Алитирование (Al)
Алитированием называется процесс насыщения поверхности стали алюминием. В результате алитирования сталь приобретает высокую окалиностойкость (до850—900° С) и коррозионную стойкость в атмосфере и в ряде сред.
При алитировании в порошкообразных смесях чистые детали вместе со смесью упаковывают в железный ящик. В рабочую смесь входят: порошковый алюминий (25—50%) или ферроалюминий (50—75%), окись алюминия (25—50%) и хлористый алюминий (~1,0%). Процесс осуществляется при температуре 900—1000°С в течение 3—12 ч.
Реже применяют алитирование в ваннах с расплавленным алюминием. Алитируемые детали погружают в расплавленный алюминий (92—94% А1 и 6—8% Fe). Железо добавляют для того, чтобы предотвратить растворение обрабатываемых деталей в алюминии. Процесс проводят при температурах 700—800°С в течение 45— 90 мин.
Алитирование в расплавленном алюминии отличается от алитирования в порошкообразных смесях простотой метода, быстротой и более низкими температурами. Основной недостаток процесса — налипание алюминия на поверхность деталей.
Иногда применяют металлизацию поверхности стали алюминием (напыление слоя алюминия на обрабатываемую поверхность) с последующим диффузионным отжигом при температуре 900—1000°С в течение 1—3 ч.
Для предохранения алюминия от окисления во время диффузионного отжига изделие покрывают обмазкой, состоящей из серебристого графита (48%), кварцевого песка (30%), глины (20%), хлористого алюминия(2%) и 20—25% от массы первых четырех составляющих - жидкого стекла.
Алитирование стали металлизацией с последующим диффузионным отжигом в несколько раз дешевле, чем в порошках. Агитированный слой представляет собой твердый раствор алюминия в железе, концентрация алюминия в поверхностном слое достигает 30-40%. Алитированию подвергают трубы, инструмент для литья цветных сплавов, чехлы термопар, детали газогенераторных машин и т. д.
Аморфное состояние металлов
При сверхвысоких скоростях охлаждения из жидкого состояния диффузионные процессы настолько замедляются, что подавляется образование зародышей и рост кристаллов. В этом случае при затвердевании образуется аморфная структура. Материалы с такой структурой получили название аморфные сплавы или металлические стекла.
Аморфное состояние обеспечивает металлическим материалам свойства, значительно отличающиеся от свойств соответствующих материалов с кристаллической структурой. Так, аморфные магнитомягкие материалы характеризуются прямоугольной петлей гистерезиса, высокой магнитной проницаемостью и очень малой коэрцитивной силой. При этом магнитные свойства материала малочувствительны к механическим воздействиям на него.

На рисунке показана связь характерных графиков изменения свободной энергии возможных фаз при трех определенных температурах t1, t2, t3 с диаграммой состояния. При температуре t2 между точками а и b в термодинамическом равновесии сосуществуют две фазы: жидкий раствор состава ха и твердый раствор состава xb. Значения свободных энергий этих растворов соответствуют точкам a' и b'. Для более точного построения линий ликвидус и солидус необходимо иметь несколько графиков для интервала температур между t1и t3.
Термодинамическое обоснование диаграммы состояния сплавов, компоненты которых полностью растворимы в жидком и твердом состояниях
Азотирование
Азотированием называется процесс насыщения поверхности стали азотом. Процесс осуществляется в среде аммиака при температуре 480—650° С. При этих температурах выделяется атомарный азот, который диффундирует в поверхностные слои детали.
Для азотирования применяют среднеуглеродистые легированные стали. При азотировании легированных сталей азот образует с легирующими элементами устойчивые нитриды, которые придают азотированному слою высокую твердость.
Перед азотированием детали подвергают термической обработке, состоящей из закалки и высокотемпературного отпуска. Затем производят механическую обработку, придающую окончательные размеры изделию.
Участки, не подлежащие азотированию, защищают тонким слоем (0,001—0,015 мм) олова, нанесенным электролитическим методом, или жидким стеклом. В процессе азотирования олово расплавляется и благодаря поверхностному натяжению удерживается на поверхности стали в виде тонкой непроницаемой для азота пленки. Продолжительность процесса зависит от толщины слоя. Обычно процесс азотирования ведут при температурах 500—520° С. В этом случае получают слои толщиной до 0,5 мм за 24—90 ч.
Для ускорения процесса азотирования применяют двухступенчатый цикл. Вначале азотирование ведут при 500—520°С, а затем температуру повышают до 580—600° С. Это ускоряет процесс в 1,5—2 раза при сохранении высокой твердости азотированного слоя.
В процессе азотирования изменяются размеры деталей за счет увеличения объема поверхностного слоя. Чем выше температура процесса и больше толщина азотированного слоя, тем больше изменение размеров деталей.
Для повышения коррозионной устойчивости изделий азотирование проводят при температуре 600—700°С в течение 15 мин. для мелких деталей и 6—10 ч. для крупных деталей.
Процесс жидкостного азотирования осуществляют при температуре 570°С в расплаве циансодержащих солей. В ходе процесса расплав непрерывно продувается сухим и чистым воздухом, что обеспечивает превращения цианида в цианат, являющийся поставщиком атомов углерода и азота.
Преимуществом жидкостного азотирования является резкое сокращение времени получения насыщенного слоя по сравнению с газовым азотированием (слой толщиной 0,10-0,20 мм получают за 1,5-3 ч). Кроме того, отсутствие водорода в среде способствует
повышению вязкости слоя. Недостатком процесса является применение ядовитых солей.
Широкое применение получает ионное азотирование. По сравнению с газовым азотированием оно имеет ряд преимуществ: меньшую продолжительность процесса, более высокое качество азотированного слоя, пониженную хрупкость слоя.
Борирование (B)
Борированием называется насыщение стали бором. Борирование проводят с целью повышения стойкости против абразивного износа. Толщина борированных слоев не превышает 0,3 мм.
Широкое распространение получил метод электролизного борирования в расплавленных солях, содержащих бор. Деталь служит катодом в ванне с расплавленной бурой. Температура процесса 900—950° С. Процесс можно вести и без электролиза в ваннах с расплавленными хлористыми солями, в которые добавляют порошкообразный ферробор или карбид бора.
Применяют также и метод газового борирования. В этом случае насыщение бором проводят в среде диборана в смеси с водородом при температуре 850—900° С.
Борированию подвергают втулки грязевых нефтяных насосов, штамповый инструмент и т. д.
Бороволокниты
Бороволокниты представляют собой композиции из полимерного связующего и упрочнителя — борных волокон,
Бороволокниты отличаются высокой прочностью при сжатии, сдвиге и срезе, низкой ползучестью, высокими твердостью и модулем упругости, теплопроводностью и электропроводимостью. Ячеистая микроструктура борных волокон обеспечивает высокую прочность при сдвиге на границе раздела с матрицей.
Помимо непрерывного борного волокна применяют комплексные боростеклониты, в которых несколько параллельных борных волокон оплетаются стеклонитью, придающей формоустойчивость. Применение боростеклонитей облегчает технологический процесс изготовления материала.
В качестве матриц для получения бороволокнитов используют модифицированные эпоксидные и полиамидные связующие. Бороволокниты КМБ-1 и КМБ-1к предназначены для длительной работы при температуре 200°С; КМБ-3 и КМБ-Зк не требуют высокого давления при переработке и могут работать при температуре не свыше 100 °С; КМБ-2к работоспособен при 300 °С.
Бороволокниты обладают высокими сопротивлениями усталости, они стойки к воздействию радиации, воды, органических растворителей и горючесмазочных материалов.
Изделия из бороволокнитов применяют в авиационной и космической технике (профили, панели, роторы и лопатки компрессоров, лопасти винтов и трансмиссионные валы вертолетов и т. д.).
Цементация
Цементацией называется процесс насыщения поверхностного слоя стальных изделий углеродом. Цементация осуществляется с целью получения высокой твердости на поверхности изделия при сохранении вязкой сердцевины, она способствует повышению износостойкости и предела выносливости.
Цементации подвергают детали из низкоуглеродистых сталей (содержание углерода до 0,25%), работающие в условиях контактного износа и знакопеременных нагрузок (втулки, поршневые пальцы, кулачки, колонки и т. д.).
Для цементации детали поступают после механической обработки с припуском на шлифование 0,05— 0,10 мм. Участки, не подлежащие цементации, защищают тонким слоем меди (0,02—0,04 мм), наносимым электролитическим способом, или специальными обмазками, состоящими из смеси огнеупорной глины, песка и асбеста, замешанных на жидком стекле, и др.
Цементация осуществляется при температурах 900—950°С. Чем меньше углерода в стали, тем выше температура нагрева для цементация. При этих температурах атомарный углерод адсорбируется на поверхности стали и диффундирует в глубь металла. В результате цементации содержание углерода в поверхностном слое составляет 0,8—1,0%. Более высокая концентрация углерода способствует охрупчиванию цементованного слоя.
Цементованный слой имеет переменную концентрацию углерода по толщине, которая уменьшается от поверхности к сердцевине. В связи с этим после медленного охлаждения в структуре цементованного слоя можно различить три зоны: заэвтектоидную, состоящую из перлита и цементита вторичного; эвтектоидную, состоящую из перлита; доэвтектоидную, состоящую из перлита и феррита.
За толщину цементованного слоя обычно принимают сумму заэвтектоидной, эвтектоидной и половины доэвтектоидной зон. Обычно толщина слоя для большинства стаей составляет 0,8—1,4 мм.
Различают два вида цементации: твердую и газовую. Среда, в которой проводят цементацию, называется карбюризатором.
Цементация в твердой среде
Карбюриза тором является активированный древесный уголь (дубовый или березовый), а также каменноугольный полукокс и торфяной кокс. Для ускорения процесса к древесному углю добавляют активизаторы — углекислый барий, кальцинированную соду, поташ.
Подготовленные для цементации изделия укладывают в металлический ящик. Предварительно в ящик насыпают слой карбюризатора 20—30 см. Детали укладывают слоями на расстоянии 10—15 мм друг от друга. Каждый слой деталей засыпают карбюризатором и на него укладывают следующий слой деталей и т. д. Последний слой засыпают карбюризатором и ящик накрывают крышкой, края которой обмазывают огнеупорной глиной или смесью глины с песком. Иногда вместо крышки кладут лист асбеста и сверху обмазывают глиной. После этого ящик помещают в печь с температурой 900—950°С.
В ящике между кусочками угля имеется воздух, кислород которого взаимодействует с углеродом карбюризатора, образуя окись углерода СО. Соприкасаясь с поверхностью деталей, окись углерода диссоциирует.


Выделившийся атомарный углерод диффундирует в глубь металла. Добавление углекислых солей активизирует процесс цементации.
Продолжительность выдержки в печи при температуре цементации зависит от требуемой толщины цементованного слоя. На практике выдержка принимается из расчета роста слоя со скоростью 0,1 мм в час. Например, слой толщиной 1 мм получают за 9,5-10,4 ч.
Для контроля над протеканием процесса и толщины цементованного слоя в ящик вместе с деталями закладывают «свидетели» - образцы диаметром 10—15 мм, изготовленные из той же марки стали, что и деталь. Во время цементации «свидетели» периодически вынимают, ломают и по излому определяют толщину цементованного слоя.
Повышение температуры цементации до 950—1000° С позволяет значительно ускорить процесс, но такой режим применим для наследственно мелкозернистых сталей.
Ящики после цементации охлаждают на воздухе и потом разбирают.
Участки изделия, не подлежащие цементации, защищают, нанося гальваническое покрытие медью. После цементации детали подвергают нормализации для измельчения зерна, повторной закалке и низкотемпературному отпуску.
Структура сердцевины зависит от состава стали и режима закалки. У углеродистых сталей она состоит из феррита и сорбита или троостита, а у легированных — из малоуглеродистого мартенсита.
Газовая цементация
В настоящее время газовая цементация является основным процессом цементации на заводах массового производства. При газовой цементации сокращается длительность процесса, так как отпадает необходимость прогрева ящиков, можно обеспечить более полную механизацию и автоматизацию процесса, упрощается последующая термическая обработка и, самое главное, можно получить заданную концентрацию углерода в слое.
Цементацию выполняют в шахтных, муфельных или безмуфельных печах непрерывного действия. При цементации в шахтных печах для получения науглероживающей атмосферы применяют метан, керосин, синтин, бензол и т. д. В печах непрерывного действия чаще используют метан. Для получения заданной концентрации углерода (обычно 0,8%) применяют атмосферы с регулируемым потенциалом углерода.
Под углеродным потенциалом атмосферы понимают определенную концентрацию углерода на поверхности цементованного слоя. Для ускорения процесса углеродный потенциал атмосферы в печи меняют по зонам. Вначале его поддерживают высоким, обеспечивающим получение в поверхностном слое концентрации углерода 1,3— 1,4%, а затем его снижают для получения в этом слое оптимального содержания углерода (0,8%).
С этой целью в первую зону, занимающую примерно 2/3 длины печи, подают газ, состоящий из смеси природного (10—15%) и эндотермического (90—85%) газов. Во вторую зону подают только эндотермический газ, находящийся в равновесии с заданной концентрацией углерода (0,8%) на поверхности. При этом за счет диффузии углерода в глубь металла и взаимодействия поверхности детали с эндотермической атмосферой концентрация углерода на поверхности уменьшается и происходит более равномерное его распределение по толщине цементованного слоя.
После газовой цементации применяют закалку (для наследственно мелкозернистых сталей) непосредственно из цементационной печи, предварительно сделав подстуживание до температуры 850—830°С. Заключительной операцией является низкотемпературный отпуск при температуре 160—180° С.
Центробежное литье
Сущность процесса литья центробежным способом заключается в том, что заполнение формы жидким сплавом и кристаллизация его происходит под воздействием центробежных сил. Центробежным способом получают отливки, имеющие не только форму тел вращения, но и другие фасонные отливки.
Детали, имеющие форму тел вращения, например втулки, вкладыши подшипников, венцы, червячные колеса, барабаны и др., отливают на центробежных машинах с вертикальной или с горизонтальной осью вращения.
Литье центробежным способом цветных сплавов широко распространено. Объясняется это тем, что, наряду с повышением качества литья, значительно снижается расход ценных цветных металлов, уменьшается брак и снижается стоимость отливок.
Одним из преимуществ литья тяжелых цветных сплавов центробежным способом является то, что под действием центробежной силы неметаллические включения, как более легкие, вытесняются на внутреннюю (свободную) поверхность, откуда легко удаляются механической обработкой. Скорость вращения формы связана с температурным интервалом кристаллизации заливаемого сплава. Чем больше интервал кристаллизации, тем больше должна быть скорость вращения формы.
Цианирование и нитроцементация
Цианированием называется процесс одновременного насыщения поверхности деталей углеродом и азотом.
На состав и свойства цианированного слоя особое влияние оказывает температура процесса. Повышение температуры цианирования ведет к увеличению содержания углерода в слое, снижение температуры — к увеличению содержания азота. Толщина цианированного слоя также зависит от температуры и продолжительности процесса.
Различают жидкое и газовое цианирование. Газовое цианирование еще называют нитроцементацией. Жидкое цианирование проводят в расплавленных солях, содержащих цианистый натрий.
Цианирование при температурах 820—850°С позволяет осуществлять закалку непосредственно из ванны. После закалки следует низкотемпературный отпуск.
Цианирование при температурах 820—850°С позволяет получать слои толщиной 0,15-0,35 мм за 30-90 мин. Для получения слоев большой толщины (0,5-2,0 мм) применяют глубокое цианирование при температурах 900-950° С, длительность 1,5-6,0 ч. Глубокое цианирование имеет ряд преимуществ по сравнению с цементацией: меньше продолжительность процесса для получения слоя заданной толщины; меньше деформация и коробление; более высокое сопротивление износу и повышенная усталостная прочность.
После цианирования деталь охлаждают на воздухе, повторно нагревают для закалки и проводят низкотемпературный отпуск. Такая обработка необходима в связи с тем, что при температурах цианирования (900—950° С) сильно вырастает зерно аустенита и необходим повторный нагрев для его измельчения. Структура цианированного слоя после закалки такая же, как после цементации.
Недостатком цианирования является ядовитость цианистых солей. Поэтому цианирование проводят в специально выделенных помещениях с соблюдением мер предосторожности.
Нитроцементацию осуществляют при температурах 840—860°С в газовой смеси из науглероживающего газа и аммиака. Продолжительность процесса зависит от глубины насыщаемого слоя и составляет 1 —10 ч. Толщина слоя колеблется от 0,1 до 1,0 мм.
После нитроцементации изделия подвергают закалке и низкотемпературному отпуску при температуре 160— 180° С.
Низкотемпературное цианирование осуществляется при температурах 540—560°С в расплавленных цианистых слоях. Низкотемпературному цианированию подвергают инструмент из быстрорежущих сталей для повышения его стойкости при резании. В результате такой обработки образуется нитроцементованный слой толщиной 0,02—0,04 мм. Длительность процесса 1 —1,5 ч.
Диаграмма растяжения
![]() |
При действии на тело внешней растягивающей силы оно растягивается, и этот процесс отражается на диаграмме растяжения.
Различают относительное и абсолютное удлинение:
|
1. Относительное
|
2. Абсолютное
|
При этом материал испытывает механическое напряжение
Связь абсолютного удлинения и механического
|
|||
|
|||
удлинения отражается в законе Гука или
где k – коэффициент податливости,

Зона ОА носит название зоны упругости (

Зона АВ называется зоной общей текучести, а участок АВ диаграммы — площадкой текучести. Здесь происходит существенное изменение длины образца без заметного увеличения нагрузки. Наличие площадки текучести для металлов не является характерным. В большинстве случаев при испытании на растяжение и сжатие площадка АВ не обнаруживается.
![]() |
Зона ВС называется зоной упрочнения. Здесь удлинение образца сопровождается возрастанием нагрузки, но неизмеримо более медленным (в сотни раз), чем на упругом участке. В стадии упрочнения на образце намечается место будущего разрыва и начинает образовываться так называемая шейка — местное сужение образца.
По мере растяжения образца утонение шейки прогрессирует.
Когда относительное уменьшение площади сечения сравняется с относительным возрастанием напряжения, сила достигнет максимума. В дальнейшем удлинение образца происходит с уменьшением силы, хотя среднее напряжение в поперечном сечении шейки и возрастает. Удлинение образца носит в этом случае местный характер, и поэтому участок кривой CD называется зоной местной текучести. Точка D соответствует разрушению образца. У многих материалов разрушение происходит без заметного образования шейки.
Если испытуемый образец, не доводя до разрушения, разгрузить, то в процессе разгрузки зависимость между силой и удлинением изобразится прямой KL. Опыт показывает, что эта прямая параллельна прямой ОА. При разгрузке удлинение полностью не исчезает. Оно уменьшается на величину упругой части удлинения (отрезок LM). Отрезок OL представляет собой остаточное удлинение. Его называют также пластическим удлинением, а соответствующую ему деформацию — пластической деформацией. При повторном нагружении образца диаграмма растяжения принимает вид прямой LK и далее — кривой KCD, как будто промежуточной разгрузки и не было.

![]() |
Чтобы дать количественную оценку описанным выше свойствам материала, перестроим диаграмму растяжения в координатах ? и ?. Эта диаграмма имеет тот же вид, что и диаграмма растяжения, но будет характеризовать уже не свойства образца, а свойства материала. Отметим на диаграмме характерные точки и дадим определение соответствующих им числовых величин. Наибольшее напряжение, до которого материал следует закону Гука, называется пределом пропорциональности ?п. Величина предела пропорциональности зависит от той степени точности, с которой начальный участок диаграммы можно рассматривать как прямую.
Упругие свойства материала сохраняются до напряжения, называемого пределом упругости. Под пределом упругости ?у понимается такое наибольшее напряжение, до которого материал не получает остаточных деформаций.Для того чтобы найти предел упругости, необходимо после каждой дополнительной нагрузки образец разгружать и следить, не образовалась ли остаточная деформация. Так как пластические деформации в отдельных кристаллах появляются уже в самой ранней стадии нагружения, ясно, что величина предела упругости, как и предела пропорциональности, зависит от требований точности, которые накладываются на производимые замеры.
Следующей характеристикой является предел текучести. Под пределом текучести понимается то напряжение, при котором происходит рост деформации без заметного увеличения нагрузки. Предел текучести легко поддается определению и является одной из основных механических характеристик материала.
Отношение максимальной силы, которую способен выдержать образец, к его начальной площади поперечного сечения носит название предела прочности, или временного сопротивления, и обозначается через ?вр.
Диаграмма состояния железоуглеродистых сплавов
Среди диаграмм состояния металлических сплавов самое большое значение имеет диаграмма состояния системы железо-углерод. Это объясняется тем, что в технике наиболее широко применяют железоуглеродистые сплавы.
Имеются две диаграммы состояния железоуглеродистых сплавов: метастабильная, характеризующая превращения в системе железо-карбид железа (цементит), и стабильная, характеризующая превращение в системе железо - графит.
На то, что система железо - графит является более стабильной, чем система железо-цементит, указывает тот факт, что при нагреве до высоких температур цементит распадается на железо и графит, т. е. переходит в более стабильное состояние.
Компоненты и фазы в сплавах железа с углеродом
Железо и углерод — элементы полиморфные. Железо с температурой плавления 1539°С имеет две модификации - ? и ?. Модификация Fe?, существует при температурах до 911°С и от 1392 до 1539°С, имеет ОЦК решетку с периодом 0,286 нм. Важной особенностью Fe? является его ферромагнетизм ниже температуры 768 С, называемой точкой Кюри.
Модификация Fe? существует в интервале температур от 911 до 1392°С и имеет ГЦК решетку, период которой при 911°С равен 0,364 им. ГЦК решетка более компактна, чем ОЦК решетка. В связи с этим при переходе Fe? в Fe? объем железа уменьшается приблизительно на 1%.
Углерод существует в двух модификациях: графита и алмаза. При нормальных условиях стабилен графит, алмаз представляет собой его метастабильную модификацию. При высоких давлениях и температурах стабильным становится алмаз.
Фазы в сплавах железа с углеродом представляют собой жидкий раствор, феррит, аустенит, цементит и свободный углерод в виде графита.
Феррит (обозначают Ф) - твердый раствор внедрения углерода в Fe?. Различают низкотемпературный и высокотемпературный феррит. Предельная концентрация углерода в низкотемпературном феррите мала и составляет 0,02%, в высокотемпературном-0,1%. Столь низкая растворимость углерода в Fe? обусловлена малым размером межатомных пор
в ОЦК решетке. Значительная доля атомов углерода вынуждена размещаться
в дефектах.
Аустенит (обозначают А) - твердый раствор внедрения углерода в Fe?. Он имеет ГЦК решетку, межатомные поры в которой больше, чем в ОЦК решетке, поэтому растворимость углерода в Fe? значительно больше и достигает 2,14%. Аустенит пластичен, но прочнее феррита (НВ 1600-2000) при температуре 20-25 °С.
Цементит (обозначают Ц) - карбид железа Fe3C. Содержит 6,69 %С и имеет сложную ромбическую решетку. При нормальных условиях цементит тверд (НВ 8000) и хрупок. Он слабо ферромагнитен и теряет ферромагнетизм при температуре 210°С. Температуру плавления цементита трудно определить в связи с его распадом при нагреве. Она установлена равной 1260°С при нагреве лазерным лучом.
Графит - углерод, выделяющийся в железоуглеродистых сплавах в свободном состоянии. Имеет гексагональную кристаллическую решетку. Графит электропроводен, химически стоек, малопрочен, мягок.
Диффузионная металлизация
Диффузионная металлизация - это процесс диффузионного насыщения поверхностных слоев стали различными металлами. Она может осуществляться в твердых, жидких и газообразных средах.
При диффузионной металлизации в твердых средах применяют порошкообразные смеси, состоящие обычно из ферросплавов с добавлением хлористого аммония.
Жидкая диффузионная металлизация осуществляется погружением детали в расплавленный металл (например, цинк, алюминий).
При газовом способе насыщения применяют летучие хлористые соединения металлов, образующиеся при взаимодействии хлора с металлами при высоких температурах. Хлориды диссоциируют на поверхности железа и выделяющийся в атомарном состоянии металл диффундирует в железо.
Диффузия металлов в железе идет значительно медленнее, чем углерода и азота, потому что углерод и азот образуют с железом твердые растворы внедрения, а металлы - твердые растворы замещения. Это приводит к тому, что диффузионные слои при металлизации получаются в десятки раз более тонкими. Поверхностное насыщение стали металлами проводится при температурах 900—1200° С.
Диффузионный отжиг (гомогенизация)
В реальных условиях охлаждения расплава кристаллизация твердых растворов чаще всего протекает неравновесно: диффузионные процессы, необходимые для выравнивания концентрации растущих кристаллов по объему, отстают от процесса кристаллизации. В результате сохраняется неоднородность состава по объему кристалла - внутрикристаллическая ликвация: сердцевина кристаллов обогащена тугоплавким компонентом сплава, а наружные части кристаллов обогащены компонентом, понижающим температуру плавления.
Диффузионным отжигом называют длительную выдержку сплавов при высоких температурах, в результате которой уменьшается ликвационная неоднородность твердого раствора. При высокой температуре протекают диффузионные процессы, не успевшие завершиться при первичной кристаллизации.
Диоды
В пластине полупроводника, на границе между двумя слоями с различного рода электропроводностями, образуется электронно-дырочный переход, называемый также p-n-переходом или запирающим слоем. Этот слой обладает вентильными свойствами, т. е. односторонней проводимостью. Это явление можно пояснить следующими положениями. Концентрация электронов в n-области во много раз больше, чем их концентрация в p-области, где они служат неосновными носителями заряда. Вследствие этого электроны диффундируют в область их низкой концентрации — p-область. Здесь они рекомбинируют с дырками акцепторов и таким путем образуют пространственный (объемный) отрицательный заряд ионизированных атомов акцепторов, не скомпенсированный положительным зарядом дырок — основных носителей заряда в этой области.
Одновременно происходит диффузия дырок в n-область. Здесь создается нескомпенсированный зарядом электронов пространственный положительный заряд ионов доноров. Таким путем между двумя областями полупроводника возникает двойной слой пространственного заряда, обедненный основными носителями заряда. Из-за наличия пространственных зарядов возникает перепад электрического потенциала между p- и n-областями. Его называют потенциальным барьером, а его величину — высотой потенциального барьера.
Электронно-дырочный переход нельзя получить, наложив одну на другую пластины, изготовленные из полупроводников с различной примесной проводимостью, так как между пластинами неизбежно наличие поверхностных пленок или очень тонкого слоя воздуха. Такой переход создается лишь посредством образования областей с различными электропроводностями в одной пластине полупроводника. Такой двухслойный полупроводниковый прибор с p-n-переходом называется полупроводниковым диодом.
Если положительный полюс источника электроэнергии соединен с p-областью полупроводникового диода, а отрицательный — с n-областью, то электрическое поле источника ослабляет до малой величины действие пространственных зарядов — снижает потенциальный барьер диода, вследствие чего резко возрастает диффузия и вместе с ней ток через p-n-переход. Такое включение полупроводникового диода называется прямым.
При обратном включении полупроводникового диода, когда с p-областью соединен минус источника напряжения, а с n-областью — плюс этого источника, внешнее поле усиливает поле пространственных зарядов и удаляет носители заряда с обеих сторон перехода. Через p-n-переход создается в этом случае лишь весьма малый ток, обусловленный движением неосновных носителей заряда. Но из-за этого тока обратное сопротивление полупроводникового диода является конечной величиной.
Для стали и чугуна F = 3000 кгс
Для сплава меди, никеля, алюминия F = 1000 кгс
Для мягких сплавов F = 250 кгс
Дополнительные компоненты полимерных композиций
Полимерные материалы: пластические массы, пленки и волокна, лаки, компаунды, клеи, герметики, резины и т. д. редко состоят из одного полимера. Для улучшения их функциональных качеств они представляют собою обычно композиции из различных полимерных и неполимерных материалов, модифицирующих их свойства.
Чаще всего такими дополнительными компонентами, содержащимися во многих полимерных материалах, являются: стабилизаторы, наполнители, пластификаторы, мягчители и смазки, красители, растворители, другие модификаторы (отверждающие агенты, присадки, сообщающие негорючесть, повышенную нагревостойкость и т. п.).
Стабилизаторами называются вещества, добавляемые в большинство полимерных материалов (в количестве порядка десятых долей процента) для предотвращения реакций старения.
Наполнители — это частицы различных материалов, добавляемые во многие полимерные композиции для сообщения им специальных свойств (повышения прочности, сообщения магнитных свойств, электропроводности, снижения звуко- и теплопроводности и т. д.) или для их удешевления. Наполнители могут быть газообразными, жидкими и твердыми. Чаще всего их применяют в виде газообразных или твердых включений в полимерную основу.
Порошковые наполнители - древесная мука, окислы (ZnO, Ti02, SiO2), мел, каолин и другие. Они мало препятствуют растеканию пресспорошка в пресс-формах и позволяют получить дешевые изделия сложной конфигурации.
Волокнистые наполнители - хлопчатобумажное, стеклянное, борное волокно, обрезки бумаги и ткани позволяют получать материалы в два и более раза прочнее, чем при порошковых наполнителях.
Особенно высока прочность пластмасс (композиционных материалов) при применении в качестве наполнителей слоистых материалов ткани, шпона или стеклянных, длинных тонких волокон; волокон бора, графитовых нитей и т. п., уложенных оптимальным образом по отношению к действующим нагрузкам. Такие композиционные материалы обладают максимальной удельной прочностью, что значительно выше, чем у многих металлических материалов.
Из них готовят напряженные элементы самолетов и двигателей (корпусы, роторы и лопатки компрессоров, обшивку самолетов и т. д.).
Наполнение резин сажей или металлическими частицами придает им проводящие, а магнитными (например, ферритами) — магнитные свойства.
Наполнение газами достигается вспениванием в процессе получения полимеров, введением твердых частиц — порофоров, выделяющих газы при нагреве в размягченный полимер. Иногда вспенивания достигают введением в полимер легкокипящих жидкостей.
Пластификаторы - вещества, добавляемые в полимерные материалы для повышения эластичности и морозостойкости (снижения хрупкости), а также для снижения температуры переработки материалов в изделия. В некоторых случаях, например для эфиров целлюлозы, такая переработка горячим прессованием вообще была бы невозможна, ибо температура разложения непластифицированных продуктов лежит ниже их температуры размягчения.
Смазки, часто вводимые в состав различных полимерных композиций, способствуют отлипу деталей металлического оборудования, применяемого при переработке полимерной композиции в изделия. В качестве смазок используют стеарин, стеараты, парафин и другие легкоплавкие вещества.
Красители вводят в полимерные материалы для придания им красивого декоративного вида или в маркировочных целях. Растворимые в полимере красители нередко называются краской, нерастворимые - пигментами.
Другие присадки. В полимерных материалах могут содержаться и другие, кроме перечисленных, присадки, придающие материалам специальные качества.
Так, для уменьшения горючести композиций на основе горючих полимеров в них вводят 10—20% антипиренов — фосфорнокислый аммоний, трехокись сурьмы, хлорированный парафин или перхлорвинил и т. п.
Для придания полимерным материалам антисептических свойств и стойкости против действия грибковой плесени и разрушающего действия насекомых к ним добавляют антисептики, фунгициды и инсектоциды. В качестве таких веществ нередко служат соли ртути и меди, а также другие ядовитые вещества.Эти присадки особенно часто добавляют в краски, изоляцию проводов и другие полимерные материалы, предназначенные для работы в тропическом климате.
Фотодиоды
Фотодиод, как и фотоэлемент с запирающим слоем, представляет собой p-n-переход, включенный в цепь в запорном направлении, последовательно с внешним источником питания. При отсутствии светового потока через фотодиод протекает незначительный так называемый темповой ток. При освещении p-n-перехода вследствие генерации избыточных носителей обратный ток увеличивается пропорционально потокe, вызывая увеличение падения напряжения на нагрузочном сопротивлении. От фотоэлементов с внешним фотоэффектом фотодиоды выгодно отличаются малыми габаритами и весом, высокой интегральной чувствительностью и небольшим рабочим напряжением.
Физические процессы, протекающие в фотодиодах, носят обратный характер по отношению к процессам, протекающим в светодиодах. Основным физическим явлением в фотодиоде является генерация пар электрон-дырка в области р-n-перехода и в прилегающих к нему областях под действием излучения.
Электрическое поле р-n-перехода разделяет электроны и дырки. Неосновные носители электричества, для которых поле является ускоряющим, выводятся этим полем за переход. Основные носители задерживаются полем в своей области проводимости.

Упрощенная структура фотодиода и его условное графическое обозначение
Генерация пар электрон-дырка приводит к увеличению обратного тока диода при наличии обратного напряжения и к появлению напряжения между анодом и катодом при разомкнутой цепи.
Фотодиоды удобно характеризовать семейством вольт-амперных характеристик, соответствующих различным световым потокам (световой поток измеряется в люменах, лм) или различным освещенностям (освещенность измеряется в люксах, лк).
Обратимся к вольт-амперным характеристикам (ВАХ) фотодиода. Пусть вначале световой поток равен нулю, тогда ВАХ фотодиода фактически повторяет ВАХ обычного диода. Если световой поток не равен нулю, то фотоны, проникая в область р-n-перехода, вызывают генерацию пар электрон-дырка. Под действием электрического поля р-n-перехода носители электрода движутся к электродам. В результате между электродами возникает напряжение, которое возрастает при увеличении светового потока. При положительном напряжении анод-катод ток диода может быть отрицательным (четвертый квадрант характеристики). При этом прибор не потребляет, а вырабатывает энергию.

В настоящее время коэффициент полезного действия солнечных элементов достигает 20%. Пока энергия, вырабатываемая солнечными элементами, примерно в 50 раз дороже энергии, получаемой из угля, нефти или урана. Но ожидается, что стоимость энергии, получаемой с помощью солнечных батарей, будет снижаться.
Фотодиоды являются более быстродействующими приборами по сравнению с фоторезисторами. Они работают на частотах 107—1010 Гц. Фотодиод часто используется в оптопарах светодиод-фотодиод.
Фотоэлементы с p-n-переходом
При освещении p-n-перехода в нем возникает э. д. с. Это явление используется в фотоэлементах с запирающим слоем, которые могут служить индикаторами лучистой энергии, не требующими внешнего питания, и преобразователями этой энергии в электрическую энергию.
Из p-полупроводника методом диффузии изготовляют тонкий слой, обладающий n-проводимостью. Между этим слоем и p-полупроводником образуется p-n-переход. При отсутствии света переход находится в равновесном состоянии и в нем устанавливается равновесный потенциальный барьер. При облучении перехода в p-области генерируются электронно-дырочные пары. Электроны, образовавшиеся в p-области, диффундируют к p-n-переходу и, подхватываясь контактным полем, перебрасываются в n-область. Дырки же преодолеть барьер не могут и остаются в p-области. Поэтому p-область заряжается положительно, n-область — отрицательно и в p-n-переходе появляется дополнительная разность потенциалов, приложенная в прямом направлении. Ее называют фотоэлектродвижущей силой.
![]() |
Принципиальная схема фотоэлемента (КПД ~15%)
Фоторезисторы
Фоторезистором называют полупроводниковый резистор, сопротивление которого чувствительно к электромагнитному излучению в оптическом диапазоне спектра.

Схематическое изображение структуры фоторезистора и его условное графическое обозначение
Поток фотонов, падающих на полупроводник, вызывает появление пар электрон-дырка, увеличивающих проводимость (уменьшающих сопротивление). Это явление называют внутренним фотоэффектом (эффектом фотопроводимости).
![]() |
Фоторезисторы часто характеризуются зависимостью тока от освещенности при заданном напряжении на резисторе. Это так называемая люкс-амперная характеристика.
Люкс-амперная характеристика фоторезистора
Графит
Графит является одной из аллотропических разновидностей углерода. Это полимерный материал кристаллического пластинчатого строения. Он образован параллельными слоями гексагональных сеток.

Кристаллическая решетка графита
В узлах каждой ячейки располагаются атомы углерода. Межатомное расстояние равно 0,143 нм. Между атомами действуют силы прочной ковалентной связи. Отдельные плоскости расположены на расстоянии 0,335 нм и связаны между собой ван-дер-ваальсовыми силами. Слоистая структура графита и слабая связь между соседними плоскостями обусловливают анизотропию всех свойств кристаллов графита во взаимно перпендикулярных направлениях. Между отдельными пластинками в решетке графита имеются свободные электроны, сообщающие графиту электро- и теплопроводность, металлический блеск.
Графит не плавится при атмосферном давлении, а при 3700°С сублимирует, минуя стадию плавления, с затратой значительной тепловой энергии на этот процесс.
Графит встречается в природе, а также получается искусственным путем. Качества природного графита невысоки, он содержит много примесей, порист, свойства почти изотропны. Поэтому его применяют лишь как антифрикционный материал и в электротехнике. Искусственные виды графита: технический и пиролитический. Эти виды графита обладают совершенной кристаллической структурой, высокой анизотропией свойств и являются высокотемпературными конструкционными материалами.
В качестве исходных материалов при производстве технического графита применяют твердое сырье — нефтяной кокс и каменноугольный пек в качестве связующего вещества. Заготовки формуются в процессе прессования или протяжки. Процесс графитизации осуществляется путем нагрева заготовок (обожженных при 1200°С) до 3000 С. Технический графит имеет степень анизотропии физико-механических свойств 3:1.
Паралитический графит получается из газообразного сырья. Он представляет собой продукт пиролиза углеводородов (метана), который осаждается на нагретых до 1000-2500 °С поверхностях формы из технического графита или керамики.
Полученный пирографит можно отделить от подложки и получить деталь или наносить его в виде покрытия на различные материалы с целью защиты их от действия высоких температур. Пирографит характеризуется степенью анизотропии, равной 100 (и более) : 1.
Для повышения качества технического графита применяется рекристаллизация при обжатии под давлением до 50 МП а и температуре свыше 2500°С, этим повышаются плотность и прочность графита.
Физико-механические свойства искусственного графита. Свойства графита зависят от природы исходного сырья, технологии получения, плотности, степени ориентации кристаллов и др.
Графит легко расщепляется по плоскости спайности. Твердость его небольшая. Плотность пористого графита составляет 200— 1200 кг/м3, конструкционного — 1500—1850 кг/м3, пирографита 960—2200 кг/м3. (Теоретическая плотность графита 2265 кг/м8.) Пористость может составлять 80 % и более.
Графит является очень хрупким материалом. Его прочность при сжатии выше, чем при изгибе и растяжении. Для графита характерно увеличение прочности и модуля упругости при нагреве. До температуры 2200— 2400°С прочность технического графита повышается на 40—60 % и лишь при дальнейшем нагреве прочность теряется. При температуре выше 1700°С проявляется ползучесть, которая имеет небольшую скорость при 2300—2900°С и напряжении 30—10 МПа. Графит хорошо проводит теплоту, поэтому его можно использовать и как проводник теплоты, и как теплоизолятор. Графит устойчив к воздействию тепловых ударов. Сочетание особых свойств графита делает его перспективным материалом высокой жаропрочности и теплозащитным материалом.
В условиях применения графита при высоких температурах, когда теплоотдача излучением является решающим фактором теплообмена, большое значение имеет степень черноты поверхности материала. Степень черноты графитовых материалов составляет 0,7—0,9, она возрастает при нагреве и шероховатости поверхности.
Графит обладает хорошими антифрикционными свойствами (f = 0,28), поэтому он применяется в качестве антифрикционных материалов, основным преимуществом которых является способность работать без смазывания в условиях высоких или низких температур, больших скоростей, агрессивных сред и т.п.
Недостатком графита является склонность его к окислению, начиная с температур 400—800°С, с выделением газообразных продуктов. Поэтому поверхность графита защищают введением легирующих добавок (Nb, Та, Si), которые делают структуру графита мелкозернистой, повышают его твердость и прочность, или нанесением защитных покрытий. Применяют силицирование графита путем обработки его поверхности парами кремнезема (при этом на поверхности графита образуется карбид кремния, обладающий высокой твердостью и прочностью) или нанесением покрытия из керамики.
Графит применяют в высоконагреваемых конструкциях летательных аппаратов и их двигателей, в энергетических ядерных реакторах, в качестве антифрикционного материала и в виде углеграфитовых волокнистых изделий.
Холодная и горячая деформации
Деформирование металлов подразделяют на холодное и горячее в зависимости от температуры. Холодное деформирование проводят ниже температуры рекристаллизации, металл наклепывается и сохраняет наклеп. Горячее деформирование приводят выше температуры рекристаллизации, когда получаемый наклеп снимается одновременно протекающей рекристаллизацией. Если рекристаллизация не устраняет наклеп, то он сохраняется частично или полностью. Это достигается при особых условиях обработки и охлаждения металла. Например, горячее деформирование с высокими скоростями и большими деформациями с дальнейшим быстрым охлаждением металла ниже температуры рекристаллизации сохраняет наклеп.
Хромирование (Cr)
Хромирование (поверхностное насыщение хромом) проводят для повышения коррозионной стойкости, кислостостойкости, окалиностойкости (до 850° С) и т. д. Хромирование средне- и высокоуглеродистых сталей повышает твердость и износостойкость.
Хромирование чаще всего проводят в порошкообразных смесях (50% металлического хрома или феррохрома, 49% окиси алюминия и 1% хлористого аммония). Процесс осуществляется при температуре 1000—1050°С. Диффузионный слой, получаемый при хромировании углеродистых сталей, состоит из карбидов хрома. Толщина хромированного слоя достигает 0,15—0,20 мм при длительности процесса 6—15 ч. Чем больше углерода в стали, тем меньше толщина слоя.
Значительно реже применяется газовое хромирование. Процесс проводят в среде, содержащей пары CrCl2. Пары CrCl2 получают пропусканием осушенных Н2 и НС1 через феррохром или хром при температуре 980°С. За 3-5 ч получают слой толщиной 0,06-0,10 мм.
Иногда применяют хромирование в вакууме. Изделия засыпают кусочками (диаметром 1—3 мм) хрома в стальном или керамическом тигле и помещают в вакуумную печь. При высокой температуре (960—1000° С) хром испаряется и диффундирует в сталь.
Хромирование применяют для пароводяной арматуры, клапанов, вентилей, а также деталей, работающих в агрессивных средах.
Износостойкость в больше,чем при шлифовке. Для коленчатых валов предел выносливости повышается на .
Эффект Холла
Предположим, что по пластине проводника, имеющей ширину a и толщину b, течет ток плотностью i. Выберем на боковых сторонах пластины точки C и D, разность потенциалов между которыми равна нулю. Если эту пластину поместить в магнитное поле с индукцией B, то между точками C и D возникает разность потенциалов VХ, называемая э. д. с. Холла. В не слишком сильных полях
Vx = rh Bai
Коэффициент пропорциональности rh называют постоянной Холла. Она имеет размерность L3/Q (L — длина, Q — электрический заряд) и измеряется в кубических метрах на кулон, (м3/Кл). Рассмотрим физическую природу эффекта Холла.
На электрон, движущийся справа налево со скоростью v, действует сила Лоренца Fл: Fл = qvB

Под действием силы Лоренца электроны отклоняются к внешней грани пластины, заряжая ее отрицательно. На противоположной грани накапливаются нескомненсированные положительные заряды. Это приводит к возникновению электрического поля, направленного от C к D. Поле EХ действует на электроны с силой f = qEx, направленной против силы Лоренца. При f — Fл поперечное электрическое поле уравновешивает силу Лоренца и дальнейшее накопление электрических зарядов на боковых гранях пластины прекращается.
Эффект Холла получил наиболее широкое практическое применение из всех гальваномагнитных явлений. Помимо исследования электрических свойств материалов он послужил основой для устройства большого класса приборов: магнитометров, преобразователей постоянного тока в переменный и переменного в постоянный, усилителей постоянного и переменного тока, генераторов сигналов переменного тока, фазометров, микрофонов и т. д.
Карбоволокниты
Карбоволокниты (углепласты) представляют собой композиции, состоящие из полимерного связующего (матрицы) и упрочнителей в виде углеродных волокон (карбоволокон).
Высокая энергия связи С—С углеродных волокон позволяет им сохранять прочность при очень высоких температурах (в нейтральной и восстановительной средах до 2200°С), а также при низких температурах. От окисления поверхности волокна предохраняют защитными покрытиями. В отличие от стеклянных волокон карбоволокна плохо смачиваются связующим (низкая поверхностная энергия), поэтому их подвергают травлению. При этом увеличивается степень активирования углеродных волокон по содержанию карбоксильной группы на их поверхности. Межслойная прочность при сдвиге углепластиков увеличивается в 1,6—2,5 раза.
Карбоволокниты отличаются высоким статическим и динамическим сопротивлением усталости, сохраняют это свойство при нормальной и очень низкой температуре (высокая теплопроводность волокна предотвращает саморазогрев материала за счет внутреннего трения). Они водо- к химически стойкие.
Карбостекловолокниты содержат наряду с угольными стеклянные волокна, что удешевляет материал.
Карбоволокниты с углеродной матрицей. Коксованные материалы получают из обычных полимерных карбоволокнитов, подвергнутых пиролизу в инертной или восстановительной атмосфере. При температуре 800—1500°С образуются карбонизированные, при 2500—3000°С графитированные карбоволокниты. Для получения пироуглеродных материалов упрочнитель выкладывается по форме изделия и помещается в печь, в которую пропускается газообразный углеводород (метан). При определенном режиме (температуре 1100°С и остаточном давлении 2660 Па) метан разлагается и образующийся пиролитический углерод осаждается на волокнах упрочнителя, связывая их.
Образующийся при пиролизе связующего кокс имеет высокую прочность сцепления с углеродным волокном. В связи с этим композиционный материал обладает высокими механическими и абляционными свойствами, стойкостью к термическому удару.
Карбоволокнит с углеродной матрицей типа КУП-ВМ по значениям прочности и ударной вязкости в 5—10 раз превосходит специальные графиты; при нагреве в инертной атмосфере и вакууме он сохраняет прочность до 2200°С, на воздухе окисляется при 450 °С и требует защитного покрытия. Коэффициент трения одного карбоволокнита с углеродной матрицей по другому высок (0,35—0,45), а износ мал (0,7—1 мкм на торможение).
Полимерные карбоволокниты используют в судо- и автомобилестроении (кузова гоночных машин, шасси, гребные винты); из них изготовляют подшипники, панели отопления, спортивный инвентарь, части ЭВМ. Высокомодульные карбоволокниты применяют для изготовления деталей авиационной техники, аппаратуры для химической промышленности, в рентгеновском оборудовании и др.
Карбоволокниты с углеродной матрицей заменяют различные типы графитов. Они применяются для тепловой защиты, дисков авиационных тормозов, химически стойкой аппаратуры.
Керамика
Керамика — неорганический материал, получаемый из отформованных минеральных масс в процессе высокотемпературного обжига. В результате обжига (1200—2500°С) формируется структура материала (спекание), и изделие приобретает необходимые физико-механические свойства.
Техническая керамика включает искусственно синтезированные керамические материалы различного химического и фазового состава; она обладает специфическими комплексами свойств. Такая керамика содержит минимальное количество или совсем не содержит глины. Основными компонентами технической керамики являются оксиды и бескислородные соединения металлов. Любой керамический материал является многофазной системой. В керамике могут присутствовать кристаллическая, стекловидная и газовая фазы.
Кристаллическая фаза представляет собой определенные химические соединения или твердые растворы. Эта фаза составляет основу керамики и определяет значения механической прочности, термостойкости и других ее основных свойств.
Стекловидная фаза находится в керамике в виде прослоек стекла, связывающих кристаллическую фазу. Обычно керамика содержит 1—10 % стеклофазы, которая снижает механическую прочность и ухудшает тепловые показатели. Однако стеклообразующие компоненты (глинистые вещества) облегчают технологию изготовления изделий.
Газовая фаза представляет собой газы, находящиеся в порах керамики; по этой фазе керамику подразделяют на плотную, без открытых пор и пористую. Наличие даже закрытых пор нежелательно, так как снижается механическая прочность материала.
Большинство видов специальной технической керамики обладает плотной спекшейся структурой поликристаллического Строения, для ее получения применяют специфические технологические приемы.
Керамика на основе чистых оксидов
В производстве оксидной керамики используют в основном следующие оксиды: А12О3 (корунд), ZrO2, AlgO, CaO, BeO. Структура керамики однофазная поликристаллическая. Кроме кристаллической фазы может содержаться небольшое количество газов (поры) и стекловидной фазы, которая образуется в результате наличия примесей в исходных материалах.
Температура плавления чистых оксидов превышает 2000 °С, поэтому их относят к классу высокоогнеупоров. Как и для других неорганических материалов, оксидная керамика обладает высокой прочностью при сжатии по сравнению с прочностью при растяжении или изгибе; более прочными являются мелкокристаллические структуры, так как при крупнокристаллическом строении на границе между кристаллами возникают значительные внутренние напряжения.
С повышением температуры прочность керамики понижается. При использовании материалов в области высоких температур важным свойством является окисляемость. Керамика из чистых оксидов, как правило, не подвержена процессу окисления.
Керамика на основе А12О3 (корундовая) обладает высокой прочностью, которая сохраняется при высоких температурах, химически стойка, отличный диэлектрик. Термическая стойкость корунда невысокая. Изделия из него широко применяют во многих областях техники: резцы, используемые при больших скоростях резания, калибры, фильеры для протяжки стальной проволоки, детали высокотемпературных печей, подшипники печных конвейеров, детали насосов, свечи зажигания в двигателях внутреннего сгорания. Керамику с плотной структурой используют в качестве вакуумной, пористую — как термоизоляционный материал. В корундовых тиглях проводят плавление различных металлов, оксидов, шлаков. Корундовый материал микролит по свойствам превосходит другие инструментальные материалы.
Особенностью оксида циркония (ZrO2) является слабокислотная или инертная природа, низкий коэффициент теплопроводности. Рекомендуемые температуры применения керамики из ZrO2 2000— 2200°С; она используется для изготовления огнеупорных тиглей для плавки металлов и сплавов, как тепловая изоляция печей, аппаратов и реакторов, в качестве покрытия на металлах для защиты последних от действия температур.
Керамика на основе оксидов магния и кальция стойка к действию основных шлаков различных металлов, в том числе и щелочных. Термическая стойкость их низкая.
Оксид магния при высоких температурах летуч, оксид кальция способен к гидратации даже на воздухе. Их применяют для изготовления тиглей, кроме того, MgO используют для футеровки печей, пирометрической аппаратуры и т. д.
Керамика на основе оксида бериллия отличается высокой теплопроводностью, что сообщает ей высокую термостойкость. Прочностные свойства материала невысокие. Оксид бериллия обладает способностью рассеивать ионизирующее излучение высоких энергий, имеет высокий коэффициент замедления тепловых нейтронов, применяется для изготовления тиглей для плавки некоторых чистых металлов, в качестве вакуумной керамики в ядерных реакторах.
Керамика на основе оксидов тория и урана имеет высокую температуру плавления, но обладает высокой плотностью и радиоактивна. Эти виды керамики применяют для изготовления тиглей для плавки родия, платины, иридия и других металлов, в конструкциях электропечей, для тепловыделяющих элементов в энергетических реакторах.
Бескислородная керамика
К тугоплавким бескислородным соединениям относятся соединения элементов с углеродом — карбиды, с бором — бориды, с азотом — нитриды, с кремнием — силициды и с серой — сульфиды. Эти соединения отличаются высокими огнеупорностью (2500—3500°С), твердостью (иногда как у алмаза) и износостойкостью по отношению к агрессивным средам. Материалы обладают высокой хрупкостью. Сопротивление окислению при высоких температурах карбидов и боридов составляет 900—1000°С, несколько ниже оно у нитридов. Силициды могут выдерживать температуру 1300—1700°С.
Карбиды. Широкое применение получил карбид кремния — карборунд (SiC). Он обладает высокой жаростойкостью (1500— 1600°С), высокой твердостью, устойчивостью к кислотам и неустойчивостью к щелочам; применяется в качестве нагревательных стержней, защитных покрытий графита и в качестве абразива.
Бориды. Эти соединения обладают металлическими свойствами, их электропроводность очень высокая. Они износостойки, тверды, стойки к окислению.
В технике получили распространение дибориды тугоплавких металлов (TiB2, ZrB2 и др.). Их легируют кремнием или дисилицидами, что делает их устойчивыми до температуры их плавления. Диборид циркония стоек в расплавах алюминия, меди, чугуна, стали и др. Его используют для изготовления термопар, работающих при температуре свыше 2000°С в агрессивных средах, труб, емкостей, тиглей. Покрытия из боридов повышают твердость, химическую стойкость и износостойкость изделий.
Нитриды. Неметаллические нитриды являются высокотермостойкими материалами, имеют низкие теплопроводность и электропроводимость. При обычной температуре это изоляторы, а при высоких температурах — полупроводники. С повышением температуры коэффициент линейного расширения и теплоемкость увеличиваются. Твердость и прочность этих нитридов меньше, чем твердость и прочность карбидов и боридов. В вакууме при высоких температурах они разлагаются. Они стойки к окислению, действию металлических расплавов.
Силициды отличаются от карбидов и боридов полупроводниковыми свойствами, окалиностойкостью, они стойки к действию кислот и щелочей. Их можно применять при температуре 1300-1700°С, при 1000 °С они не реагируют с расплавленным свинцом, оловом и натрием. Дисилицид молибдена используется наиболее широко в качестве стабильного электронагревателя в печах при температуре 1700°С в течение нескольких тысяч часов. Из спеченного MoSi2 изготовляют лопатки газовых турбин, сопловые вкладыши двигателей; его используют как твердый смазочный материал для подшипников, для защитных покрытий тугоплавких металлов от высокотемпературного окисления.
Сульфиды. Из сульфидов нашел практическое применение только дисульфид молибдена, имеющий высокие антифрикционные свойства. Его применяют в качестве сухого вакуумстойкого смазочного материала. Рабочие температуры на воздухе от -150 до 435°С, в вакууме до 1100°С, в инертной среде до 1540°С. Дисульфид молибдена электропроводен, немагнитен, стоек к радиации, воде, инертным маслам и кислотам, кроме крепких НС1, HNO3, и царской водке.При температуре выше 400°С начинается процесс окисления с образованием оксидной пленки, а при 592 °С образуется МоО3, являющийся абразивом.
Классификация конструкционных материалов
Перечень конструкционных материалов, применяемых в машино- и приборостроении, велик, и классифицировать их можно по разным признакам. Большинство из них, такие, как стали, чугуны, сплавы на основе меди и легких металлов, являются универсальными. Они обладают многочисленными достоинствами и используются в различных деталях и конструкциях.
Наряду с универсальными применяют конструкционные материалы определенного функционального назначения: жаропрочные, материалы с высокими упругими свойствами, износостойкие, коррозионно- и жаростойкие.
Классификация подразделяет конструкционные материалы по свойствам, определяющим выбор материала для конкретных деталей конструкций. Каждая группа материалов оценивается соответствующими критериями, обеспечивающими работоспособность в эксплуатации. Универсальные материалы рассматриваются в нескольких группах, если возможность применения их определяется различными критериями. В соответствии с выбранным принципом классификации все конструкционные материалы подразделяют на следующие группы:
1. Материалы, обеспечивающие жесткость, статическую и циклическую прочность
2. Материалы с особыми технологическими свойствами
3. Износостойкие материалы
4. Материалы с высокими упругими свойствами
5. Материалы с малой плотностью
6. Материалы с высокой удельной прочностью
7. Материалы, устойчивые к воздействию температуры и рабочей среды
Классификация конструкционных сталей
Стали классифицируют по химическому составу, качеству, степени раскисления, структуре и прочности.
По химическому составу стали классифицируют на углеродистые и легированные. По концентрации углерода те и другие подразделяют на низкоуглеродистые (< 0,3 % С), среднеуглеродистые (0,3-0,7% С) и высокоуглеродистые (> 0,7% С). Легированные стали в зависимости от введенных элементов подразделяют на хромистые, марганцовистые, хромоникелевые, хромокремнемарганцевые и многие другие. По количеству введенных элементов их разделяют на низко-, средне- и высоколегированные. В низколегированных сталях количество легирующих элементов не превышает 5%, в среднелегированных содержится от 5 до 10%, в высоколегированных - более 10%.
По качеству стали классифицируют на стали обыкновенного качества, качественные, высококачественные и особовысококачественные.
Под качеством стали понимают совокупность свойств, определяемых металлургическим процессом ее производства. Однородность химического состава, строения и свойств стали, а также ее технологичность во многом зависят от содержания газов (кислорода, водорода, азота) и вредных примесей - серы и фосфора. Газы являются скрытыми, количественно трудно определяемыми примесями, поэтому нормы содержания вредных примесей служат основными показателями для разделения сталей по качеству. Стали обыкновенного качества содержат до 0,055% S и 0,045% Р, качественные - не более 0,04% S и 0,035% Р, высококачественные - не более 0,025% S и 0,025% Р, особовысококачественные - не более 0,015% S и 0,025% Р.
По степени раскисления и характеру затвердевания стали классифицируют на спокойные, полуспокойные и кипящие. Раскисление - процесс удаления из жидкого металла кислорода, проводимый для предотвращения хрупкого разрушения стали при горячей деформации.
Спокойные стали раскисляют марганцем, кремнием и алюминием. Они содержат мало кислорода и затвердевают спокойно без газовыделения.
Кипящие стали раскисляют только марганцем. Перед разливкой в них содержится повышенное количество кислорода, который при затвердевании, частично взаимодействуя с углеродом, удаляется в виде СО. Выделение пузырей СО создает впечатление кипения стали, с чем и связано ее название. Кипящие слали дешевы, их производят низкоуглеродистыми и практически без кремния (Si < 0,07%), но с повышенным количеством газообразных примесей.
Полуспокойные стали по степени раскисления занимают промежуточное положение между спокойными и кипящими.
При классификации стали по структуре
учитывают особенности ее строения в отожженном и нормализованном состояниях. По структуре в отожженном (равновесном) состоянии конструкционные стали разделяют на четыре класса: 1) доэвтектоидные, имеющие в структуре избыточный феррит; 2) эвтектоидные, структура которых состоит из перлита; 3) аустенитные; 4) ферритные. Углеродистые стали могут быть первых двух классов, легированные - всех классов.
Композиционные материалы с металлической матрицей
Композиционные материалы состоят из металлической матрицы, упрочненной высокопрочными волокнами (волокнистые материалы) или тонкодисперсными тугоплавкими частицами, не растворяющимися в основном металле (дисперсно-упрочненные материалы). Металлическая матрица связывает волокна (дисперсные частицы) в единое целое. Волокно (дисперсные частицы) плюс связка (матрица), составляющие ту или иную композицию, получили название композиционные материалы.

Схема структуры (а) и армирования непрерывными волокнами (б) композиционных материалов:
1 — зернистый (дисперсно-упрочненный) материал; 2 — дискретный волокнистый композиционный материал; 3 — непрерывно волокнистый композиционный материал; 4 — непрерывная укладка волокон; 5 — двухмерная укладка волокон; 6,7 — объемная укладка волокон
Композиционные материалы с волокнистым наполнителем по механизму армирующего действия делят на дискретные и с непрерывным волокном. Дискретные волокна располагаются в матрице хаотично. Диаметр волокон от долей до сотен микрометров. Чем больше отношение длины к диаметру волокна, тем выше степень упрочнения.
Часто композиционный материал представляет собой слоистую структуру, в которой каждый слой армирован большим числом параллельных непрерывных волокон. Каждый слой можно армировать также непрерывными волокнами, сотканными в ткань, которая представляет собой исходную форму, по ширине и длине соответствующую конечному материалу. Нередко волокна сплетают в трехмерные структуры.
Композиционные материалы отличаются от обычных сплавов более высокими значениями временного сопротивления и предела выносливости (на 50—100%), модуля упругости, коэффициента жесткости и пониженной склонностью к трещинообразованию. Применение композиционных материалов повышает жесткость конструкции при одновременном снижении ее металлоемкости.
Прочность композиционных материалов определяется свойствами волокон; матрица в основном должна перераспределять напряжения между армирующими элементами.
Поэтому прочность и модуль упругости волокон должны быть значительно больше, чем прочность и модуль упругости матрицы. Жесткие армирующие волокна воспринимают напряжения, возникающие в композиции при нагружении, придают ей прочность и жесткость в направлении ориентации волокон.
Материал |
?В |
?-1 |
E, ГПа |
?В/? |
E/ ? |
MПа |
|||||
Бор — алюминий Бор— магний Алюминий — углерод Алюминий — сталь Никель — вольфрам |
1300 1300 900 1700 700 |
600 500 300 350 150 |
220 220 220 110 |
500 590 450 370 |
84,6 100 100 24,40 |
Анизотропия свойств волокнистых композиционных материалов учитывается при конструировании деталей для оптимизации свойств путем согласования поля сопротивления в полями напряжения.
Армирование алюминиевых, магниевых и титановых сплавов непрерывными тугоплавкими волокнами бора, карбида кремния, диборида титана и оксида алюминия значительно повышает жаропрочность. Особенностью композиционных материалов является малая скорость разупрочнения во времени с повышением температуры.
Основным недостатком композиционных материалов с одно- и двумерным армированием является низкое сопротивление межслойному сдвигу и поперечному обрыву. Этого недостатка лишены материалы с объемным армированием.
Дисперсно-упрочненные композиционные материалы. В отличие от волокнистых композиционных материалов в дисперсно-упрочненных композиционных материалах матрица является основным элементом, несущим нагрузку, а дисперсные частицы тормозят движение в ней дислокаций.
Высокая прочность достигается при размере частиц 10—500 нм при среднем расстоянии между ними 100—500 нм и равномерном распределении их в матрице. Прочность и жаропрочность в зависимости от объемного содержания упрочняющих фаз не подчиняются закону аддитивности.
Использование в качестве упрочняющих фаз стабильных тугоплавких соединений (оксиды тория, гафния, иттрия, сложные соединения оксидов и редкоземельных металлов), нерастворяющихся в матричном металле, позволяет сохранить высокую прочность материала. В связи с этим такие материалы чаще применяют как жаропрочные. Дисперсно-упрочненные композиционные материалы могут быть получены на основе большинства применяемых в технике металлов и сплавов.
Наиболее широко используют сплавы на основе алюминия — САП (спеченный алюминиевый порошок). САП состоит из алюминия и дисперсных чешуек А12О3. Частицы А12О3 эффективно тормозят движение дислокаций и тем самым повышают прочность сплава. Плотность этих материалов равна плотности алюминия, они не уступают ему по коррозионной стойкости и даже могут заменять титан и коррозионно-стойкие стали при работе в интервале температур 250-500 °С. По длительной прочности они превосходят деформируемые алюминиевые сплавы. Длительная прочность для сплавов САП-1 и САП-2 при 500 °С составляет 45—55 МПа.
Большие перспективы у никелевых дисперсно-упрочненных материалов. Широкое применение получили сплавы ВДУ-1 (никель, упрочненный двуокисью тория), ВДУ-2 (никель, упрочненный двуокисью гафния) и ВД-3 (матрица Ni + 20 % Cr, упрочненная окисью тория). Эти сплавы обладают высокой жаропрочностью. Дисперсно-упрочненные композиционные материалы, так же как волокнистые, стойки к разупрочнению с повышением температуры и длительности выдержки при данной температуре.
Области применения композиционных материалов не ограничены. Они применяются в авиации для высоконагруженных деталей самолетов (обшивки, лонжеронов, нервюр, панелей и т. д.) и двигателей (лопаток компрессора и турбины и т.д.), в космической технике для узлов силовых конструкций аппаратов, подвергающихся нагреву, для элементов жесткости, панелей, в автомобилестроении для облегчения кузовов, рессор, рам, панелей кузовов, бамперов и т. д., в горной промышленности (буровой инструмент, детали комбайнов и т. д.), в гражданском строительстве (пролеты мостов, элементы сборных конструкций высотных сооружений и т. д.) и в других областях народного хозяйства.
Применение композиционных материалов обеспечивает новый качественный скачок в увеличении мощности двигателей, энергетических и транспортных установок, уменьшении массы машин и приборов.
Композиционные материалы с неметаллической матрицей
Композиционные материалы с неметаллической матрицей нашли широкое применение. В качестве неметаллических матриц используют полимерные, углеродные и керамические материалы. Из полимерных матриц наибольшее распространение получили эпоксидная, фенолоформальдегидная и полиимидная. Угольные матрицы коксованные или пироуглеродные получают из синтетических полимеров, подвергнутых пиролизу. Матрица связывает композицию, придавая ей форму. Упрочнителями служат волокна: стеклянные, углеродные, борные, органические, на основе нитевидных кристаллов (оксидов, карбидов, боридов, нитридов и др.), а также металлические (проволоки), обладающие высокой прочностью и жесткостью.
Свойства композиционных материалов зависят от состава компонентов, их сочетания, количественною соотношения и прочности связи между ними. Армирующие материалы могут быть в виде волокон, жгутов, нитей, лент, многослойных тканей.
Содержание упрочнителя в ориентированных материалах составляет 60—80%, в неориентированных (с дискретными волокнами и нитевидными кристаллами) 20—30%. Чем выше прочность и модуль упругости волокон, тем выше прочность и жесткость композиционного материала. Свойства матрицы определяют прочность композиции при сдвиге и сжатии и сопротивление усталостному разрушению.
По виду упрочнителя композиционные материалы классифицируют на стекловолокниты, карбоволокниты с углеродными волокнами, бороволокниты и органоволокниты.
В слоистых материалах волокна, нити, ленты, пропитанные связующим, укладываются параллельно друг другу в плоскости укладки. Свойства получаются анизотропными. Для работы материала в изделии важно учитывать направление действующих нагрузок. Можно создавать материалы как с изотропными, так и с анизотропными свойствами. Можно укладывать волокна под разными углами, варьируя свойства композиционных материалов. От порядка укладки слоев по толщине пакета зависят изгибные и крутильные жесткости материала.
Применяется укладка упрочнителей из трех, четырех и более нитей.
Наибольшее применение имеет структура из трех взаимно перпендикулярных нитей. Упрочнители могут располагаться в осевом, радиальном и окружном направлениях.
Трехмерные материалы могут быть любой толщины в виде блоков, цилиндров. Объемные ткани увеличивают прочность на отрыв и сопротивление сдвигу по сравнению со слоистыми. Система из четырех нитей строится путем расположения упрочнителя по диагоналям куба. Структура из четырех нитей равновесна, имеет повышенную жесткость при сдвиге в главных плоскостях. Однако создание четырехнаправленных материалов сложнее, чем трехнаправленных.
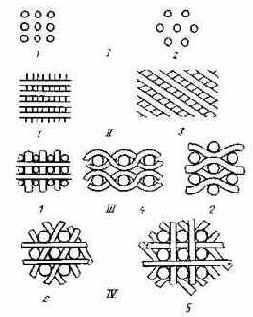
Схемы армирования композиционных материалов: I - однонаправленная; II - двухнаправленная; III - трехнаправленная; IV - четырехнаправленная.
Укладка волокон (1 - прямоугольная, 2 - гексагональная, 3 - косоугольная, 4 - с искривленными волокнами, 5 - система из n нитей)
Кристаллизация металлов
Переход металла из жидкого или парообразного состояния в твердое с образованием кристаллической структуры называется первичной кристаллизацией. Образование новых кристаллов в твердом кристаллическом веществе называется вторичной кристаллизацией.
Процесс кристаллизации состоит из двух одновременно идущих процессов - зарождения и роста кристаллов. Кристаллы могут зарождаться самопроизвольно (самопроизвольная кристаллизация) или расти на имеющихся готовых центрах кристаллизации (несамопроизвольная кристаллизация).
Легированные стали
Маркировка легированных сталей состоит из сочетания букв и цифр, обозначающих ее химический состав. По ГОСТ 4543-71 принято обозначать хром - X, никель - Н, марганец - Г, кремний-С, молибден-М, вольфрам-В, титан-Т, ванадий-Ф, алюминий - Ю, медь-Д, ниобий - Б, бор-Р, кобальт-К. Цифра, стоящая после буквы, указывает на примерное содержание легирующего элемента в процентах. Если цифра отсутствует, то легирующего элемента меньше или около 1 %.
Две цифры в начале марки конструкционной легированной стали показывают содержание углерода в сотых долях процента. Например, сталь 20ХНЗА в среднем содержит 0,20%С, 1 % Сг и 3 % Ni. Буква А в конце марки означает, что сталь высококачественная. Особовысококачественные стали имеют в конце марки букву Ш.
Некоторые группы сталей содержат дополнительные обозначения: марки шарикоподшипниковых сталей начинаются с буквы Ш, электротехнических - с буквы Э, автоматных - с буквы А.
Влияние легирующих элементов на механические свойства сталей
Легирующие элементы вводят для повышения конструкционной прочности стали. Легированные стали производят качественными, высококачественными или особовысококачественными. Их применяют после закалки и отпуска, поскольку в отожженном состоянии они по механическим свойствам практически не отличаются от углеродистых.
Улучшение механических свойств обусловлено влиянием легирующих элементов на свойства феррита, дисперсность карбидной фазы, устойчивость мартенсита при отпуске, прокаливаемость, размер зерна.
В конструкционных сталях феррит — основная структурная составляющая (не менее 90% по объему), во многом определяющая их свойства. Легирующие элементы, растворяясь в феррите, упрочняют его. Наиболее сильно повышают твердость медленно охлажденного феррита кремний, марганец, никель, т. е. элементы, имеющие отличную от него кристаллическую решетку.
К важнейшим факторам, способствующим повышению конструкционной прочности, относятся снижение при легировании критической скорости закалки и увеличение прокаливаемости. Наиболее эффективно повышает прокаливаемость введение нескольких элементов : Cr + Mo, Cr + Ni, Cr + Ni + Mo и др. При комплексном легировании высокие механические свойства можно получить практически в сечении любого размера, поэтому комплексно-легированные стали применяют для крупных деталей сложной формы. Большинство легирующих элементов измельчает зерно, что способствует повышению работы развития трещины и снижению порога хладноломкости.
Для обеспечения высокой конструкционной прочности количество легирующих элементов в стали должно быть рациональным. После достижения необходимой прокаливаемости избыточное легирование (за исключением никеля) снижает трещиностойкость и облегчает хрупкое разрушение.
Литье по выплавляемым моделям
Модель изготавливается из парафина, стеарина, церезина и других материалов. В роли связующего выступает кварцевый песок совместно с этил силикатом.
Недостатком этого метода является то, что используемые формы однократного применения, у которых маленькая толщина оболочки, то есть детали получаются небольших размеров (до 10кг).
Литье под давлением
Литье под давлением является одним из самых прогрессивных методов получения отливок из цветных сплавов.
Сущность процесса литья под давлением состоит в том, что в стальную пресс-форму под большим давлением и с большой скоростью вводится расплавленный металл. При этом происходит мгновенное заполнение всей полости формы любой сложной конфигурации. Этот метод обеспечивает получение тонкостенных отливок с чистой поверхностью и точными размерами. Литье под давлением по сравнению с другими способами получения отливок имеет ряд преимуществ:
Высокая точность размеров отливки
В основном точность размеров отливок соответствует 5-му классу точности по ГОСТу 2689-54. Точность размеров отливки зависит от точности изготовления пресс-формы, состава сплава и его температуры, температуры формы и продолжительности выдержки металла под давлением.
Высокий класс чистоты поверхности отливок
Шероховатость поверхности отливок соответствует 6-му классу чистоты по ГОСТу 2789-59. Чистота поверхности отливок зависит в первую очередь от чистоты обработки пресс-формы (ухудшается по мере износа формы) и от применяемых сплавов. Шероховатость поверхности алюминиевых и магниевых отливок соответствует 5-8-му классу чистоты.
Минимальный объем механической обработки отливок
В сочетании с высокой точностью размеров и высокой чистотой поверхности детали, отлитые под давлением, в большинстве случаев не требуют последующей механической обработки.
Минимальный расход металла
Этим методом можно изготовлять тонкостенные отливки, получение которых другими методами литья невозможно. Изготовление отливок без припусков на механическую обработку приводит к минимальному расходу дорогостоящих цветных металлов.
Высокая прочность
Благодаря быстрому охлаждению отливки приобретают мелкозернистую структуру и повышенную прочность. Чем меньше толщина стенки отливки, тем больше ее прочность.
По сравнению с другими способами литье под давлением позволяет полностью механизировать и автоматизировать технологический процесс получения отливок и имеет самый короткий производственный цикл. Указанные преимущества литья под давлением приводят к значительному повышению производительности труда, улучшению условий труда и снижению себестоимости отливок в несколько раз.
Однако преимущества литья под давлением проявляются главным образом в крупносерийном и массовом производстве, когда очень быстро окупаются затраты на изготовление стальных пресс-форм. Стойкость пресс-форм зависит от применяемых сплавов и является одним из основных факторов, определяющих себестоимость деталей, получаемых литьем под давлением, и целесообразность применения этого способа.
Литье под давлением широко применяется в автомобилестроении, приборостроении, авиационной промышленности, в радиотехнике и электропромышленности, а также и в других отраслях машиностроения. Этому способствует создание все более мощных машин литья под давлением, позволяющих расширить ассортимент отливок, увеличить их габаритные размеры и сложность, а также повысить качество отливок.
Литье под низким давлением
Особенностью этого способа является заполнение формы расплавом снизу вверх непосредственно из печи и кристаллизации отливки под действием низкого давления.
На крышку герметичного металлического тигля, помещенного в электропечь, установлена металлическая форма. Через крышку тигля проходит один или два металлопровода, немного не доходящих до дна тигля. Верхняя часть металлопровода через литниковую втулку сообщается с коллектором литниковой системы. Внутренняя полость отливки оформляется песчаным стержнем, внутри которого находится трубчатый литой каркас. На металлическую форму установлен песчаный стержень с фильтром из стружки. По трубопроводу в тигель подается сжатый воздух или инертный газ, который, оказывая давление на поверхность сплава, вытесняет его по металлопроводу вверх в литниковую систему и через нее в полость формы.
Сначала расплав подается медленно, затем, достигнув электроконтакта в нижней части формы, включает дополнительное давление пневмосистемы и быстро заполняет полость формы. Достигнув второго электроконтакта, расплав включает прибор, прекращающий дальнейшее повышение давления пневмосистемы. Давление поддерживается на постоянном уровне до полного затвердения отливки. Стружковый фильтр пропускает воздух, вытесняемый из формы поступающим расплавом, но препятствует выходу металла, обеспечивая плавное торможение потока в конце заполнения полости формы.
После затвердевания отливки давление в тигле автоматически сбрасывается, форма раскрывается и отливка извлекается.
Автоматическое управление скоростью заполнения формы металлом впервые осуществлено при разработке машин для литья под низким давлением. Литье под низким давлением применяется при изготовлении сложных крупногабаритных тонкостенных деталей из алюминиевых и магниевых сплавов.
Литье в кокиль
Повышенные механические свойства и плотность
Вследствие большой скорости охлаждения жидкого металла в кокиле образуется мелкокристаллическая структура отливок, что способствует повышению их плотности и механических свойств.
Повышенная точность размеров и чистота поверхности отливок
Благодаря более точным и стабильным размерам металлических форм и более чистой их поверхности повышается точность размеров и чистота поверхности отливок. Точность отливок из алюминиевых и магниевых сплавов при литье в кокиль на два класса выше, чем при литье в песчаные формы.
Меньшие припуски на механическую обработку
Вследствие большей точности и чистоты поверхности отливок при литье в кокиль припуски на механическую обработку отливок на 40—50% меньше, чем при литье в песчаные формы.
Экономия формовочных и вспомогательных материалов
При литье в кокиль алюминиевых и магниевых сплавов применяют незначительную часть песчаных стержней, на которые расходуется меньше формовочных и вспомогательных материалов, чем при литье в песчаные формы.
По мере роста удельного веса литья в кокиль в общем производстве отливок расход формовочных и вспомогательных материалов резко снижается. Соответственно уменьшаются грузопоток и затраты на приготовление и транспортировку этих материалов.
Снижение брака
Более стабильные условия технологического процесса литья в кокиль по сравнению с литьем в песчаные формы дают возможность снизить брак.
Снижение расхода металла
Получение более точных отливок с меньшими припусками на механическую обработку, уменьшение веса литниковой системы, а также увеличение с 20 до 30% использования отходов в шихте при литье в кокиль цветных сплавов позволяет уменьшить черновой вес отливок и снизить расход свежих чушковых материалов. Экономия свежих металлов при литье в кокиль достигает на отдельных отливках от 37 до 75%.
Снижение трудоемкости
При литье в кокиль сокращается производственный цикл изготовления отливок, так как исключаются операции приготовления формовочных смесей и формовки, уменьшается объем изготовления и сушки песчаных стержней, плавки металла и отделки отливок. В результате значительно снижается трудоемкость производства отливок.
Снижение себестоимости
Перечисленные выше преимущества литья в кокиль приводят к снижению себестоимости отливок из цветных сплавов.
Кроме того, при литье в кокиль облегчается очистка и обрубка литья, значительно уменьшается число применяемого оборудования (формовочных и стержневых машин, очистного и другого технологического и транспортного оборудования). Увеличивается съем литья с квадратного метра производственной площади и резко улучшаются санитарно-технические условия труда.
Литье в оболочковые формы
Преимущества этого метода заключаются в высокой точности отлива, также получается низкая шероховатость поверхности и малый расход формовочного материала.
Недостатками этого метода являются ограничения по массе у детали (до 100кг), также формы можно использовать малое число раз (2÷3 раза), что способствует низкой производительности.
Литье в землю
Недостатки этого метода заключаются в том, что поверхность детали получается шероховатой, охлаждение детали происходит очень медленно, то есть производительность будет низкой, также такой детали присущи низкие механические свойства, так как кристаллизация происходит длительное время и образуется крупнозернистая структура у детали.
Литье выжиманием
Для получения крупногабаритных тонкостенных деталей панельного типа изобрели новый способ литья в металлические формы со сближающимися стенками. Разработанный по этому принципу литейный процесс назван «литье выжиманием».
Залитый в нижнюю часть раскрытой формы (металлоприемник) жидкий сплав по мере сближения стенок закрывающейся формы поднимается и заполняет ее. При этом на стенках формы идет наращивание кристаллизующегося сплава, удаление избытка расплава наружу и соединение в одно целое закристаллизовавшегося сплава.
Литье выжиманием имеет следующие две особенности, определяющие его сущность как метода получения тонкостенных деталей с большой поверхностью:
1. Процесс заполнения формы расплавом происходит сплошным потоком, сечение которого во много раз превосходит толщину стенки отливки. В результате намного снижаются гидравлические потери при заполнении полости формы и создаются условия замедленной кристаллизации сплава.
2. Формообразование отливки происходит в процессе сжимания потока жидкого сплава в два этапа. Сначала сплав кристаллизуется на стенках формы в виде корки с постепенным наращиванием толщины слоя за счет расплава, непрерывно подаваемого из металлоприемника в зоны кристаллизации. Затем корки соединяются в цельную отливку с одновременным удалением избытка жидкого металла вместе с находящимися в нем загрязнениями.
Медные сплавы
Свойства меди. Медь металл красновато-розового цвета; кристаллическая ГЦК решетка, полиморфных превращений нет. Медь менее тугоплавка, чем железо, но имеет большую плотность. Медь обладает хорошей технологичностью. Она прокатывается в тонкие листы, ленту. Из меди получают тонкую проволоку, медь легко полируется, хорошо паяется и сваривается. Медь характеризуется высокими теплопроводностью и электропроводимостью, пластичностью и коррозионной стойкостью.
Примеси снижают все эти свойства. По ГОСТ 859-78 в зависимости от содержания примесей различают следующие марки меди: М00 (99,99%Cu), М0 (99,97%Cu), M1 (99,9%Cu), М2 (99,7%Cu), МЗ (99,5%Cu). Наиболее часто встречающиеся в меди примеси подразделяют на три группы.
1. Растворимые в меди элементы Al, Fe, Ni, Zn, Ag повышают прочность и твердость меди и используются для легирования сплавов на медной основе.
2. Нерастворимые элементы РЬ и Bi ухудшают механические свойства меди и однофазных сплавов на ее основе. Образуя легкоплавкие эвтектики, располагающиеся по границам зерен основной фазы, они вызывают красноломкость. Причем вредное влияние висмута обнаруживается при его содержании в тысячных долях процента, поскольку его растворимость ограничивается 0,001%. Вредное влияние свинца также проявляется при малых его содержаниях (< 0,04 %). Висмут, будучи хрупким металлом, охрупчивает медь и ее сплавы. Свинец, обладая низкой прочностью, снижает прочность медных сплавов, однако вследствие хорошей пластичности не вызывает их охрупчивания. Кроме того, свинец улучшает антифрикционные свойства и обрабатываемость резанием медных сплавов, поэтому применяется для легирования двухфазных сплавов меди.
3. Нерастворимые примеси O, S, Se, Tl присутствуют в меди и ее сплавах в виде промежуточных фаз, которые образуют с медью эвтектики с высокой температурой плавления и не вызывают красноломкости.
Кислород при отжиге меди в водороде вызывает «водородную болезнь», которая может привести к разруше нию металла при обработке давлением или эксплуатации готовых деталей.
Механические свойства меди в большой степени зависят от ее состояния и в меньшей от содержания примесей. Высокая пластичность чистой отожженной меди объясняется большим количеством плоскостей скольжения. Холодная пластическая деформация (достигающая 90% и более) увеличивает прочность, твердость, предел упругости меди, но снижает пластичность и электрическую проводимость. При пластической деформации возникает текстура, вызывающая анизотропию механических свойств меди. По электропроводимости и теплопроводности медь занимает второе место после серебра. Она применяется для проводников электрического тока и различных теплообменников, водоохлаждаемых изложниц, поддонов, кристаллизаторов.
Недостатки меди: высокая плотность, плохая обрабатываемость резанием и низкая жидкотекучесть.
Общая характеристика и классификация медных сплавов. Сохраняя положительные качества меди (высокие теплопроводность и электропроводимость, коррозионную стойкость и др.), медные сплавы обладают хорошими механическими, технологическими и антифрикционными свойствами.
Для легирования медных сплавов в основном используют элементы, растворимые в Cu, Zn, Sn, Al, Be, Si, Mn, Ni. Повышая прочность медных сплавов, легирующие элементы практически не снижают, а некоторые из них (Zn, Sn, Al) увеличивают пластичность. Высокая пластичность - отличительная особенность медных сплавов. По прочности медные сплавы уступают сталям.
По технологическим свойствам медные сплавы подразделяют на деформируемые (обрабатываемые давлением) и литейные; по способности упрочняться с помощью термической обработки - на упрочняемые и неупрочняемые. По химическому составу медные сплавы подразделяют на две основные группы: латуни и бронзы.
Латунями называются сплавы меди с цинком.
Они бывают двойными (простые) и многокомпонентными (легированные). Двойные деформируемые латуни маркируются буквой Л (латунь) и цифрой, показывающей среднее содержание меди в процентах. Латуни с содержанием 90% Cu и более называются томпаком (Л96), при 80 - 85%Cu — полутомпаком (Л80). В марках легированных латуней кроме цифры, показывающей содержание меди, даются буквы и цифры, обозначающие название и количество в процентах легирующих элементов. Алюминий в медных сплавах обозначают буквой А, никель-Н, олово-О, свинец-С, фосфор-Ф, железо-Ж, кремний-К, марганец-Мц, бериллий-Б, цинк-Ц. Например, ЛАН59-3-2 содержит 59%Cu, 3% Аl, 2% Ni. В марках литейных латуней указывается содержание цинка, а количество каждого легирующего элемента ставится непосредственно за буквой, обозначающей его название. Например, ЛЦ40МцЗА содержит 40% Zn, 3% Mn, 1% Al.
Бронзами называются сплавы меди со всеми элементами кроме цинка. Название бронзам дают по основным элементам. Так, их подразделяют на оловянные, алюминиевые, бериллиевые, кремнистые и др. В бронзах в качестве легирующей добавки может присутствовать цинк. Деформируемые бронзы маркируют буквами Бр (бронза), за которыми следуют буквы, а затем цифры, обозначающие название и содержание в процентах легирующих элементов. Например, БрОЦС4-4-2,5 содержит 4% Sn, 4 % Zn, 2,5 % Pb. Сплавы меди с никелем имеют названия: мельхиоры, куниали, нейзильберы. В марках литейных бронз содержание каждого легирующего элемента ставится сразу после буквы, обозначающей его название. Например, БрО6Ц6СЗ содержит 6% Sn, 6% Zn, 3% Pb.
Свойства промышленных латуней, обрабатываемых давлением
Латунь |
Массовая доля, % |
?в |
?0,2 |
?,% |
HB |
|
Cu |
Прочих элементов |
MПа |
||||
Л90 Л68 Л63 Л 60 ЛА77-2 ЛАН59-3-2 ЛН65-5 ЛЖМц59- 1-1 ЛМц58-2 ЛО70-1 ЛС59-1 ЛК80-3 |
88-91 67-70 62-65 59-62 76-79 57-60 64-67 57-60 57-60 69-71 57-60 79-81 |
- - - - 1,75-2,5 А1 2,5-3,5 А1 2-3 Ni 5-6,5 Ni 0,1-0,4 Al 0,6-1,2 Fe 0,5-0,8 Mn 0,3-0,7 Sn 1-2 Mn 1-1,5 Sn 0,8-1,9 Pb 2,5-4 Si |
260 320 330 380 400 380 400 450 400 350 400 300 |
120 91 110 160 140 300 170 170 160 100 140 200 |
45 55 50 25 55 50 65 50 40 60 45 58 |
530 550 560 770 600 750 600 880 850 600 900 1000 |
Механические свойства материалов
Из всех свойств, которыми обладают твердые тела, наиболее характерными являются механические свойства — прочность, твердость, пластичность, износостойкость и др. Именно благодаря этим свойствам твердые тела получили столь широкое практическое применение в качестве конструкционных, строительных, электротехнических, магнитных и других материалов, без которых немыслимо развитие материального производства. Рассмотрим некоторые из этих свойств.
Металлопласты
Полимерные материалы (пластмассы), наполненные металлическим заполнителем в виде порошков, волокон, ткани, называются металлопластами.
Металл сообщает таким композициям ряд специальных свойств — магнитных (при наполнении железом, пермаллоем и т. д.), повышенную электро- и теплопроводность, поглощение и отражение радиоволн, повышенную демпфирующую способность и т. д.
Полимеры, наполненные магнитными порошками, называются магнитодиэлектриками.
Нагрев для снятия остаточных напряжений
Многие технологические воздействия на обрабатываемые детали сопровождаются возникновением в них остаточных напряжений, которые уравновешиваются в объеме детали. Значительные остаточные напряжения возникают в отливках и полуфабрикатах, неравномерно охлаждающихся после проката или ковки, в холоднодеформированных полуфабрикатах или заготовках, в прутках в процессе правки, в сварных соединениях, при закалке и т. п.
Остаточные напряжения, возникшие в указанных случаях, чаще всего нежелательны. Они могут вызвать деформацию деталей при обработке резанием или в процессе эксплуатации, а, суммируясь с напряжениями от внешних нагрузок, привести к преждевременному разрушению или короблению конструкции; увеличивая запас упругой энергии, остаточные напряжения повышают вероятность хрупкого разрушения. Во многих сплавах они вызывают склонность к растрескиванию в присутствии коррозионно-активной среды. По величине остаточные напряжения могут достигать предела текучести.
Для уменьшения остаточных напряжений изделия нагревают. С повышением температуры предел текучести понижается, поэтому остаточные напряжения вызывают пластическую деформацию и снижаются до уровня предела текучести металла при температуре нагрева.
В стальных и чугунных деталях значительное снижение остаточных напряжений происходит в процессе выдержки при температуре 450 °С; после выдержки при температуре 600 °С напряжения понижаются до очень низких значений. Время выдержки устанавливается от нескольких до десятков часов и зависит от массы изделия.
В сплавах на основе меди и алюминия существенное уменьшение остаточных напряжений происходит при меньших температурах нагрева. Например, в холоднодеформированных латунных полуфабрикатах остаточные напряжения практически полностью снимаются в процессе отжига при 250-300°С
По окончании выдержки при заданной температуре изделия медленно охлаждают, чтобы предотвратить возникновение новых напряжений. Допустимая скорость охлаждения зависит от массы изделия, его формы и теплопроводности материала; она обычно лежит в пределах 20-200 °С/ч.
Назначение и виды химико-термической обработки
Химико-термической обработкой называется процесс поверхностного насыщения стали различными элементами путем их диффузии из внешней среды при высокой температуре. Цель химико-термической обработки — поверхностное упрочнение металлов и сплавов и повышение их стойкости против воздействия внешних агрессивных сред при нормальной и повышенных температурах.
Процессы химико-термической обработки состоят из трех стадий:
- диссоциации, которая заключается в распаде молекул и образовании активных атомов диффундирующего элемента;
- адсорбции, т. е. контактирования атомов диффундирующего элемента с поверхностью стального изделия и образования химических связей с атомами металла;
- диффузии, т. е. проникновения насыщающего элемента в глубь металла.

Концентрация диффундирующего элемента на поверхности зависит от притока атомов этого элемента к поверхности и от скорости диффузионных процессов, т. е. отвода этих атомов в глубь металла. Чем выше концентрация диффундирующего элемента на поверхности детали, тем больше толщина слоя. Чем выше температура процесса, тем больше скорость диффузии атомов, а, следовательно, возрастает толщина диффузионного слоя.
Границы зерен являются участками, где диффузионные процессы облегчаются из-за наличия большого числа дефектов кристаллического строения. Если растворимость диффундирующего элемента в металле мала, то часто наблюдается преимущественная диффузия по границам зерен. При значительной растворимости диффундирующего элемента в металле роль пограничных слоев уменьшается. В момент фазовых превращений диффузия протекает быстрее.
|

Неорганические материалы
К неорганическим полимерным материалам относятся минеральное стекло, ситаллы, керамика и др. Этим материалам присущи негорючесть, высокая стойкость к нагреву, химическая стойкость, неподверженность старению, большая твердость, хорошая сопротивляемость сжимающим нагрузкам. Однако они обладают повышенной хрупкостью, плохо переносят резкую смену температур, слабо сопротивляются растягивающим и изгибающим усилиями имеют большую плотность по сравнению с органическими полимерными материалами.
Основой неорганических материалов являются главным образом оксиды и бескислородные соединения металлов. Поскольку большинство неорганических материалов содержит различные соединения кремния с другими элементами, эти материалы объединяют общим названием силикатные. В настоящее время применяют не только соединения кремния, но и чистые оксиды алюминия, магния, циркония и другие, обладающие более ценными техническими свойствами, чем обычные силикатные материалы.
В группу неорганических полимеров входит также графит. Неметаллические материалы подразделяют на графит, неорганическое стекло, стеклокристаллические материалы — ситаллы и керамику.