зерен увеличиваются в размерах вследствие перехода атомов от деформированного окружения к более совершенной решетке; при этом большеугловые границы новых зерен перемещаются в глубь наклепанного металла.

Схемы изменения твердости (а) и пластичности (6) наклепанного металла при нагреве: I - возврат; II - первичная рекристаллизация; III - рост зерна
Рассмотренная стадия рекристаллизации называется первичной рекристаллизацией или рекристаллизацией обработки. Первичная рекристаллизация заканчивается при полном замещении новыми зернами всего объема деформированного металла.
По завершении первичной рекристаллизации происходит рост образовавшихся зерен при увеличении выдержки или температуры; эта стадия рекристаллизации называется собирательной рекристаллизацией. Этот процесс самопроизвольно развивается при достаточно высоких температурах в связи с тем, что укрупнение зерен приводит к уменьшению свободной энергии металла из-за уменьшения поверхностной энергии.
Рост зерен происходит в результате перехода атомов от одного зерна к соседнему через границу раздела; одни зерна при этом постепенно уменьшаются в размерах и затем исчезают, а другие становятся более крупными, поглощая соседние зерна. С повышением температуры рост зерен ускоряется. Чем выше температура нагрева, тем более крупными окажутся рекристаллизованные зерна. Первичная рекристаллизация полностью снимает наклеп, созданный при пластической деформации; металл приобретает равновесную структуру с минимальным количеством дефектов кристаллического строения. Свойства металла после рекристаллизации близки к свойствам отожженного металла.
Влияние углерода и постоянных примесей на свойства стали
Сталь — сложный по составу железоуглеродистый сплав. Кроме железа и углерода - основных компонентов, а также возможных легирующих элементов, сталь содержит некоторое количество постоянных и случайных примесей, влияющих на ее свойства.
Углерод, концентрация которого в конструкционных сталях достигает 0,8%, оказывает определяющее влияние на их свойства. Степень его влияния зависит от структурного состояния стали, ее термической обработки.
После отжига углеродистые конструкционные стали имеют ферритно-перлитную структуру, состоящую из двух фаз - феррита и цементита. Количество цементита, который отличается высокой твердостью и хрупкостью, увеличивается пропорционально концентрации углерода. В связи с этим, по мере повышения содержания углерода, увеличиваются прочность и твердость, но снижаются пластичность и вязкость стали.
Влияние углерода еще более значительно при неравновесной структуре стали. После закалки на мартенсит временное сопротивление легированных сталей интенсивно растет по мере увеличения содержания углерода и достигает максимума при 0,4%С. При большей концентрации углерода становится нестабильным из-за хрупкого разрушения стали, о чем свидетельствуют низкие значения ударной вязкости. При низком отпуске механические свойства полностью определяются концентрацией углерода в твердом растворе.
Углерод изменяет и технологические свойства стали. При увеличении его содержания снижается способность сталей деформироваться в горячем и особенно в холодном состояниях, затрудняется свариваемость.
Постоянные примеси в стали: марганец, кремний, сера, фосфор, а также газы: кислород, азот, водород.
Марганец - полезная примесь; вводится в сталь для раскисления и остается в ней в количестве 0,3-0,8%. Марганец уменьшает вредное влияние кислорода и серы.
Кремний - полезная примесь; вводится в сталь в качестве активного раскислителя и остается в ней в количестве до 0,4%, оказывая упрочняющее действие.
Сера - вредная примесь, вызывающая красноломкость стали - хрупкость при горячей обработке давлением. В стали она находится в виде сульфидов. Красноломкость связана с наличием сульфидов, которые образуют с железом эвтектику, отличающуюся низкой температурой плавления (988 °С) и располагающуюся по границам зерен. При горячей деформации границы зерен оплавляются, и сталь хрупко разрушается. От красноломкости сталь предохраняет марганец, который связывает серу в сульфиды, исключающие образование легкоплавкой эвтектики. Устраняя красноломкость, сульфиды, так же как и другие неметаллические включения (оксиды, нитриды и т. п.), служат концентраторами напряжений, снижают пластичность и вязкость стали. Содержание серы в стали строго ограничивают. Положительное влияние серы проявляется лишь в улучшении обрабатываемости резанием.
Фосфор - вредная примесь. Он растворяется в феррите, упрочняет его, но вызывает хладноломкость - снижение вязкости по мере понижения температуры. Сильное охрупчивающее действие фосфора выражается в повышении порога хладноломкости. Каждая 0,01 % Р повышает порог хладноломкости на 25 °С. Хрупкость стали, вызываемая фосфором, тем выше, чем больше в ней углерода.
Фосфор - крайне нежелательная примесь в конструкционных сталях. Однако современные методы выплавки и переплавки не обеспечивают его полного удаления. Основной путь его снижения - повышение качества шихты.
Кислород, азот и водород - вредные скрытые примеси. Их влияние наиболее сильно проявляется в снижении пластичности и повышении склонности стали к хрупкому разрушению. Кислород и азот растворяются в феррите в ничтожно малом количестве и загрязняют сталь неметаллическими включениями (оксидами, нитридами). Кислородные включения вызывают красно- и хладноломкость, снижают прочность. Повышенное содержание азота вызывает деформационное старение.
Водород находится в твердом растворе или скапливается в порах и на дислокациях.Хрупкость, обусловленная водородом, проявляется тем резче, чем выше прочность материала и меньше его растворимость в кристаллической решетке.
Случайные примеси - элементы, попадающие в сталь из вторичного сырья или руд отдельных месторождений. Из скрапа в сталь попадает сурьма, олово и ряд других цветных металлов. Сталь, выплавленная из уральских руд, содержит медь, из керченских - мышьяк. Случайные примеси в большинстве случаев оказывают отрицательное влияние на вязкость и пластичность стали.
Заполнение зон электронами. Проводники, диэлектрики и полупроводники
Каждая энергетическая зона содержит ограниченное число энергетических уровней. В соответствии с принципом Паули на каждом уровне может разместиться не более двух электронов. При ограниченном числе электронов, содержащихся в твердом теле, заполненными окажутся лишь несколько наиболее низких энергетических зон. По характеру заполнения зон электронами все тела можно разделить на две большие группы.

К первой группе относятся тела, у которых над целиком заполненными зонами располагается зона, заполненная лишь частично (рис. а). Такая зона возникает в том случае, когда атомный уровень, из которого она образуется, заполнен в атоме не полностью. Частично заполненная зона может образоваться вследствие наложения заполненных зон на пустые или частично заполненные (рис. б). Наличие зоны, заполненной лишь частично, присуще металлам.
Ко второй группе относятся тела, у которых над целиком заполненными зонами располагаются пустые зоны (рис. в, г). Типичным примером таких тел являются химические элементы IV группы таблицы Менделеева — углерод в модификации алмаза, кремний, германий и серое олово, имеющее структуру алмаза. К этой же группе тел относятся многие химические соединения — окислы металлов, нитриды, карбиды, галогениды щелочных металлов и т. д. Согласно зонной теории твердых тел, электроны внешних энергетических зон имеют практически одинаковую свободу движения во всех телах независимо от того, являются они металлами или диэлектриками. Движение осуществляется путем туннельного перехода электронов от атома к атому. Несмотря на это, электрические свойства этих тел, в частности удельная электропроводность, различаются у них на много порядков.
По ширине запрещенной зоны тела второй группы условно делят на диэлектрики и полупроводники. К диэлектрикам относят тела, имеющие относительно широкую запрещенную зону. У типичных диэлектриков Eg > 3 эВ. Так, у алмаза Eg — 5,2 эВ; у нитрида бора Eg - 4,6 эВ.
К полупроводникам относят тела, имеющие сравнительно узкую запрещенную зону (рис. г). У типичных полупроводников Eg < 1 эВ. Так, у германия Eg = 0,65 эВ; у кремния Eg = 1,08 эВ; у арсенида галлия Eg = 1,43 эВ
Диэлектрики:
Запрещенная зона Wg~5эВ; ?=108÷1018Ом*м;
Металлы:
Запрещенная зона Wg=0; ?=10-8÷10-6Ом*м;
Полупроводники:
Запрещенная зона Wg~1эВ; ?=10-6÷107Ом*м;